Offsite construction, commonly thought of as the conception, design, and fabrication of building components, systems, or entire modules at an offsite location before their ultimate installation onsite, is continuing to garner increased attention in the AEC industry. In fact, preliminary data from BuiltWorlds' 2024 Offsite Construction Benchmarking Survey shows that over 75% of respondents encourage their trade partners to employ prefab or modular techniques. Similarly, over 81% of companies plan to participate in a project consisting of prefabricated or modular components in the next year, further highlighting the industry's shift offsite.
In an effort to better understand the rapidly evolving role of offsite construction and how it will impact the industry, we sat down with Ben Bruns and Melanie Taylor, The Boldt Group's new Modular leaders responsible for growing the modular business geographically and across industry sectors.

Ben Bruns, Vice President of Modular, The Boldt Group
Initial insights from the duo focused on advancing capabilities across three key areas:
- Design: The design process is evolving to support modular construction through iterative experience and continuous learning (DfMA).
- Versatility: While most people are familiar with prefabrication in the single and multi-family housing markets, more building types are taking advantage of standardization in design to leverage IC. For example, much of Boldt’s current and recent modular work is in the healthcare industry, specifically with patient bed space, exam rooms, and other repeatable areas.
- Production mindset: There is more focus on creating standards and controlling the supply chain and logistics to ensure the kind of repeatability that can maximize offsite construction opportunities, especially at scale."
Read the rest of the conversation below!
1. Across the spectrum of offsite/industrialized construction, what and where are the biggest opportunities for leveraging the various systems/technologies in commercial, heavy industrial and/or infrastructure construction?
While offsite/industrialized construction (IC) is seeing increasingly widespread adoption across many vertical markets, including commercial, heavy industrial and infrastructure, the industry has yet to fully achieve the level of industrialization the manufacturing sector is known for. There is ample opportunity to adopt these manufacturing principles, design thinking and technology in the built environment, even accounting for the considerable variability in the nature of the projects across these markets.
For example, commercial projects (including workplaces, hospitality and multifamily housing) lend themselves better to what we consider the far end of the IC spectrum with flat-packing or volumetric modular construction. An example most of us are familiar with is modular hotel rooms or offices. These projects tend to be smaller in size and standardized to a degree and therefore easier to modularize, as well as logistically easier to transport via flatbed truck.
Heavy industry, manufacturing, and infrastructure, on the other hand, have different needs. These projects tend to be larger, heavier and are typically more suitable for offsite fabrication of individual components, such as prefabricated wall panels or larger assemblies.
Regarding technology, generative design and the use of configurators are currently a large opportunity in the IC space. Repeatable components, or a kit of parts already designed for manufacturing, can be fed into configurators, allowing new products to be generated and customized to meet needs. Configurators support the transformation of traditional construction into the realm of customizable products.
a. What types of projects would significantly benefit from offsite construction?
Our philosophy is that nearly all projects stand to benefit from IC or offsite construction in some form. As these manufacturing principles proliferate in the built environment, design firms are increasingly being driven to design their projects with offsite manufacturing intent, or Design for Manufacturing and Assembly (DfMA) as it is known in the industry.
By collaboratively developing designs specifically to leverage offsite construction, we are opening the door to new ways to solve familiar challenges related to speed-to-market; shortages of local, skilled labor; weather conditions; constricted staging and laydown space; and enhanced safety, quality and sustainability.
b. Apart from internal processes at Boldt, are you working with any noteworthy partners/technologies to help optimize your offsite offerings?
We have aligned with key design partners and clients who have also embraced this IC philosophy and a mission advancing modular and prefabricated construction at a core level as an organization. When you have that shared culture, you have a platform that lends itself to true innovation, with partners using their unique insight to bring value-added ideas to the table.
This has allowed our teams to collaborate with clients to reimagine what would otherwise be just a series of projects as a true “program.” This, in turn, promotes rapid learning and advancement of our offerings, making each successive project within that program more successful than the last.
Ready to find out more?
Join us this December in Raleigh-Durham for BuiltWorlds' 2024 Offsite Construction Conference where Melanie is joining us to discuss how the industry can effectively connect the factory and job site. Find out more using the link to the right!
2. Offsite construction (modularization, prefabrication) offers an array of benefits—safer, more efficient, more sustainable, more controlled, etc. Yet, offsite construction still hasn’t taken off in the market the way many have predicted, particularly during the pandemic. How do you explain the market’s reaction and relationship with offsite construction?
The rather long nature of design, development and construction means change is slow in construction, especially radical change that requires new ways of designing structures. Many projects recently completed or under construction may have started that development cycle even before the pandemic. So, while we certainly saw an upswing in demand for offsite construction during the pandemic, particularly in the demand for our modular STAAT MOD ICU and observation bed product line, normalization of this kind of thinking is still working its way through the system.
