
by ROB SIMON, Columbus Place Finish Lead | March 14, 2017
Rob Simon is a finish lead at Lithko Contracting, a full-service concrete contractor based in Ohio. Here, he talks about tackling high tolerance floors, which require a different technique to conventional slab placements.
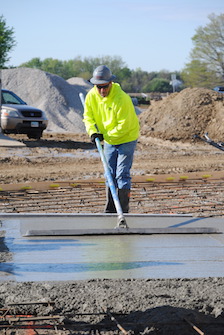
Warehouse projects are one of Lithko’s largest market segments, and one of the biggest challenges is creating a high tolerance floor. Super flat floors are mostly used in warehouse settings that have narrow aisles and high racks or automated material handling to store and retrieve products. These high tolerance floors allow for higher productivity when it comes to transporting products in and out of the facility.
In conventional slab placements, the goal is to place large square footages of slab in an efficient manner with the manpower and materials available. The place and finish team will use conventional machines, such as the laser screed, to aid in placing the concrete. For a high tolerance floor, the approach is a little bit different.
At Lithko, we routinely place slabs ranging from 40,000 to 60,000 square feet at tolerances well above specification requirements and have won concrete industry awards for Flatness and Levelness. Instead of placing a large area at once, the total package team will set forms for 14- to 16-foot aisle ways.
During this process, the carpentry work has to be very precise to ensure the best formwork is in place for the concrete. When placing, the team will use a crank screed to place the concrete and use a check rod to ensure flatness. Once the machines have been run, they will use a scrape rod to cut the highs and fill the lows, which guarantees that the floor is as flat as they are able to make it.
Once the concrete is cured, an independent company comes in to test for tolerance. In a regular slab placement, they use an F meter to measure horizontally and vertically across the entire slab. In a strip placement, they run chalk lines down the aisles to mark the wheel path of the fork truck. They then run the dipstick along the chalk lines. If any high spots remain, the team must grind them smooth. The tools used only allow for a tolerance thickness of 3 sheets of paper, which presents an additional challenge.
On our projects, our teams set the goal at this bar — we want to avoid having spots to grind. At a Macy’s distribution center in Remington, WV, we poured a high-traffic bay that was 50 feet across. Lithko used a traditional laser screed approach and through our precise carpentry and place finish methods, there was only one small spot to grind.
More recently, in a limited distribution center in Columbus, OH, the team strip poured 17,000 square feet a day, for a total of 220,000 square feet. Again, we set our sights high, and it paid off — we completed the job with only three 12-inch spots to grind.
Lithko is currently looking to fill several open positions through the BuiltWorlds Job Board. For more on the company, click here.
Discussion
Be the first to leave a comment.
You must be a member of the BuiltWorlds community to join the discussion.