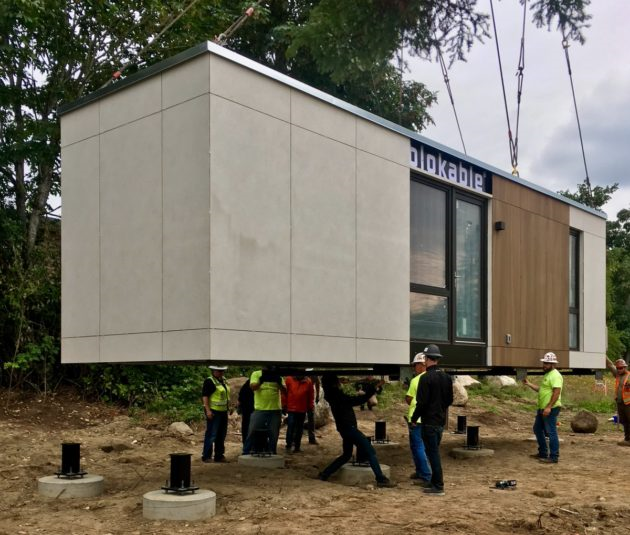
Moving construction from jobsites and into factories can have a significant impact on how we build. Join us on Day 3 of the 2021 Building Conference as we discuss modularization and prefabrication with Christopher Sharples (SHoP Architects), Britton Langdon (MSuite), Aaron Hold (Blokable), and Chris Mortenson (Modulous).
Modular building is a prefabricated process consisting of repeated sections called modules. Modular construction must be considered in all stages of a project’s lifecycle – from design to building erection. The key benefits to modular construction lay in reduced on-site production times, leaner supply-chains, and limiting redesigns. At scale, this has the potential to reduce construction costs by 20%.
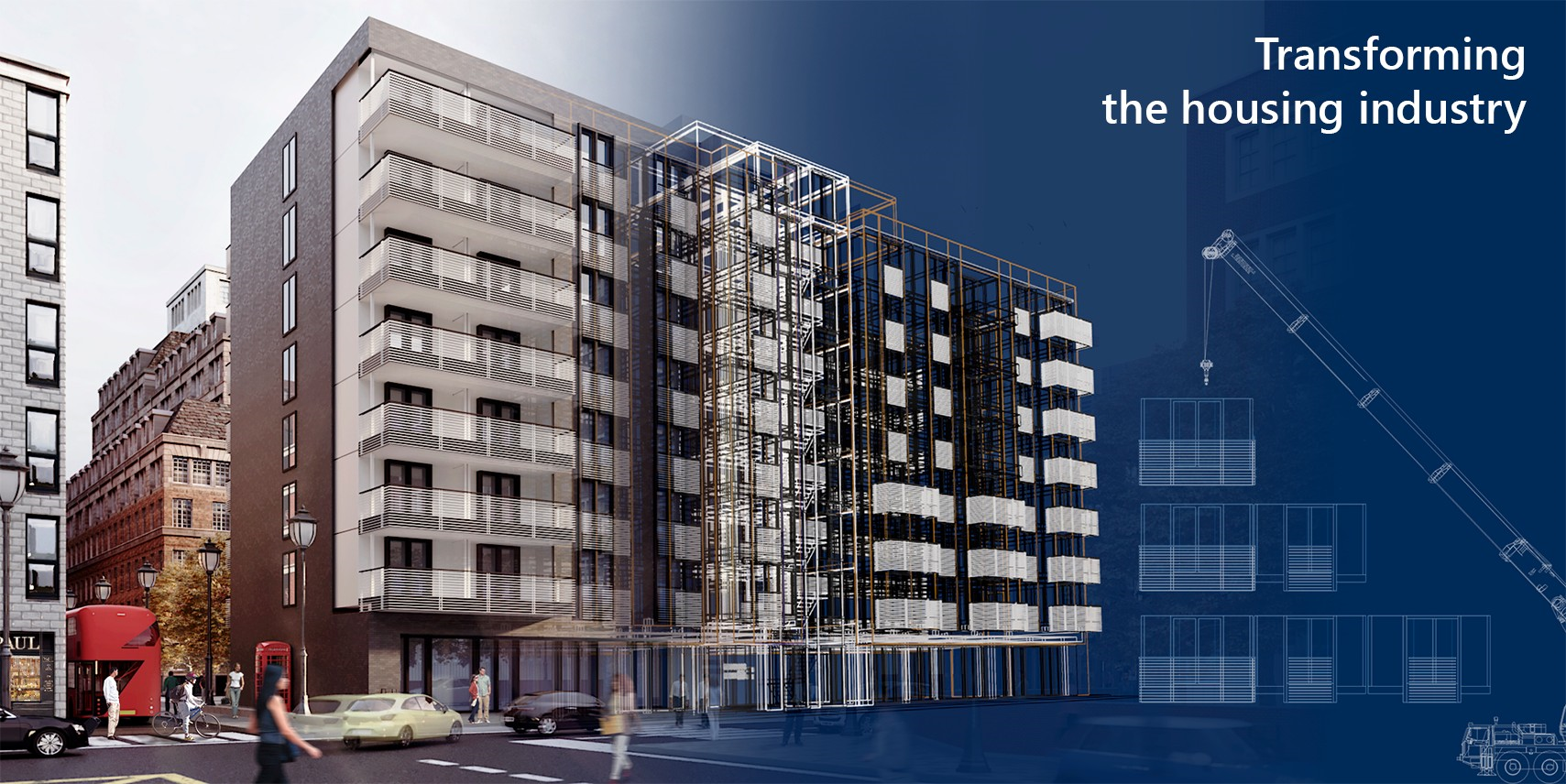
