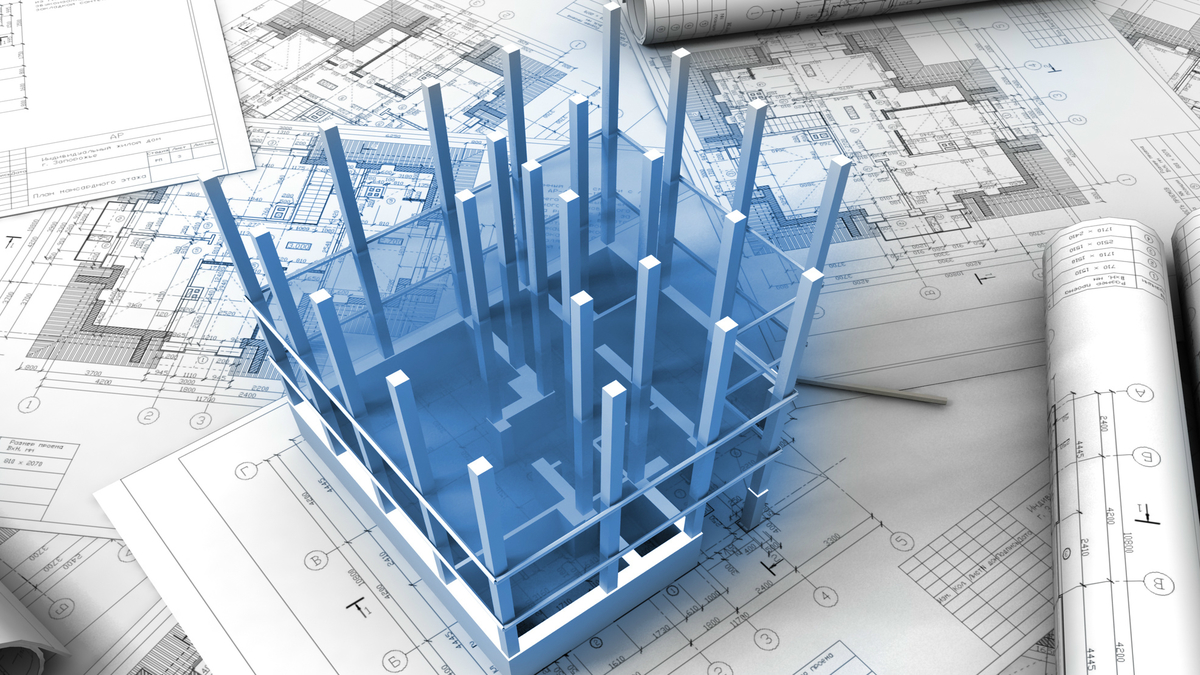
This article is a Contributor Post written by Matthew Carli of Laticrete. If you are interested in the BuiltWorlds Contributor Program, click here.
Understanding construction has meant a cryptic world with a backbone of sweat and heavy hard work for as long as people have built structures, which undoubtedly has produced rewarding structures the world over. However the near future will make this world seem as backwards as not being able to flag a taxi via an app. BIM and its increasing dimensions, like integrated supply chain, providing full integration from design to install to use will be digitalized, which is where we, as a material supplier, get excited.
This digitalization of construction, having data points on the job site, even post install, combined with new installation systems like 3D construction printers or off-site construction solutions are quickly creating an environment for development that the construction materials world has only dreamed of. While much is still in beta theory currently, technology adaption will hit the construction world at an exponential rate as it makes up for lost years of stagnated productivity, and the momentum is already picking up, from investors in drones, 3D printing, and top tech companies entering the space.

New technologies such as 5D Building Information Modeling (BIM) or 3D concrete printing (3DCP) are not yet commonplace, yet quickly gaining traction, as the adoption curves have already been set in motion. These kinds of digital and automated technologies have the interest of investors, the tech community, large construction players, and those who have been searching for solutions to address productivity gaps, all creating a platform that will push the limits to what construction materials have meant in the past.
