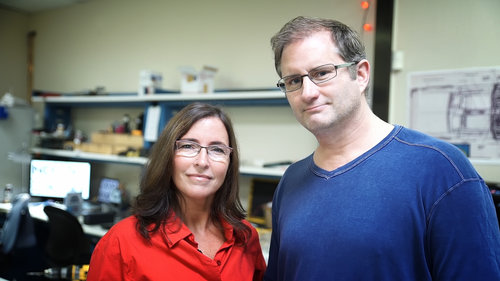
On the eve of President Trump’s inauguration, the National Oceanic and Atmospheric Administration quietly released its latest report on rising sea levels, and the news was far from good. The document predicts a global mean sea level rise of at least 0.3 meters and as much as 2.5 meters by 2100, and portions of the United States along the coastlines of the Atlantic and the Gulf of Mexico are expected to see above-average rises, leaving their low-lying urban areas even more prone to costly water damage.
With the fight against climate change moving at a crawl, most development in such areas is working to take increased water levels into account, either via construction of levees or structures propped on stilts, but Greg Henderson of Arx Pax has a different solution. The US Army veteran-turned-seasoned architect and engineer formed his company a few years ago with the idea for a three-tiered foundation system, dubbed the SAFE Building System. It consists of a pool of water at its base, filled with hollow concrete modules that are linked to create a solid platform on which to build. The platform is protected from flooding because it can actually rise with the water level, and it’s also protected from other disruptive events such as earthquakes.
Curious about how—and how soon—the SAFE Building System might be implemented, BuiltWorlds spoke to Henderson recently. Read on to learn more about the particulars of the system, how it inspired Arx Pax’s ancillary work in hover engines, and how the company is working to get pilot projects off the ground in flood-prone parts of the US and elsewhere, including the Republic of Kiribati.
So you were a partner and principal at other architecture firms for more than 15 years before you decided to move out on your own and found Arx Pax. What was behind your decision to leave?
My grandfather was a carpenter, his father was a carpenter, my dad had built some homes, and so I knew I wanted to build. When I got out of the army, I came back to California and I joined a construction crew to learn. I was with my family’s small development company; we were doing small residential projects in the San Francisco Bay Area. At the same time, I took every class I could at West Valley Community College.
The whole time, I’m studying and understanding more about humanity’s approach to building. The international building code, if you get into the purpose of it, is a pretty low bar. The entire purpose is essentially to make sure that, during disasters, buildings don’t collapse on the occupant. Most architects focus on the aesthetic, the design, and I was taking in more of a holistic approach. My ideas were unconventional, and so in order to be able to try them, I had to go out on my own.
How did Arx Pax get started? Why get into hoverboards?
Back in 2012, [my wife] Jill and I formed the company, and we realized, after talking to business advisors and friends, that it was going to be a tough slog to change the world’s largest industry—which happens to be also one of the most conservative industries.
Our first patent was the three-part foundation system. We realized that the most cost-effective way of separating a structure from the earth is to simply float it. We’ve been floating things for thousands of years, and when something is floating, it is impervious to floods and rising sea levels and earthquakes. I thought, “OK, what are all the ways you could float something?” You can float something in water, you can float it on an entrapped gas, you can float it on a liquefiable solid, and the question in the back of my mind was, “Well, why not use an electromagnetic field? If you can levitate a 50,000-kilogram train, why not a house?” Back in 2012, I wrote in a big, fat Sharpie marker on our living room mirror, “Build a hoverboard, and use it to draw attention to the three-part foundation system.” And that’s what we did.
Wow, so the hover technology is actually directly linked to the SAFE Building System.
The ironic thing is we have hover engines that are powering a half-dozen teams in the SpaceX Hyperloop competition. The only real new technology that’s being developed with the Hyperloop are hover engines, and there’s some really unique properties there, but we want to empower other people to solve that problem. Our focus is on the SAFE Building System. It’s our obligation to get it going as soon as possible because we know it can save lives, property, and communities.
“The example I like to use is the SR-520 bridge. … We’re talking about 19.9-20 acres of floating concrete structure that weighs over 400,000 tons and that’s able to carry an additional 300,000 tons. … We are taking that technology and making it much more cost-effective.”
You announced the SAFE Building System in October of last year, but how long had you been thinking about it before that?
I’ve been thinking about it and working on it quietly for many, many years. We’re innovating by integrating a bunch of very well-proven technologies.
The example I like to use is the SR-520 bridge. It’s a floating concrete bridge across Lake Washington, outside Seattle. If you look at just the pontoon system that supports the SR-520 bridge, we’re talking about 19.9-20 acres of floating concrete structure that weighs over 400,000 tons and that’s able to carry an additional 300,000 tons. That’s a lot of building, people, and property that you can safely float. And that bridge is built in proximity of the number one earthquake hazard in the United States: the Cascadia Subduction Zone, off the coast of Washington.
We are taking that technology and making it much more cost-effective. Instead of casting in place giant concrete pontoons that weigh 11,000 tons, we’re talking about precasting concrete pontoons in a factory setting where we can rapidly produce them very cost-effectively at the size of shipping containers. You can move and assemble them with normal construction equipment.
Your announcement included a quote from Bay Area structural engineering firm Daedalus. Is it involved with your work at all?