Fabrication, construction, and building erection can all be sequenced simultaneously for shorter project timelines as well. In fact, modular construction projects finish twice as fast, on average, compared to traditional construction techniques. Once on the jobsite, the reduction in customization, complexity, and RFIs allow construction workers to set modules in place, then lock them together to create a seamless building.
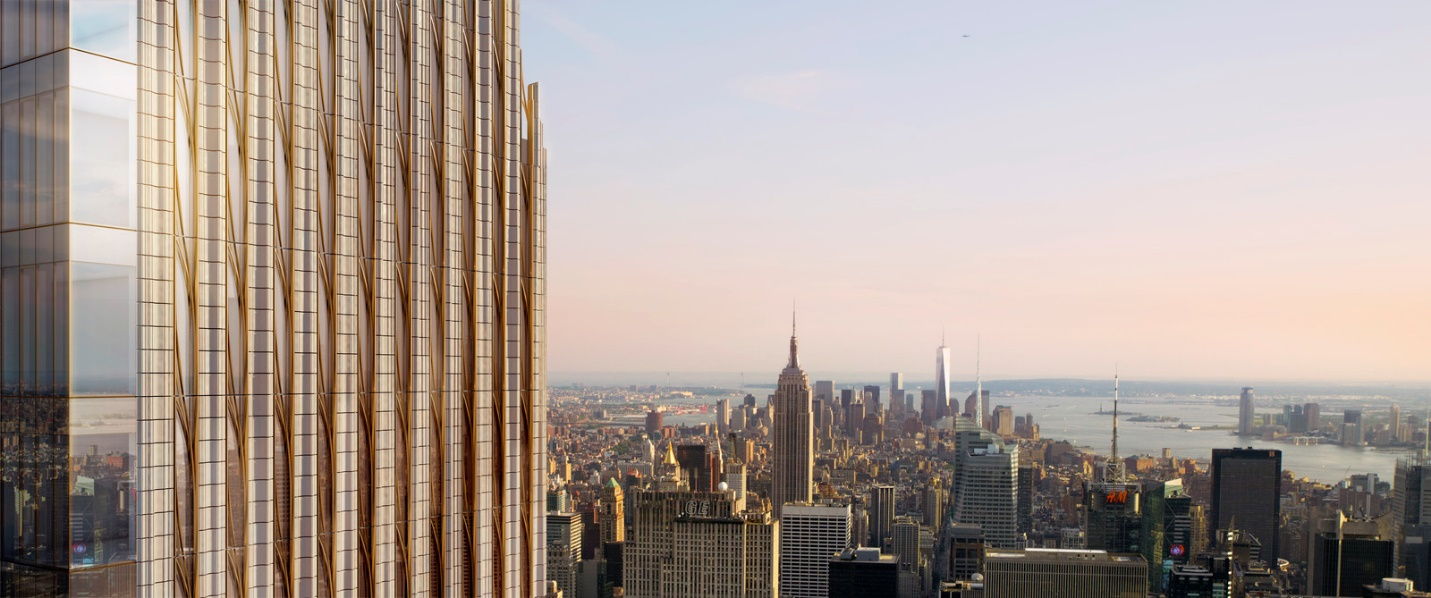
Modularity Must Be Considered from Design to Construction
Modular construction is optimized when considered throughout the project’s lifecycle. This starts with architects and engineers in design. Next, it moves towards fabrication with manufacturers optimizing supply chains to align with project schedules. Finally, all logistics must be managed from jobsite delivery to construction.
