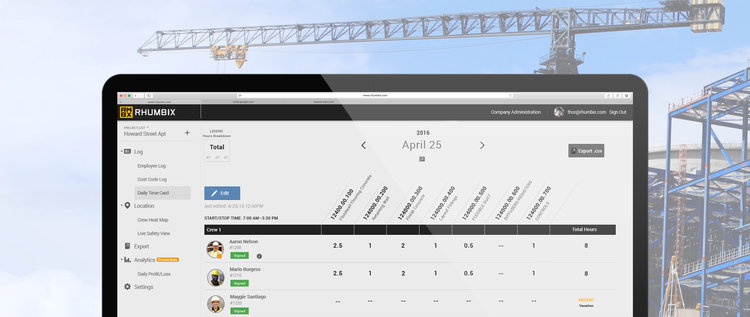
Construction lags behind most sectors when it comes to information technology spending. But changing from manual, paper-based processes to digitization isn’t as simple as flipping a switch — how do we move away from legacy systems and determine a clear return on investment?
The Case for Change
A number of recent reports from sources including McKinsey, the World Economic Forum, and KMPG have focused on the persistent problem of construction productivity, where the reliance of non-digital processes is often cited as a root cause. Paper-based data takes a long time to collect, requires significant resources to enter into management systems, and is often rife with errors and inaccuracies.
Perhaps the biggest challenge with paper processes is that the data just never gets used. How frequently are daily reports, which contain significant data on jobsite experiences and occurrences, ignored until they are needed to defend a claim or support a notification of change?
Consider timekeeping and daily reports. Your teams spend valuable hours creating timecards in the field, communicating that data back to the office, and payroll spends time fixing errors and guessing at entries. Data can take days before it is accessible in your systems, diminishing the opportunity to question the information and make corrections. Daily reports that contain critical contextual information on how your operations are performing, what needs to be changed, and lessons learned are infrequently recognized and shared.
“Most executives say their organizations are held back by manual processes and multiple systems. ”
Improving Data’s Quality, Usefulness
Compared to many technology developments in construction, including drones, robotics and BIM, improving how field data is gathered seems much less exciting. Without this data, however, benchmarking and measuring the innovation ROI becomes challenging, which impacts adoption of technology by the industry.
In the tight-margin business that is construction, we need to measure more reliably and consistently, and with fewer resources to empower innovation in our industry.
“Although mobile technology has huge potential for construction projects, less than 1/3 say their organizations use it routinely, and a similar proportion have no mobile platforms.”
3 Things to Consider when Adopting New Technology to Improve Data
1. Embrace cloud based software solutions for data collection and measurement: Cloud based SaaS solutions have become significant in many industries but are still finding their role in construction. On-premise software has been the primacy in the construction industry for years, but much of the data that the industry needs is gathered from jobsites, where the flexibility of mobile solutions makes adoption obvious. Cloud solutions are secure, scalable, rapidly deployable, and, more often than not, optimized for mobile devices, delivering a better user experience.
2. Look for software platforms, not point solutions: From drawing management to collaboration and task management, construction teams can choose from a vast array of apps and software to help manage operations in the field. There is a significant risk that a jobsite IT deployment made up of a myriad of point solutions will overload your field teams. To achieve maximum output from a minimal number of applications, these platforms should be:
- Compatible with (and leverage,)other software programs in use in the industry
- Mobile-ready to allow remote access from the field
- Intuitive and appropriately designed for use by your crews
Procore Connect is a good example of one such platform.
3. Challenge Software Vendors: Software providers are both part of the problem and the key to the solution. The construction industry must demand better operability from software tools and more intuitive and attractive software designs. Solutions that are designed for the office often don’t translate well into the field, despite being mobile-ready offerings. Cloud based tools are not inherently sticky, like on-premise solutions. The industry has amazing buying power — don’t be afraid to use it!
Discussion
Be the first to leave a comment.
You must be a member of the BuiltWorlds community to join the discussion.