It’s pretty easy to guess what those in construction see in job-site robots such as SAM100 from Construction Robotics. Project managers likely see the potential for increases in efficiency while lower-level workers might see a labor competitor. But what do those in architecture see? How might construction robotics affect our ideas of building design?
To find out, we talked with Michael Silver, an assistant professor at the University at Buffalo who’s part of the Sustainable Manufacturing and Advanced Robotic Technologies (SMART) program funded by the school’s Community of Excellence. The interdisciplinary team of students and faculty—led by Kemper Lewis, chair of the Department of Mechanical and Aerospace Engineering; Ken English, the associate director; and Omar Kahn, chair of the School of Architecture and Planning—consists of building designers, computer scientists, economists, and industrial engineers who work together across disciplines to explore new techniques of making, including new ways of approaching the process of building design and fabrication. Among the projects it’s working on is a brick-hauling robot that could aid workers on job sites.
Silver sat down with us recently, after presenting at our “Rise of the Machines” conference back on April 6, to explain how architects have dealt with technological advances in the past, how he became interested in job-site robots, and where he hopes to take the robot he’s designing from here.
You work on robots for construction sites, but your background is in architecture?
I’m a practicing architect, but I’m also very interested in transforming the way buildings are made. By developing new robotic technologies that can operate in the field, I believe the designer can affect direct changes in the both the functional and aesthetic character of architecture. You can’t make a building without knowing what it’s made out of, and you can’t make it if you don’t understand how things go together. Using advanced systems to enhance quality and lower costs while speeding up production is important, but if architects participate in the invention of these new systems, then they can also better shape the future of built form.
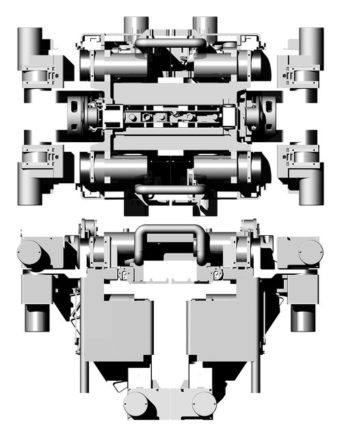
How can architects influence the way we think about robotics?
I think we are at a unique moment in history when it has become possible to dramatically alter the means of production. Designers have traditionally appropriated tools or used existing construction methods to shape the built environment. If you can collaborate with contractors and process engineers, then a whole new space of innovation opens up. Rather than simply retrofitting the end effector of an industrial robot arm, I think that we are now in a position to develop complete systems from scratch. If our team can work directly with laborers to construct novel hardware and code, then I think we’ll come up with stuff that is both practical and formally innovative.
How did you become interested in creating robots for construction?
As a member of SMART, I’m exposed daily to new ways of thinking about technology and how new discoveries in other fields can be applied to the problem of building. I often imagine, through my colleague’s research, novel ways of approaching the development of automated systems that can operate in conjunction with existing trades while enhancing productivity and alleviating the drudgery of dirty, difficult, dangerous work. Collaborating with SMART members has been a really eye-opening experience.
What’s the main objective of your current research?
The robot project we’re working on now is meant to foster a dialogue between SMART members and the building trades. More precisely, we are designing a leg-based hod carrier that will help masons transport heavy bricks across difficult terrain. I want to see how workers respond to this proposed tool and then adapt it to better fit their needs. The project is as much about engineering new machines, as it is a form of anthropological fieldwork sponsored by industry partners like the International Masonry Institute [IMI] and Construction Robotics. In the end, we really want laborers to eagerly embrace what we build for them. Getting early input on our work from a master mason is absolutely essential. As Louis Kahn said, “Listen to the people who work with their hands.”
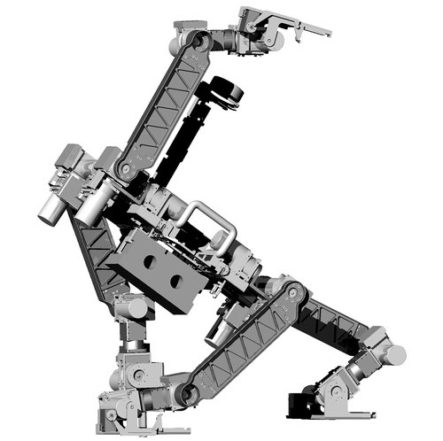
Talk a little bit more about the robot you’re designing and what you hope it will do.
The current machine we’re building is the fifth in a series of On-Site Construction Robots, or OSCRs. OSCR-5 was nicknamed by one of my students “The Folding Humanoid.” It’s a bipedal machine that collapses into the form of a compact toolbox. I think this device will help break down the fears workers have of autonomous systems, which sometimes reminds them of those metal monsters in movies like The Terminator. If you can pick up a tool, control it with augmented reality goggles, and relieve your aching muscles by letting it carry heavy payloads, then it becomes a useful extension of the body.
How have your collaborators helped with the project?
Professors Nils Napp and Karthik Dantu at UB’s Department of Computer Science, along with Scott Peters from Construction Robotics, provided us with a roadmap showing how to navigate the technical challenges of actually building a machine. Dave Sovinsky at IMI supplied us with financial support and technical information. Construction Robotics also designed the electronics and motion control system for our robot. This is a project that only an interdisciplinary team can tackle effectively. I’m really grateful for all their input. Students are especially thrilled to be working on this project because it exposes them to a wide range of experts from different disciplines while remaining focused on the problem of building. Financial support for the work was also made possible by generous grants from Autodesk, the American Institute of Architects, and the New York State Council of the Arts.
Are there specific ways that you’re looking to develop OSCR further in the future?
It’s hard to say what we’ll learn from the trades, but it’s going to be very exciting to see what track they put us on next.
“If architects participate in the invention of … new systems, then they can also better shape the future of built form.
What new tools are helping you tackle this work?
One of the key technologies we are using now is 3-D metal printing. Today, we can use different digital techniques to create new machines part-by-part. This way of working runs against the traditional approach of forcing ideas through existing craft procedures or even through store-bought software packages running off-the-shelf CNC equipment. Metal parts solve a lot of mechanical problems that less durable, plastic components cannot. Buffalo Manufacturing Works [BMW] is a key contributor to our project. Their advanced fabrication equipment allows us to quickly build very strong, high-tolerance parts in titanium. BMW is a state-run, university-affiliated consortium located downtown near UB’s medical campus. Their facilities allow companies to test new digital manufacturing processes before they adopt them.
Are there any limitations, from a design standpoint, to developing robots for construction sites?
What you’re asking raises some very interesting scientific and philosophical questions. From an engineering perspective, I think it’s hard to know for sure what will be possible in the future. Are there specific limits newly discovered physical laws will place on the operational intelligence of machines? How smart can a robot be if it has no mind, no feelings, or experiences? And is it even possible to construct a conscious artifact? These are really hard problems to address. The other issue you raise involves specific ethical challenges that can be more easily tackled. I don’t think we want to construct conscious machines because in the end they would be utterly useless. No one wants to be called a ‘tool’ and robots are just that, tools. Without emotions, machines don’t experience pain and that is what allows them to function so well. They are the ultimate servants.
Discussion
Be the first to leave a comment.
You must be a member of the BuiltWorlds community to join the discussion.