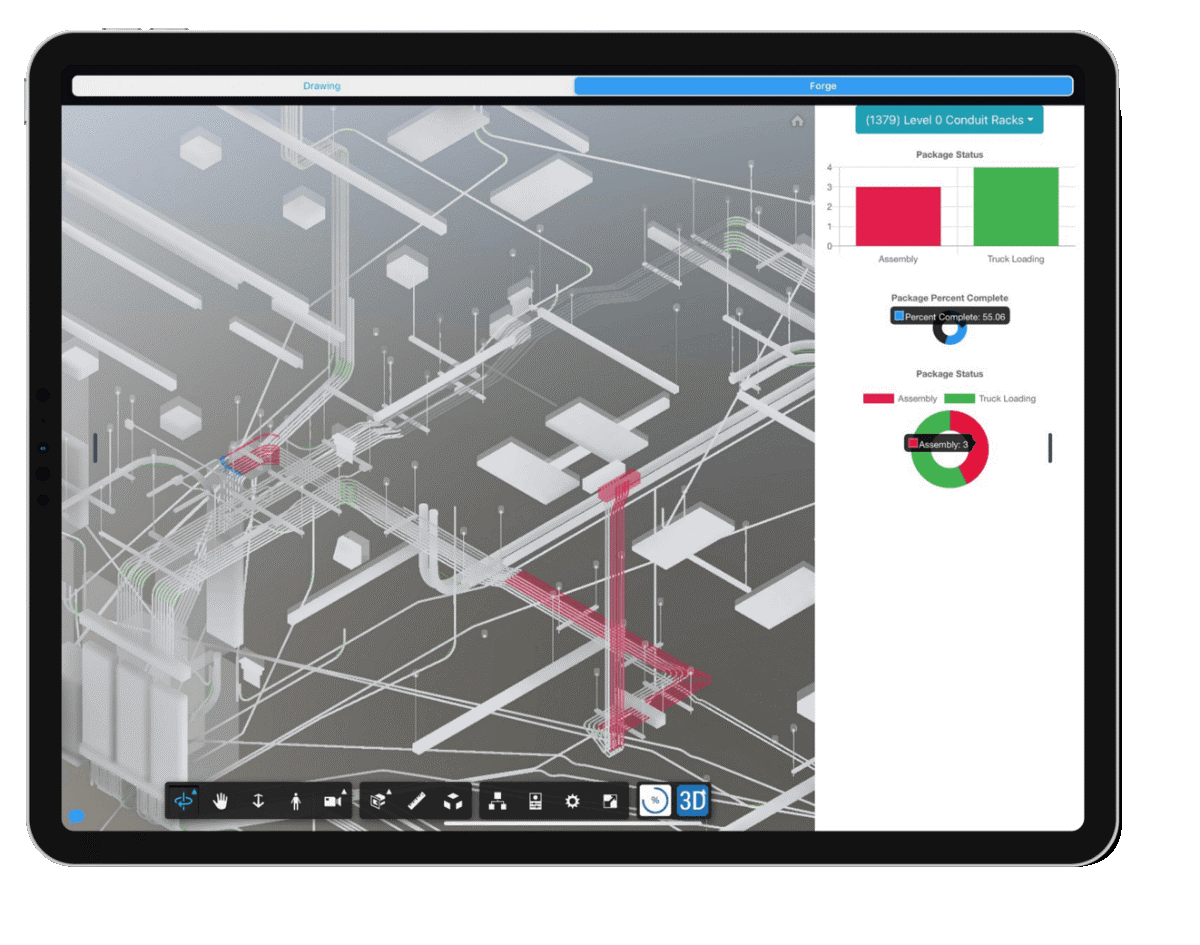
Modular Design, Supply Chain, & Jobsite Logistics
SHoP Architects is an award-winning architecture firm based in New York City advocating new practices for sustainability, equity, and inclusion for the design of public and cultural spaces for communities. Discussion led by Christopher Sharples, Founding Principal.
MSuite is a management platform suite for construction to better track, manage, and share KPIs to improve productivity, status, and health of projects throughout the lifecycle. Discussion led by Britton Langdon, CEO.
Blokable reduces the cost and time to create and operate multi-family housing through offsite construction and prefabrication. Discussion led by Aaron Holm, Co-CEO.
Modulous is a digitally integrated process to enable the rapid design, assembly, and delivery of high-quality, affordable, sustainable smart homes. Discussion led by Chris Mortenson, COO.
Discussion
Be the first to leave a comment.
You must be a member of the BuiltWorlds community to join the discussion.