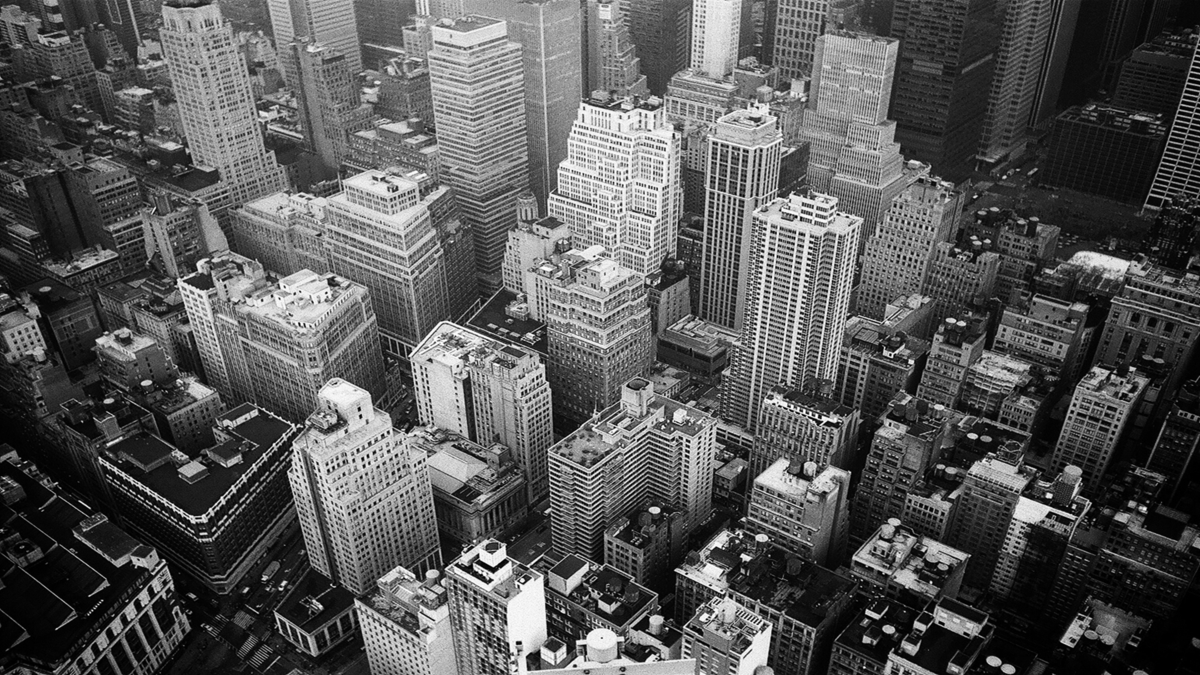
Last week, the BuiltWorlds team left snowy Chicago for New York City for our Projects NYC Conference. Focusing on the crucial preconstruction phase, this gathering of industry professionals featured discussions about the emerging solutions that builders are using to get their projects off the ground more efficiently.
The conference was held at Company (formerly known as Grand Central Tech), overlooking the iconic Grand Central Station. Company began two years ago as a place to foster innovation and encourage the growth of local technology and smart city solutions in Manhattan for growth stage companies. It is a haven for successful startups that have recently exited either an accelerator or incubator program, and are in the growth stage.
Separating themselves from WeWork and other co-working spaces, Company really focuses on creating an ecosystem of similar ventures. This allows tenants to interact with other companies they are likely to work with or engage within the normal course of business.
“That is the number one reason people are here,” said Robinson Hernandez, the executive director of Company’s UrbanTech Hub.
Currently, there are 55 startups in Company’s portfolio, including BuiltWorlds members Kwant.ai and OnSiteIQ.
Throughout the day, we heard from industry leaders and were given demos of some of the most exciting preconstruction solutions on the market. Here are three of key takeaways we gleaned from Projects NYC:
1. Increase efficiency and limit the number of different technologies used on job sites
Preconstruction is arguably the most important phase in a project’s lifecycle. Get it wrong, and you are immediately faced with mounting delays and busted budgets. In recent years, as we’ve seen more and more technology solutions being utilized successfully in the construction process, many builders have turned to digital solutions to tackle the preconstruction process. Yet, it seems we’ve hit critical mass when it comes preconstruction software tools.