Productivity gains can be encouraged and embraced by various forces; we are starting to see government entities, trade groups, and others in the construction sector pushing to integrate – or at the very least consider – new technologies. In 2009, Wisconsin became the first U.S. state to require the use of BIM on state-funded projects of a certain size. Trade associations like the Modular Building Institute (MBI) are encouraging innovation within the industry by promoting Permanent Modular Construction (PMC) technologies, with a goal of five percent commercial market share by 2020. In 2011, Singapore established a Building Innovation Panel, tasked with evaluation and approval of innovative construction products and methods.
The government of Dubai, with Sheikh Mohammed bin Rashid Al Maktoum leading the way, has launched the ‘Dubai 3D Printing Strategy’ with the intent to become the leading hub for 3D printing technology by the year 2030. All over the world we are seeing the exploration of/desire for improved productivity/efficiencies, giving validity to what economists have been saying for years of the labor and productivity threats to construction, and turning these into opportunities to put their city or country on the map of progress.
Off-site prefabrication is an example where the potential for new material development is directly related to the potential of all the dimensions of BIM modeling and a single integrated digital environment that seamlessly shares project information across all parties from material manufacturer to designers to supply chain to installers and more. This exchange of information, combined with a job site free of contaminates, climate controlled, and reducing numerous other variables means that we can develop and optimize products to a level of precision previously unthinkable.
New and Related BuiltWorlds Content
Then, as the cycle continues and the concept known as, Design for Manufacture and Assembly (DfMA), is applied, we get an end result that is both customizable and reproducible, making design dreams economically feasible with higher productivity than current construction methods, a win-win all around. This from the material perspective mean a collaborative space for development of technologies like robotic installations or UV cured system.
Future materials is not the only area where BIM will be changing construction, the latent benefit of technical expertise properly integrated into selection and specification choices will mean getting the right product for the job. Internally at Laticrete for example, we are sitting on 62+ years of collective industry knowledge and testing data that currently is entering the market in the form of massive submittal packages, data sheets, safety data sheets, LEED submittals, and more, that get read slightly more often than user agreements for your smartphones.
Imagine where all this collective intelligence would be fully integrated into the BIM objects themselves, making users’ source experts. Systems will aid in selecting the right material based on a myriad of characteristics from weight, compatibility, environmental impact, and others, to name a few.
Combining past knowledge, real time data, and future product development means that the construction process of tomorrow will be a calculated production effort, leveraging the strengths of all the aforementioned knowledge base that (pardon the pun) creates a structured platform for the future of architecture. So, from a material supplier’s perspective, BIM and other technologies entering the construction world are welcomed with open arms, as they present a platform to showcase the potential to what material science can do.
BIM and other consolidated platforms in construction will eventually be used by all in the construction value chain facilitating sophisticated designs in a seamless coordinated fashion. Even going further on this integrated exchange is the ability to simply click, print and have your building constructed robotically. The BOD (Building on Demand) is an example future that is already here, the first printed building in Europe was the brainchild of Henrik Lund-Nielsen of 3D Print Huset in Denmark who is part of a growing focus on 3D construction printing, again getting us, from the material supply side excited to push our labs towards the optimal mortars for these new constructors.
The downstream is even more promising, as new materials emerge for 3D printed barracks on the battle fields reducing the risk for soldiers, structures on the moon using locally sourced materials, or buildings constructed in their own footprint, be it on top of a mountain or under the sea, the potential material demands grow with each new case.
While some of this may sound like a utopian environment, and I agree, this future exchange of integrated designs, schedules, costing, supply chain, and more will in my opinion simply be what the future market will expect. Managers and owners will expect the same information to make decisions like we see in the myriad of dashboards quantifying the rest of the world around us, so why would construction be any different? Change never comes easy, but as the title of this article suggests, from the perspective of the construction material world, BIM and all its future dimensions gives a source of excitement to truly implementable technological breakthroughs that I personally cannot wait to see.
Matthew Carli is an avid world traveler, passionate about people, nature, food, and quickly becoming a futurist upon seeing the potential opportunities within construction technology. Working in strategy and business development at Laticrete International, he dedicates a large percentage of his time working to crack the puzzle to how we can integrate technological advancements into the flooring industry.
Discussion
Be the first to leave a comment.
You must be a member of the BuiltWorlds community to join the discussion.