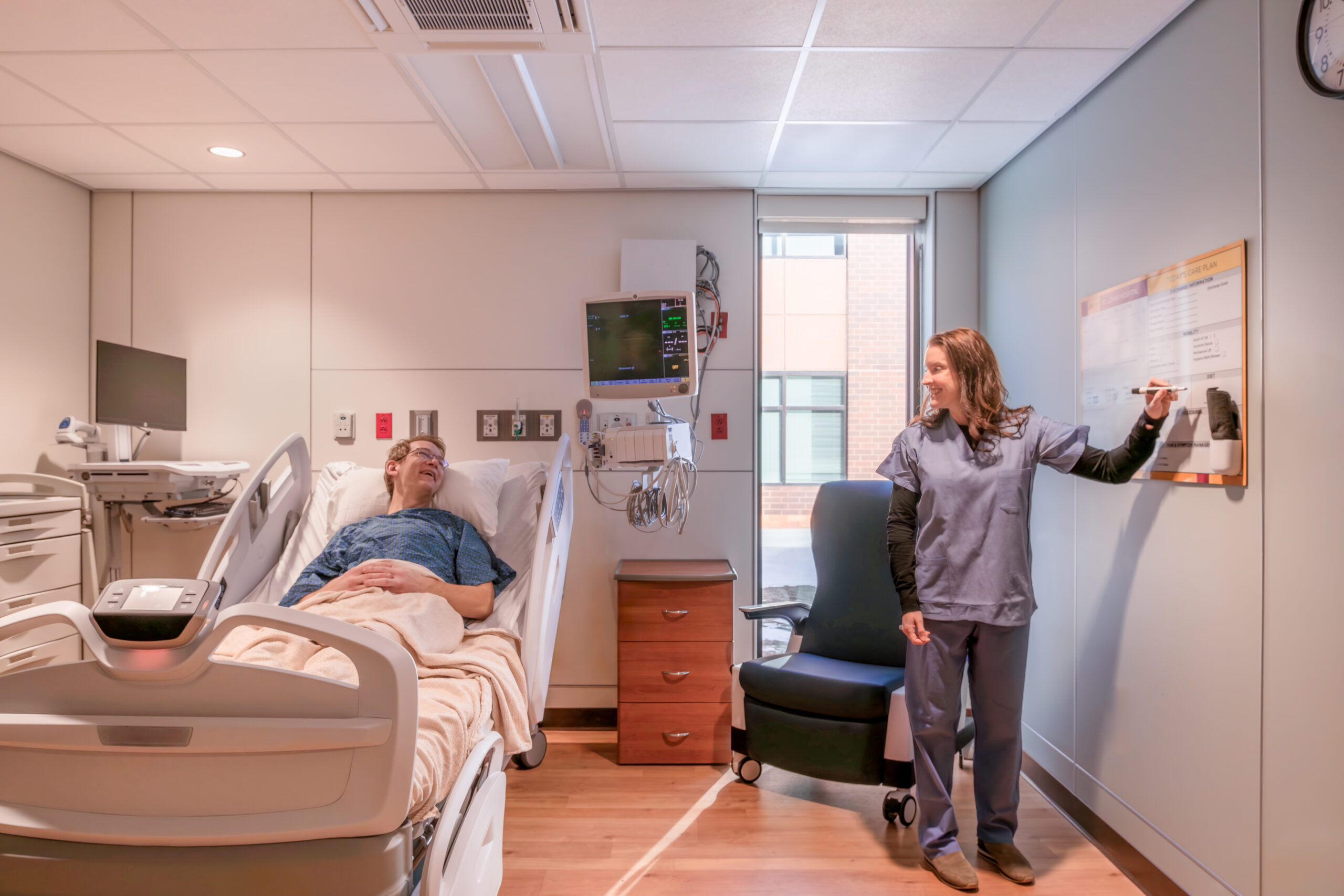
Other contributing factors are challenges in the market with escalation, labor shortages and in some cases, market shrinkage. Some clients and contractors have chosen to focus on their known, core business first, as construction manufacturing does require a significant investment of both capital and human resources. As projects ramp up and costs are driven down (and labor availability remains challenged), offsite construction is poised for growth.
3. Data from BuiltWorlds’ 2023 Offsite Construction Benchmarking Report indicate resistance/lack of understanding from project stakeholders, design limitations, supply chain/logistics, and cost are a few barriers to widespread utilization of offsite construction. Have you had similar experiences?
The construction industry is slow and resistant to change. While we are seeing more interest in the services and products we offer, there is still room to increase awareness. In addition, many people have preconceived ideas about prefabrication based on outdated stereotypes (such as the prefabricated homes of yesteryear.) This is why education and awareness are so vital for the industry right now.