Doug Robertson, the principal of Daedalus, is an accomplished engineer, particularly in terms of base isolation. There’s a massive masonry building at UC–Berkeley called the Hearst Mining Building. I think it’s about 100 years old. He was the project engineer who was in charge of its base-isolation retrofit.
We’ve worked personally on residential projects together. He’s the one who developed the engineering drawings that we have right now for SAFE Building modules. And we have memorandums of understanding that we’re establishing with premier design and structural firms—many of them global—to design not just in the US but according to building standards around the world.
Your announcement mentioned a pilot program with the Republic of Kiribati. How is that progressing?
Kiribati is the lowest-lying nation in the world. They’re on the absolute front lines of climate change, and every year their whole country floods. In May of 2016, I had the opportunity to present a little bit of what we’re doing at the UN, and the next day I got a call from Ambassador [Makurita] Baaro. She’s put us in contact with the presidential cabinet, and I’ve been going back and forth, trying to coordinate with their minister of public works and utilities. We’re trying to establish a pilot project, but the challenge is the countries and the people who need this technology the most are the least able to afford its development. The last time I heard from the minister, he was in the United Arab Emirates, trying to raise money.
It’s not just loss of land, either; their most pressing problem is loss of potable drinking water because they rely on rainwater to resupply their wells. The SAFE Building System has an added benefit that it can actually capture and store rainwater.
Where else are you looking to develop soon?
We’re partnering with people in places like Australia and New Zealand. There’s a small team in Australia, Ecohouz, and they’re trying to bring the system to places like Bangladesh that are in dire need.
Here in the US, there’s been great response, not surprisingly, in the places that flood the most. I spoke with a gentleman from the Coastal Protection and Restoration Authority who has helped develop the coastal master plan for Louisiana. Louisiana is losing land through erosion and sea level at an incredibly rapid rate. I think it’s four football fields an hour. The other big area is Florida.
All of these areas need help, and FEMA’s in a bit of a predicament because they’re already $20 billion in the hole, it doesn’t look like the national flood insurance program is sustainable, and the reinsurers are starting to balk and understand that this is not sustainable. FEMA’s saying, “You have to either reinforce or retreat.” We’re offering another alternative. We can simply get out of the way, and the best way to do that is by learning to design structures that can accommodate and move over things like flood waters and storm surge.
So it sounds like you haven’t begun actual construction yet.
We have not begun actual construction, but what’s convenient is that the work we’re doing is transferable. The engineering we’re doing, the analysis, the value engineering—the result is we’re going to come up with a very efficient system that can be deployed anywhere. And there’s a significant advantage to this: in terms of real estate development, urban development, one of the biggest factors in cost is the time to deliver a project. We can design our system, know exactly what the conditions will be, and build your structure ahead of time. The faster you can deliver a project and cut down on time that you have to cover financing is a big deal to a lot of people.
“FEMA’s saying, ‘You have to either reinforce or retreat.’ We’re offering another alternative. We can simply get out of the way, and the best way to do that is by learning to design structures that can accommodate and move over things like flood waters and storm surge.”
How quickly could you scale something up if someone were to approach you with funding?
A matter of months. Properly funded we would build in the Bay Area, our backyard, but we can deliver anywhere. If an investor wanted to fund a specific development, the first thing we’d do the next day is order molds for our modules. These are high-quality molds that would make these precast concrete modules. An acre would take 226 modules, so if you figure you can do about one module a day per mold and we’ve got 10 molds going, that gives you an idea of our production for an area.
Our main goal is to establish regional partners who know their markets, know their local building codes, know the officials, understand the players. We want to partner with a developer in every major region—in Miami, in Houston, in New Orleans, along the Barrier Islands, in Seattle, in the Bay Area.
A lot of flood-prone cities now have chief resilience officers. Have you been able to get any traction with any of them directly?
Yes, but there are a number of government agencies and quasi-government agencies that have a say, including the Army Corps of Engineers. Here in the Bay Area, there is the California Coastal Commission, there’s the local city and the county, there’s California Fish & Game, there’s the Regional Water Quality Control Board. All of these agencies need to approve projects, so we want to work thoughtfully with all of them. It’ll be very interesting to see which city goes first, and unfortunately it will probably be after the next big flood, when they understand, “OK, it’s time to do something.”
What are the general permitting and approval challenges of getting your building system into flood-prone urban areas? Are there any regulations you might face?
Undoubtedly, but we’re introducing proven technology. We’re just combining well-known systems, so you look at the containment vessel and say, “OK, well that’s a pool or a reservoir, and we know how to build those.” You look at the construction platform and say, “Well, yeah, that is a floating concrete pontoon, and we’ve been doing that for 100 years.” You look at how it’s connected, how the utilities work, and say, “Well, they’ve been doing that with flexible dock connections for a very long time.” We’re pulling all those pieces together and integrating them.
One of the primary concerns is historic preservation. For every regulatory challenge, there’s an asset, and one of them is being able to retrofit and preserve historic structures to get them out of floods. There’s a famous piece of architecture in your neck of the woods, the Farnsworth House. They’re trying to figure out how to preserve it because it’s in a flood zone. There’s an expensive proposal for some sort of mechanical lifting device. It’d be a whole lot simpler with the SAFE system.
Discussion
Be the first to leave a comment.
You must be a member of the BuiltWorlds community to join the discussion.