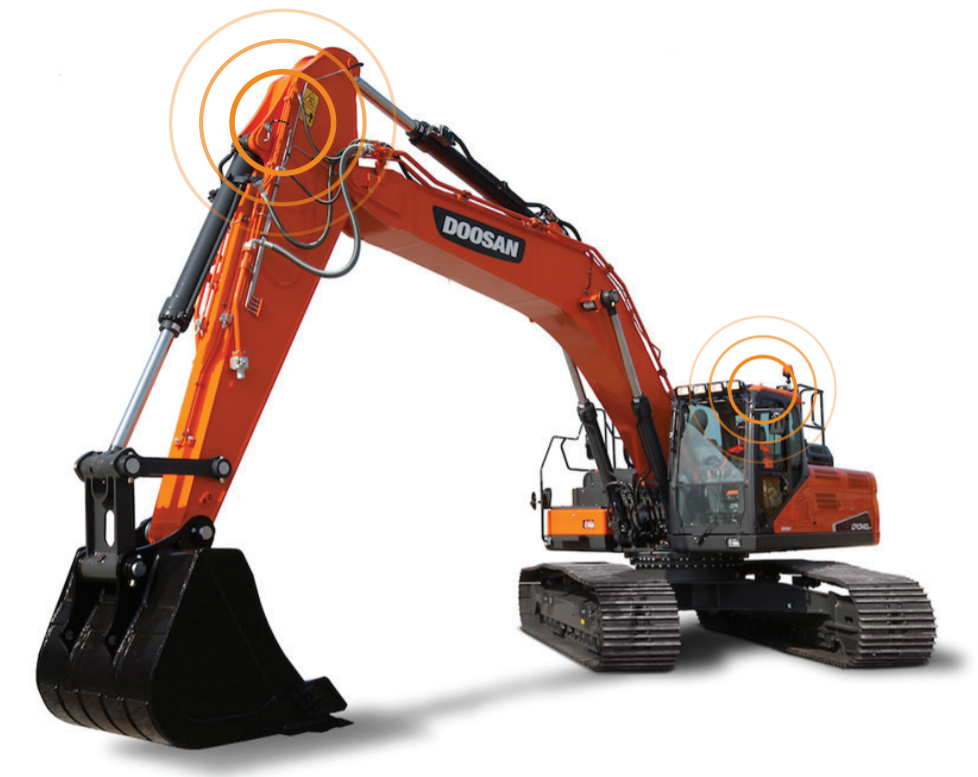
Downtime is costly. Tool are becoming more and more specialized on jobsites. Different metrics pertain to maintenance, utilization rates, and equipment health. On February 24 at 10 am CT, join EquipmentShare and Trackunit as we dive into how these digital connectivity tools are used to improve the utilization rates of all machines to eliminate downtime.
Join Willy Schlacks, President & Co-Founder of EquipmentShare, and Jeffrey Cohen, President of Trackunit, and as we explore how digital tools are connecting all aspects of jobsites into a single, manageable platform, giving you greater control and focus on your projects. Learn best practices across the industry on how these tools are used with OEM, rental, and owned equipment.
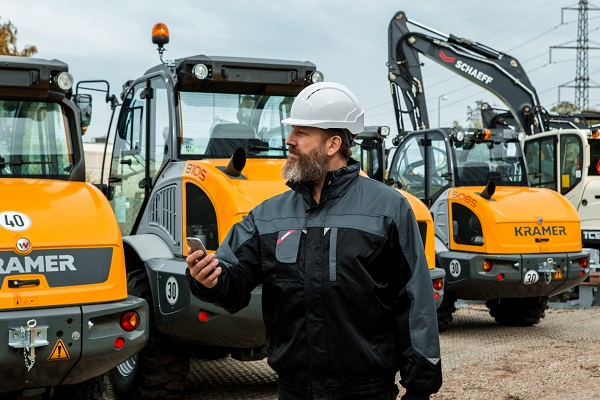
With the goal of eliminating downtime by 2025, Trackunit is challenging the status quo by creating services that connect the entire ecosystem within construction. Trackunit has partnered with Mortenson in the past, providing smarter ways to manage tools and maintenance. Telematics enables the user to detect and collect incredible amounts of data. Trackunit helps to put these insights to manage assets better through technology that’s changing the future. Downtime is missed revenue, lost profits, and broken promises. Learn how Trackunit plays a great role in the solution!
