
Houston-based Hines Interests, one of the world’s leading real estate development, investment, and management enterprises, is getting into the lumber business. Having recently completed a seven-story, 220,000-square-foot mass-timber building in Minneapolis, Hines is planning to develop a second wood-framed structure in Chicago and is said to be eyeing a third in Atlanta.
The move marks a departure for a firm perhaps best known for dotting skylines with glossy glass and steel high-rises. It also heralds the first time a US developer of Hines’ stature has demonstrated significant interest in mass-timber buildings.

Wood frames are gaining buzz in the US construction industry, the result of recent advances in the engineering of glue-laminated timber, specified for columns and beams, and cross-laminated timber (CLT), frequently specified for floor slabs, walls, and roofs. Research and testing have also doused concerns about the performance of mass timber during fires, since the material forms a charcoal coating that functions as a barrier to protect and insulate the wood’s inner layers.
Additionally, timber-framed buildings frequently outperform steel and concrete frames in lightness, strength, sustainable design, insulative properties, and speed of construction.
To date, however, mass-timber structures remain few and far between in the US and typically rise only four to five stories, in accordance with building codes. Among the exceptions are Framework, a 12-story mixed-use development in Portland, OR, due for completion in December, and 475 W. 18th, a 10-story New York City structure opening in 2018.
At present, the Minneapolis structure, designed by Michael Green Architecture and DLR Group, with Magnusson Klemencic Associates serving as structural engineer. reigns as the nation’s tallest mass timber building. Its name, T3, stands for “timber, technology, transport,” denoting a clearly defined tenant base: office-based enterprises seeking the rustic charms of loft-style spaces, similar to those of refurbished manufacturing plants but with superior technical infrastructure and easy access to public transportation.
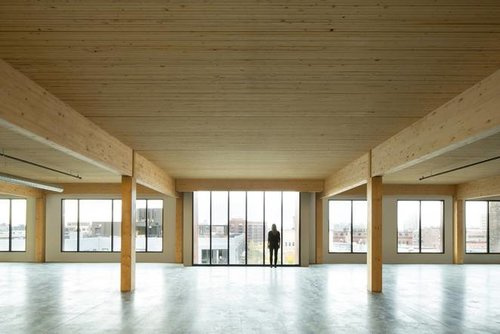
In 2015, Hines indicated T3 would be the first Minneapolis building to receive preliminary Wired Certification, a standard based on excellence in internet connectivity, including redundancy and resilience.
“Our goal is to deliver the warmth and authenticity of a brick and timber building, with all the benefits of new construction,” Hines confirmed in an online statement discussing T3. “In addition, using wood to construct T3 generates numerous environmental benefits. The heavy timber throughout T3 actually absorbed CO2 before being harvested, and there are fewer carbon emissions during the manufacturing process compared to steel, concrete, or masonry.”
Online retailer Amazon, a proponent of sustainable design, has leased 70,000 square feet in T3 to establish a technology development office.
“It’s a really, really creative way of appealing to those office tenants who are looking for nontraditional, creative-type office space.”
Assuming T3 serves as a template for the Chicago undertaking, “Ir’s a really, really creative way of appealing to those office tenants who are looking for nontraditional, creative-type office space,” Kyle Kamin, a tenant broker and executive vice president with CBRE, a real estate enterprise with no ties to the the project, told reporters. “It’s a cool, creative design that feels more organic than glass and steel.”
The Chicago project will be sited at Goose Island, a 160-acre parcel on the Chicago River that’s home to UI Labs, a public-private research and development enterprise. The island is sparsely populated, but Kamin predicts it will emerge as Chicago’s “next frontier for development.”

Though Hines declined to discuss the Chicago project with BuiltWorlds, much as it did with media during preliminary planning for T3, it is anticipated that the building will match the size of the Minneapolis structure, assuming plans are approved. Because the developer hasn’t released renderings of the project, issues of height, massing, cladding, and structural design remain an open question.

T3 may provide some hints, however. The building is clad in weathering steel, with the interior featuring exposed timber. Rather than CLTs, the structure employs nail-laminated panels (NLPs), with other components such as a post-and-beam frame and a concrete topping slab. “The T3 structural framing system—columns on a 20-foot to 30-foot grid, beams running one direction between columns, and panels spanning across beams—is an efficient one,” Lucas Epp, a structural engineer with the project’s wood fabricator, StructureCraft, told reporters. The result is a one-way system with service lines extending alongside beams. Hence, no clashes.
Typical of mass-timber construction, many wood components, including NLT panels, were prefabricated. Under the direction of general contractor Kraus-Anderson Construction, crews put in place 180,000 square feet of wood in nine and a half weeks, proceeding at a rate of about 30,000 square feet per week.
Discussion
You must be a member of the BuiltWorlds community to join the discussion.