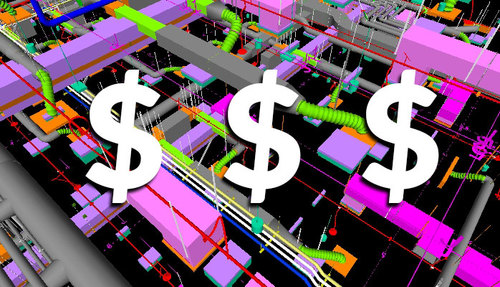
Who has time to innovate?
When the economy is chugging and so many projects are just out there for the taking, it’s only natural –especially in the AEC space — for firms to pursue work the same way they always have. “Sure, maybe the process is a bit broken, but I don’t have time to fix it…” seems to be the thinking.
In such competitive waters, new technology designed to improve old processes truly has to swim upstream, especially when breathless contractors are afraid to come up for air, much less learn or try anything new. Many designers are no more adventurous, content to give pseudo-savvy owners a more tech-filled proposal that they quickly dismiss after winning the work. As one veteran architect told the Chicago Building Congress earlier this fall, “Too often, technology still costs too much. How many projects are there still where you have these great, whiz-bang [BIM systems, but in the end, they went unused, left on the shelf?”
The tech didn’t really fail. Its benefits were just not seen as big enough to warrant the time investment to get over the learning curve. But what if the evidence was too overwhelming to be ignored? What if the potential savings in time and money were just so great that they could not be put off?

“Every project still relies on drawings, but the production of those drawings is still labor-intensive, and their coordination can take several months,” says Brett Young, founder and CEO of startup Building System Planning Inc., or simply BuildingSP. “With our new technology and tools, we can coordinate tasks like an individual mechanical pipe run in under a second, and entire building floors in just a couple of hours,” he claims.
Wait, what? Seconds? Hours? How?
“We are using algorithms to automate drawing production, so our tools are making people more effective,” explains Paul Cassidy, BuildingSP’s CTO. “The result is buildings that are more affordable, better performing, and that enable the use of more and more technology.”
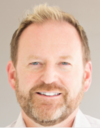
Specifically, the Emeryville CA-based startup uses heuristic algorithms and semantic ontologies to “teach” machines how to coordinate systems within BIM. (The firm’s slogan is Moving BIM Forward.) “We develop intelligent software,” adds Cassidy, who is an expert in algorithm development, with degrees in both electrical and computer engineering. “Existing planning software relies on manual input, multiple layers of coordination, and correction of all systems,” he says. “We use algorithms, automation and machine learning to achieve better solutions in faster time frames. We do clash-free routing of systems using rules and preferences.”

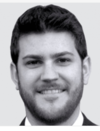
The initial technology implemented was framed on the doctoral work of Christian Van Der Velden, a Melbourne, Australia-based expert in advanced algorithms, artificial intelligence and “knowledge-based engineering”. Now a key member of BuildingSP’s initial six-person team, Van Der Velden had studied how to use algorithms to automatically route mechanical and electrical systems in aerospace engineering. But his PhD work uncovered broader applications in general engineering and he developed a significant code base that auto-routes using Visual Basic while communicating to Dassault’s Catia CAD software platform. BuildingSP has adapted significant growth to Van Der Helden’s work, attaching a re-written and expanded code base to Autodesk’s Revit BIM platform.
“We now have code that automatically routes building utilities in a data-driven way,” says Young, who holds a degree in civil and environmental engineering from UC-Berkeley. “Of the four major building systems, we are working on a complete solution now for electrical with a full release expected after the first of the year. Our goal is to transform BIM into a highly-automated practice that gives project teams sets of solutions and options which can be analyzed and evaluated.”
The idea is to do so quickly and early enough in the building process not only to head off potential problems, but also to change project procurement. “We’re dramatically shortening a high-value process at a critical point in the project life cycle — when there’s still an ability to influence the overall outcome of the building,” explains Cassidy. “Globalization of computer hardware started once they applied automation and intelligence to microchip design. That is exactly what we’re doing for the AEC industry.”
out of the trenches
CEO Young cut his teeth in the industry with Cahill Contractors, a San Francisco-based commercial builder for which he served nine years, rising to senior project manager for BIM implementation. In 2010, he left to start his own BIM consulting firm, Modulus Consulting, which soon developed a clientele among large contractors like Clark Construction, DPR, Skanska USA, Swinerton, Pankow, Whiting-Turner, and Webcor Builders. Many subcontractors, designers, and owners were also customers. The 278 projects that Modulus completed in Young’s five years there directly informed him of the specific solutions most needed in the field.
“There’s a huge need for more BIM staff,” says Young. “Our industry has gotten good at training and managing great BIM professionals. So the real opportunity now is to make their tools better and to enable them to improve the entire process.”
BuildingSP’s stated goal is to enable greater efficiency in design and construction. It aims to do so with tools that reduce workloads and leverage talents, qualities especially in demand in thriving markets with tight labor demand. As CEO and CTO, respectively, Young and Cassidy have also taken special care to balance their startup’s real-world industry expertise with that of the team’s mathematical and algorithmic strengths. Indeed, the team is split evenly between experts in artificial intelligence, algorithms, and large-scale CAD solutions, and AEC veterans with expertise in BIM and BIM coordination. In that way, the staff is an extension and reflection of its two leaders.
In the end, though, all are united by a common purpose.
“We like building things and we like helping people build things,” says Young. “We know both the pains and benefits of BIM firsthand. Reducing the pain so that we can fully realize the benefits is a fantastic challenge. We are very excited to be working on this problem.”
Indeed, Young, Cassidy, Van Der Helden, and their colleagues all believe the timing is just right.
“Construction is ripe for disruption,” says Young. “Stagnant labor productivity means that project stakeholders can’t realize efficiencies enjoyed by other industries. So, everyone in our industry has known for a long time that things have to change. We see enormous opportunity now for the use of intelligence and automation finally to enable that change.”
This week, the BuildingSP team is attending Autodesk University. For more on their solutions, click here.
Discussion
Be the first to leave a comment.
You must be a member of the BuiltWorlds community to join the discussion.