From Trackunit
As the construction industry continues to become more digital, Trackunit is connecting all aspects of jobsite. From OEM to rental to owned equipment, see how Trackunit is giving visibility into utilization of all machines and tools and continuing to Eliminate Downtime.
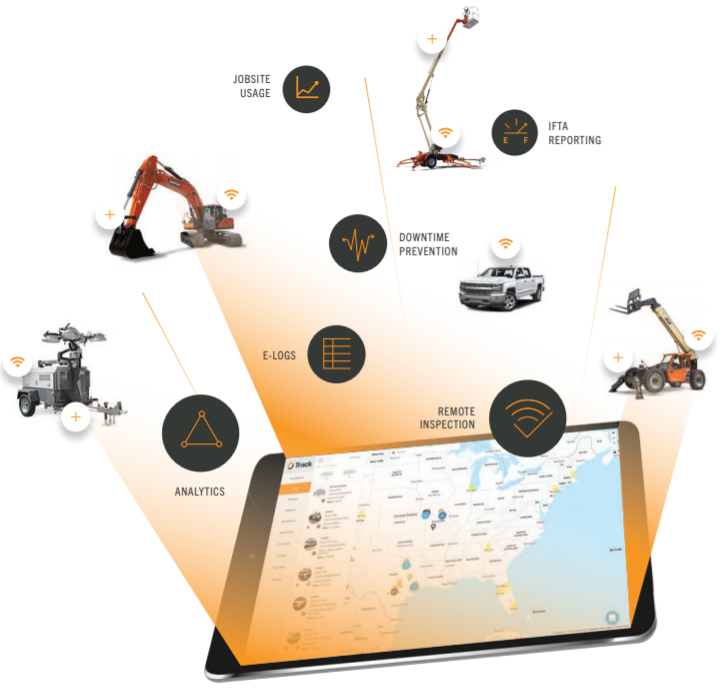
EquipmentShare is a nationwide construction technology and equipment solutions company on a mission to change construction through its cloud-powered platform of fleet management. EquipmentShare’s fleet management technology is OEM-agnostic, tracking any equipment to monitor machines, tools, materials, and people.
From EquipmentShare
EquipmentShare’s customer, a $4 billion construction company with 3,500+ employees, aimed to establish connectivity and transparency across their multiple assets, jobsites and facilities and employees. Their goal was to ensure they knew where each equipment asset was located at all times, in addition to tracking its maintenance history and upcoming service needs. The customer also needed a solution to achieve these goals while simultaneously working with several other legacy software systems the company had used for years. It was a priority to have uninterrupted business operations, and the tracking solution needed to integrate with their existing software systems. EquipmentShare implemented its fleet management technology solutions with the customer and successfully integrated them to work in the background of the customer’s five other software systems to funnel the utilization, health and GPS location data of nearly 2,000 tracked assets into one single data lake. The data could be accessed by anyone across the company from an internet-connected device. This technology integration also digitized the customer’s manual service and maintenance methods to increase efficiency, communication and productivity. Currently, the customer is tracking 1,700 assets with EquipmentShare’s technology with a goal of adding EquipmentShare’s tracking hardware to 15,000 more assets over the next several years. Additionally, the customer’s maintenance is now performed using a digital work orders tool and is accurate based on data pulled directly from the customer’s mixed fleet. The customer has also saved hours each week that were typically spent locating downed machines, driving to jobsites to diagnose service and miscalculating maintenance plans. The customer will now be able to bid more aggressively using accurate data gathered in a central location by EquipmentShare’s tracking hardware.
This Week’s Discussion: How Fleet Management Technologies Improve Productivity
This week learn from EquipmentShare’s Willy Schlacks (President) and Trackunit’s Jeffrey Cohen (President) as we dig into how to best manage assets on a jobsite. Explore construction technologies and what it means for the present and future. Times are changing – fleet management synthesizes more data than before. This provides an opportunity to not only monitor productivity and flexibly plan out sequencing but also predict usage rates on future projects.
Knowledge is Power – Use Equipment Data and Platforms to Become Agile and Efficient
New technology ecosystems are enabling those within construction to better keep promises, deadlines, and budgets by making better use of asset management.
Discussion
Be the first to leave a comment.
You must be a member of the BuiltWorlds community to join the discussion.