“A lack of technology is not the problem,” said Andrew Petty, Firm BIM Leader at CannonDesign, during the conference’s first panel, focused on interoperability. “It’s actually too much technology. You need to evaluate what’s right for each project.”
A lack of technology is not the problem. It’s actually too much technology. You need to evaluate what’s right for each project.
This sentiment was shared by Petty’s fellow panelists. While having a digital solution available to get a project successfully off the ground, not all firms operate using the same tools, which causes mismatches and all-around chaos. Often times, contractors are in touch with a variety of different stakeholders as they begin laying the groundwork for a new project.
“We are dealing with owners, clients, partners, and engineers,” said Vin Solano, Executive Vice President of Preconstruction at Hollister Construction Services. “A centralized tool is missing. We are using a couple of different platforms.”
This complicates things during preconstruction, as each stakeholder has their own preferred tool they use.
“Unlike the airline industry, you can’t force everybody to use one given tool,” said Michael J. Squarzini, Managing Principal at Thornton Tomasetti.
As Solano pointed out, there needs to be a centralized tool--or a few different tools--that are essentially industry standard, so that builders aren’t having to hop from program to program, solution to solution, every time they take on a new job. This way vital information, BIM models, and plans can easily be transferred and accessed easily and quickly.
Related Content
2. Data standardization is essential
Segueing from standardizing preconstruction tools, one topic that received a significant amount of air at Projects NYC was the standardization of data. During a panel about the new horizons in preconstruction technology, Brian Ahmes, Co-Founder of Parafin, spoke about hurdles developers have to overcome during preconstruction.
“Developers are jumping from Excel and sketches on the back of napkins and envelopes to generative design,” he said.
Despite this, the industry has no standard on how data should be shared.
“Before the industry gets standardized, you need to have internal standardization,” said Satyam Verma, a partnerships and market development lead for Pype. “Our interoperability is only as good as the workflows that already exist.”
Developers are jumping from Excel and sketches on the back of napkins and envelopes to generative design.
Much like the point made above, data is shot around the industry in a variety of formats and methods, depending on the preference of the stakeholders involved, which can be problematic.
“Everyone wants interoperability,” said Dustin Devan, CEO of BuildingConnected. “But it’s difficult, because you have to choose which relationship to invest in.”
Both internal and industry-wide standards need to be set in stone so that important data can be readily shared with ease.
“I do look forward to a future where data is flowing because that could lead to some improved outcomes,” said Devan.
3. BIM isn’t going anywhere
Stop the presses. You heard it here first.
“Everyone has accepted BIM isn’t a fad,” Micahel DeLacey, Principal and CEO of Microdesk, told Kevin Bredeson, President, and CEO of ConTech Consulting, during a Fireside Chat.“It isn’t going away; it’s driving efficiency in design and construction.
This really should come as a shock to no one, but it’s important to note. Because while BIM has slowly become more widely used over the past two decades, we are at a new turning point for the technology now.
“We are in an industry that’s in a huge transition,” DeLacey said. “BIM has been around for 15 years, but it hasn’t been adopted across the board.”
DeLacey believes that the industry is at “the 50% mark” when it comes to total adoption. While many owners call for the use of the technology on their jobs, they really don’t understand it or exactly how to effectively get it on their jobs.
We are in an industry that’s in a huge transition.
“They want to offload the technical responsibility,” DeLacey said. “We try to encourage them to pay attention to the technology.”
DeLacey says that more and more accepting responsibility for the technology they demand and are hiring experienced people to bring it to their jobsites, but the industry still has a “long way to go.”
In the meantime, more and more owners need to take steps to understand how the technology can be effectively utilized on their jobs.
Discussion
Be the first to leave a comment.
You must be a member of the BuiltWorlds community to join the discussion.