Environmental impacts of the construction sector are well known. Its estimated contribution of 40 percent of the global CO2 emissions annually is reported often.
Unfortunately, despite the growing awareness of the sector’s climate impact, measurable change has occurred at a glacial pace. The Economist even gloomily declared in 2022, “The construction industry remains horribly climate-unfriendly.” This presents both a continuing challenge and an important opportunity, as decarbonizing the construction sector could significantly improve climate outcomes and enhance global sustainability for everyone.
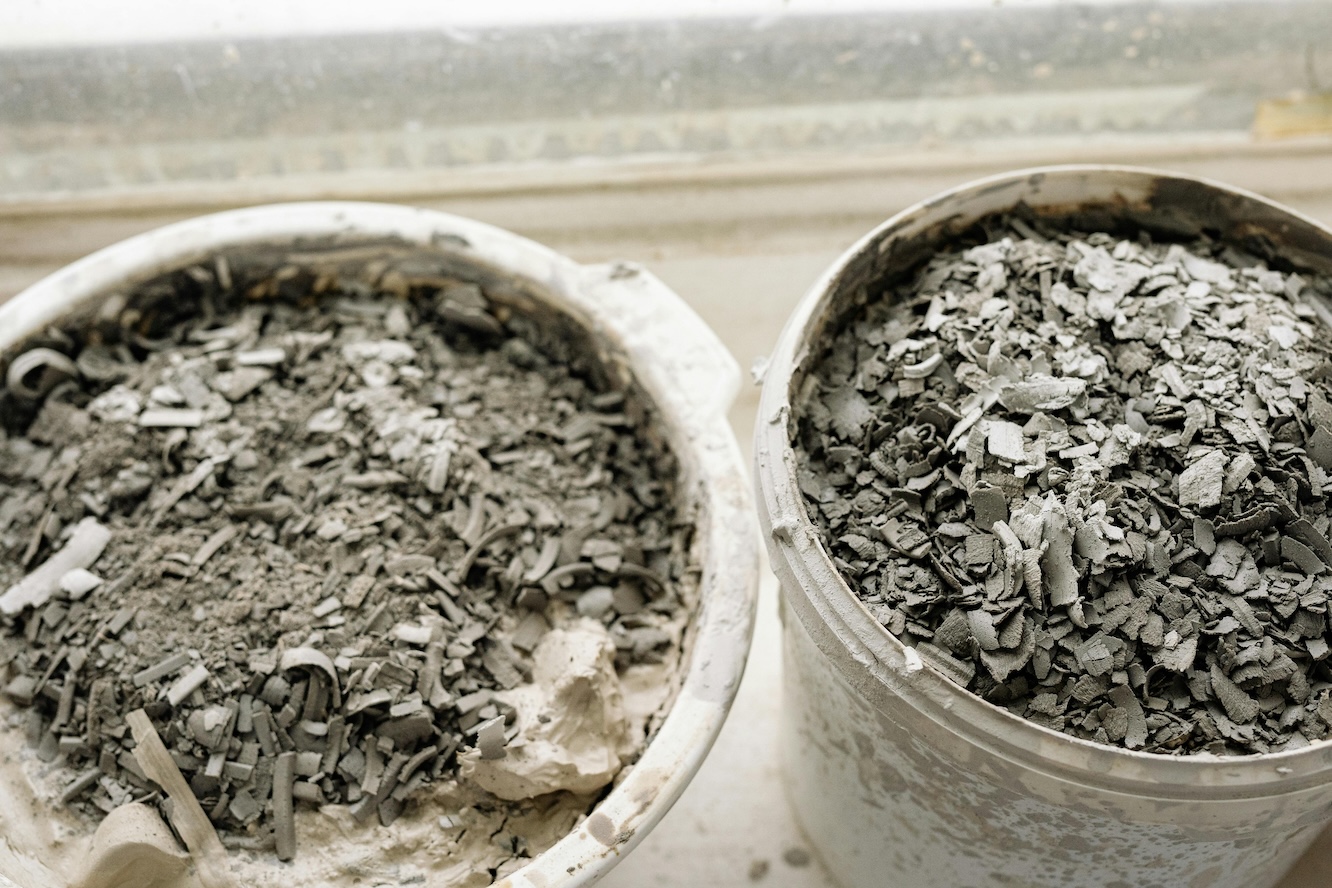
That pace of change must pick up as pressure grows for design, engineering, and construction companies to pursue net-zero emissions and minimize their carbon footprint more quickly. According to one industry survey, 90 percent of US engineering and construction companies “receive requests from customers to lower the amount of embodied carbon used in construction projects.” And, to be fair, some of those companies are answering the call, pursuing LEED v4.1 certification as a part of a strategic effort to reach carbon neutrality.
Another useful tactic to help bridge the gap between demand for sustainability and measurable change is implementing a robust Construction Waste Management (CWM) Plan. According to the EPA’s most recent report, more than 600 million tons of construction and demolition debris are generated annually in the United States alone. Here are five steps construction companies worldwide can take to curb waste and be more environmentally conscious.
1. Anticipate and Address Common Roadblocks
Proactive waste management helps achieve LEED waste credit and cultivate a sustainable construction process. The most common roadblocks include:
- Lack of planning
- Inaccessible local markets for waste
- Not knowing what waste types local haulers will take
- Assuming that a certified facility is required
- Not managing the site to prevent contamination of dumpsters.
For example, interior general contractors working in tightly packed urban environments can find the roadblocks to better waste practices seemingly insurmountable. However, working with the owner and design team early in the construction process can uncover challenges and help define integrative solutions to implement before the design is finalized.
