Featuring:
Project Details
The Exchange is a condominium building development and one of the first projects using Barton
Malow’s LIFTbuild technology, where structural components were assembled from the top down. This innovative approach involved lifting and securing floors and walls from above, markedly enhancing efficiency, safety, and reducing the overall construction time for this specific urban development project. The LIFTbuild process incorporates the use of core shafts, which are central structural elements essential to this innovative construction method.
These core shafts serve as the primary support structures around which the rest of the building is constructed. In the LIFTbuild approach, the core shafts are typically built using traditional construction methods, and once erected, they provide the necessary stability and framework for the subsequent top-down assembly of the building's floors and walls. Installing these shafts quickly was critical to ensuring the project remained on schedule.

Objectives
Barton Malow & Trunk Tools set 74 productivity targets in order to catch up and maintain the original project schedule and increase overall labor output. Some of the 74 goals included:
- Complete the floor plate on level 8 in 4 days vs 5 planned days for an incentive payout to the crew of $5,040
- Placement of slab on metal deck (SOMD) in 8 hrs. vs. 10 planned hours for an $840.00 incentive payout to the crew
- Install metal decking in 9 hrs. vs 10 planned hours for an incentive payout of $472.50
- Detail deck in 9 hrs vs 10 planned hours for an incentive payout of $682.50
- Unload shake out Sequences 1 and 2 in 4 hours for an incentive payout of $472.50
- Have all bolts installed in 9 hours for an incentive payout of $367.50

Outcomes
TrunkPerform helped to get The LIFTbuild portion of The Exchange project back on schedule and to reduce budget overruns by a substantial order. At a total cost of $28,500 for incentive bonus payments and administrative costs over the following weeks, Barton Malow was able to save over $194,000 dollars on this portion of the project. They also finished in 94 days, two days ahead of schedule, despite being 12 days behind at the midway point of the build. These impressive improvements resulted in over $6 in savings per $1 spent on the TrunkPerform solution. This also
translated to a rough cost of $1500 in incentives payments to remove one day off the project schedule during the structural steel erection phase.

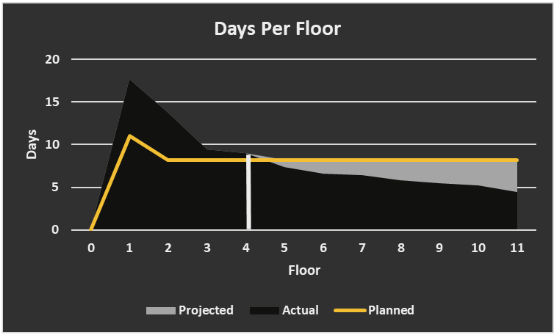
Next Steps & Future Use
N/A
BuiltWorlds Analysis
Per BuiltWorlds benchmarking data, 75% of construction companies are utilizing a Workforce Management solution in some capacity. While still relatively early in their overall maturity, technology solutions providing project teams the ability to better track, incentivize, and produce efficiencies are an increasingly powerful tool in the contractor's tech stack. Quality data indicates increasing functionalities and ratings across most categories, particularly in labor management and task tracking criteria