Paracosm’s Rubin (left) and modular maestro Krulak both spoke at our CEO Forum last spring.
They met a year ago at the first BuiltWorlds Summit. And now, as a result, our industry may soon reap the benefits.
Last April, Paracosm CEO Amir Rubin had just spoken onstage about his Gainesville FL-based firm’s 3D mapping capabilities that use hand-held laser scanners on jobsites via tablets with scanning apps. “3D-mapping and AR will bring new levels of quality control to work sites,” he said. “Stakeholders will be able to visualize and verify work in place throughout the project lifecycle to ensure safety on the job site, and that the as-built matches the design.”
In the crowd and impressed was Roger Krulak, the builder responsible for B2BKLYN, which at 32 stories would become the world’s tallest, multifamily, modular high-rise when it opened last fall in Brooklyn NY. Krulak was most impressed with the potential applications for modular construction that he envisioned for the Paracosm technology that Rubin, himself, had not yet contemplated. As luck would have it, their two seats were next to each other in the audience, so the two got to talking, and they hung out together after the session. Later, they carried their conversation with them to dinner.
- This year’s BuiltWorlds Summit is only a week away! Got tix? Learn more here.
“I found Amir’s presentation super-interesting, and I thought it had some real possibilities for modular manufacturing,” recalls Krulak. The more they talked, the more excited they became about a potential partnership they saw forming focused on one simple idea.
“Essentially what we are talking about is projection mapping that can project, say, wall framing onto a framing table,” says Krulak. Adds Rubin, “But it is so metrically accurate that you can use it for actual measurements. Using all of our 3D expertise, we’re effectively projecting the blueprint onto the table.”
By eliminating the back and forth with tape measures between field and factory, Krulak and Rubin estimate the process could save 25-30% on labor costs for fabrication and installation. The idea is to inject so much more accuracy and precision on the front end that it removes rework on the back end.
“Projection mapping has been used before elsewhere, but this is the first application that I am aware of in construction, and certainly for modular work, where it is used for actual measurement,” notes Rubin.
After the BW event last April, the pair went back to their respective East Coast workplaces, but they kept in touch, and Rubin even brought his team to NYC to view Krulak’s Brooklyn Navy Yard manufacturing facility. Last fall, once Krulak formally acquired the modular capabilities of his former employer, Forest City Ratner, he turned to Rubin to put pen to paper and formalize their own partnership.
Now, the two are excited about the months to come. “We are testing the technology and making it flexible enough to adjust accurately to the table size and to the depth of the table,” explains Krulak, now CEO of Brooklyn-based Full Stack Modular. “We are set to go ‘live’ with it now by the end of May. ”
Does the new technology apply equally well to non-modular construction?
“Sure it does, so we intend to market it beyond modular, as well,” adds Krulak. “We’d be crazy not to.”
Stay tuned, world. Who knows what else these two will come up with in the days ahead? And remember, it all started at the BuiltWorlds Summit.
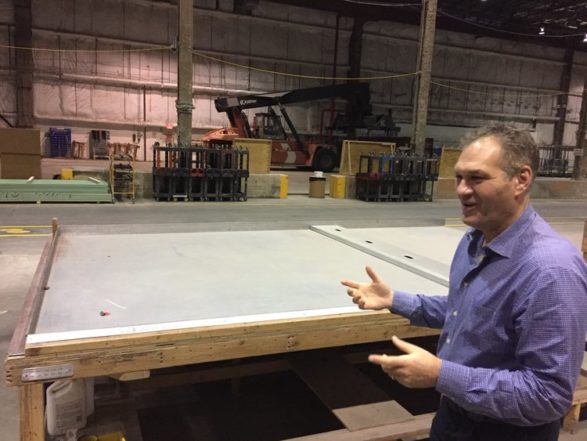
Discussion
Be the first to leave a comment.
You must be a member of the BuiltWorlds community to join the discussion.