According to Michael Orbank, a sustainability manager for Structure Tone (part of the STO Building Group) responsible for many projects in Boston, “The roadblocks of tight urban sites, cramped project boundaries, and freight elevator woes abound. However, recognizing these roadblocks early in the project lifecycle and collaborating with the project team on carbon goals and removal logistics, turn many of these formidable challenges into innovative process changes.”
Early communication with architect and engineering teams is key, allowing everyone to ask the important questions, and leverage data and timely insights to achieve compliance.
2. Create a Construction Waste Management (CWM) Plan
A CWM Plan is a proactive measure for reporting on waste diversion activities, outlining specific details of waste management throughout the project lifecycle. It starts with identifying the various waste streams produced during construction before providing estimates of the total waste generated and the proportions expected to be diverted from landfills.
Within the CWM Plan, the targeted markets for diverted waste materials are specified, ensuring there is a clear understanding of where the materials will be sent for reuse or recycling. It also details haulers capable of meeting the stringent requirements of LEED, including their processes for weighing and documenting source-separated waste streams to enhance recycling efforts.
Simply put, a CWM Plan is a blueprint for responsible waste management that aligns with the LEED certification goals.
By reviewing the project schedule and understanding when typical waste streams are being created, a carefully developed and properly communicated CWM Plan allows for field team buy-in and baseline comparisons during and after implementation.
“Construction waste management plans need to stop being seen as boilerplate and start being seen as opportunities for decarbonization and waste diversion,” added Orbank. Structure Tone took this approach, following a CWM Plan that estimates when each source of waste is expected and provides for its timely removal and separation from other waste sources. Overall, this has reduced commingled hauls on LEED projects with little to no added cost.
3. Understand Your Hauler Process
Understanding the intricacies of your hauler’s process is critical for efficient construction waste management and achieving minimum goals. This includes understanding the hauler’s techniques for tagging dumpsters, methods for weighing and documenting separated or commingled waste streams, and identifying haulers and recyclers proficient in processing.
Once again, collaboration is key. Having a constructive dialogue with haulers and recyclers allows you to pinpoint inefficiencies or areas ripe for enhancement and discover potential innovations.
These entities should document the diversion rates of source-separated materials and maintain a minimum commingled facility average recycling rate of 75 percent. This knowledge and collaboration are fundamental to optimizing waste management and advancing eco-friendly construction practices.
Notably, you don’t need a certified facility. Achieving a diversion rate of 50 percent or more through a Recycling Certification Institute-authorized facility marks a meaningful accomplishment in sustainable waste management; however, such certification is not a prerequisite for earning the two points for Construction Waste in a LEED project.
4. Communicate and Educate
A developed CWM Plan only goes so far if the field team isn’t brought into the process. Effective communication and ongoing education are fundamental to the success of any waste management plan, especially for achieving credits in sustainable practices.
Regular interactions with on-site personnel are necessary to highlight the importance of their collaboration in obtaining the desired credits. Communicating changes to C&D waste practices is vital to moving the needle toward waste reduction and landfill diversion. Additionally, clear and readable signage in the languages understood by the workforce is vital to guide them in proper waste segregation and disposal.
Structure Tone found that simple educational meetings during project kick-off and short monthly check-ins (which can be combined with LEED IAQ inspections) allow for transparent communication and CWM Plan success. Orbank noted that “By training field staff, collecting feedback on implementation improvements, and sharing it all with the project team, Structure Tone was able to implement site separation programs on five new sites in 2023.”
5. Track, Report, and Evolve
Of course, understanding the data is crucially important. Efficient tracking and reporting are needed to develop monthly CWM Plan performance assessments. Proper collection to ensure accurate and consistent data—in terms of pounds per square foot or diversion rate—must be planned into the process.
It is important to note that these regular assessments also can help determine whether to pursue LEED v4 or v4.1, with the flexibility to opt for v4.1 on a credit-by-credit basis. At completion, a comprehensive final waste report also is necessary. This report details the total waste, landfill, and diversion amounts, stipulating that calculations—whether by weight or volume—remain consistent throughout the duration of the project.
Along the way, Structure Tone has continued to dig deep into the data to understand where waste is going and how it is being generated to ensure future hauls and projects can reduce and divert as much waste as possible. The details are crucial to discovering what works, what needs to be changed, and which long-held industry practices could need updating.
While general contractors “typically receive waste reports and push them through without scrutiny or comprehension of the data,” Orbank reports that “Taking time to fully understand these reports clarifies our impacts on the process, and Structure Tone is now using our waste data as a baseline for improvements and a reference point on what isn’t working.”
With new LEED standards coming soon, companies will need to continue to evolve their on-site practices and LEED reporting protocols. The right data will make this process easier and, ultimately, help sustainability leaders like Orbank inform the industry about what “better” waste practices should look like.
Better Waste Management Betters Businesses and the Environment
Reducing the built environment’s substantial carbon footprint represents a significant step toward limiting the negative climate impacts of construction. It’s an expansive challenge that requires all stakeholders to make a positive change but promises a significant return on investment for businesses and communities that embrace it, differentiating future-focused companies from those refusing to move forward.
For construction companies, implementing a thoughtful CWM Plan is an excellent place to start mitigating the negative effects of building byproducts, and following these five steps should make that process easier.
About the Author: Tommy Linstroth is the Founder and CEO of Green Badger, a leading SaaS provider simplifying sustainability, LEED, and ESG in the built industry.
Discussion
Be the first to leave a comment.
You must be a member of the BuiltWorlds community to join the discussion.