What are drones?
Unmanned aerial vehicles, otherwise known as drones, are a cutting-edge technology tool that improves the process of gathering data on a construction site. As the name implies, drones are unmanned vehicles that can fly over and capture images of jobsites.
Drones are made up of two major parts — the drone itself, considered the platform, and the payload, which in the case of image capture drones, is the camera attached for capturing the image of the construction site.
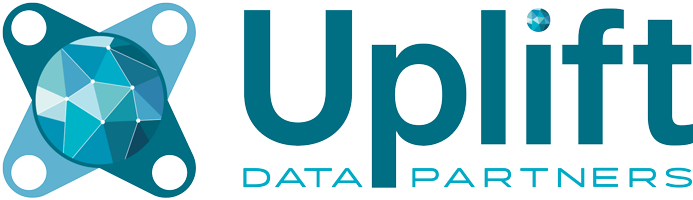
Drones are used where traditional methods of image capture is risky, inefficient, or expensive to use manned aerial vehicles such as helicopters or planes.
The full economic benefit of savings and efficiencies of drone captured imagery can be achieved when a company can find a drone solution that manages the logistics of drone flights, pilot certification, and analysis of the images that are captured by the drone. There can also be added benefit when a drone company (such as Uplift Data Partners) understands the construction industry and its needs.
Case study: Using drones to reduce costs on a jobsite
The typical approach to monitoring aggregate movement has been a reliance on the site supervisor to monitor the number of trucks moving on and off the job site and comparing this to the invoices. Payments are made based on the counts/monitoring that the site supervisor maintains.
This process is complicated by site haul-offs, as heavy traffic leads to miscounts, misplacement of aggregates, and waste. An added layer of complexity is involved when the subsurface geology is environmentally harmful or dangerous.
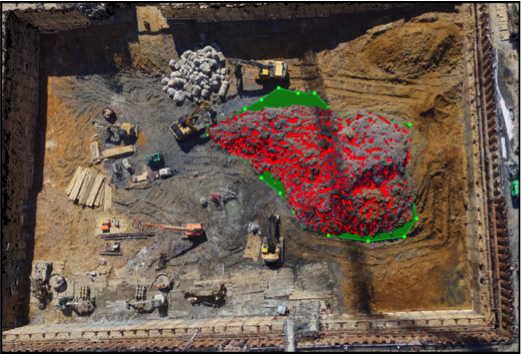
On one particular jobsite (pictured above), the movement of the environmentally dangerous haul-off found on the site, “blue marl” soil, was to a separate landfill from the rest of aggregate waste haul off.
A combination of truck types — tandems, tri-axles, quad axles, and centipedes — by the haul-off contractor complicated the site supervisor’s tracking of the process.
The contractor was billing a flat rate of 9 c/y per truck even though each truck had a different capacity. This made calculating the truck counts and haul-off volumes difficult and led to increased costs, because traditionally, the data would have been captured using daily counts managed by the site supervisor.
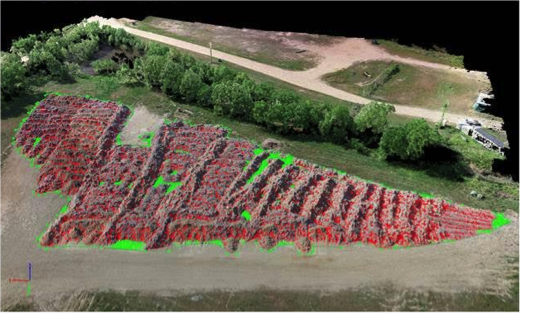
The process, however, was improved by capturing the measurements using drones.
To improve the truck count and haul-off volume calculations, Uplift Data Partners deployed drone pilots to fly the dump site and capture images of the site stockpiles.
Upon analysis of the images, an equitable rate/truck type could be determined. Uplift’s drones were able to fly, process, and calculate the volumes in 24 hours, resulting in a cost savings of $32,940 — far and above the cost of deploying the drones and getting the images analyzed.
Click here to learn more about how drones can improve efficiency and cost savings on construction sites.
This article was sponsored by Uplift Data Partners.