As we share success stories with our clients and demonstrate those operational benefits, we will see that confidence grow.
a. Is there a future where offsite construction can cater to lower price points?
Yes, modular construction must compete with traditional construction – and it can today. Historically, it has been associated with higher costs, which it seeks to offset through blisteringly fast speed-to-market. However, as the industry matures, economies of scale, standardization and improved processes will drive down costs.
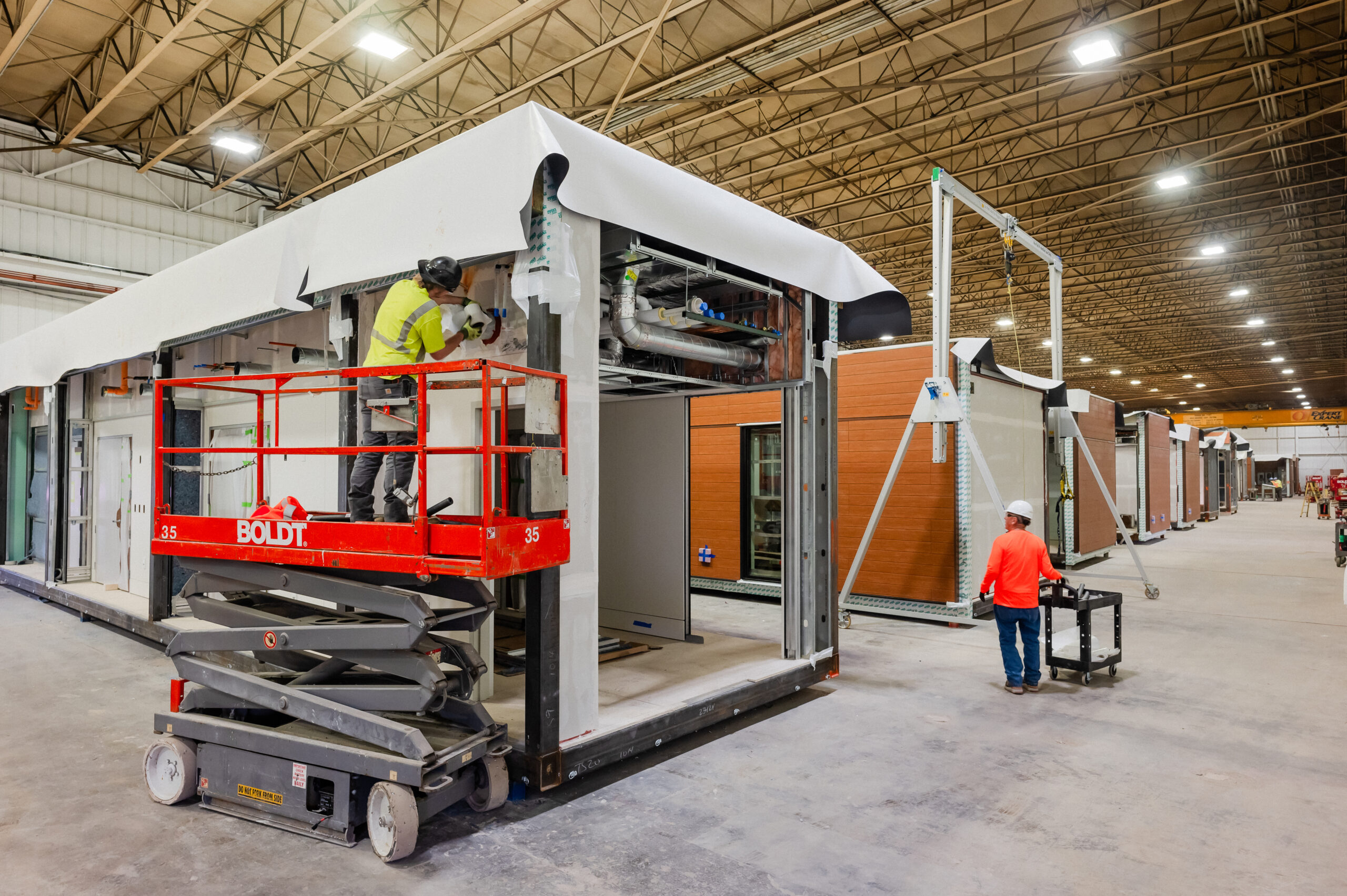
The ability to eliminate waste and deploy improvements is exponentially higher in a factory setting than a jobsite. One of the elements people don’t realize at first is the benefit to an owner’s program of standardization. This process tends to strip out ‘nice to have’ and replaces it with ‘this works perfectly and is not overdesigned.’ Costs per square foot may be slightly higher, but costs per unit are the same or lower because the net-to-gross is optimized.
b. Could the infrastructure in offsite construction support significant scaling up without compromising the industry’s ability to deliver quality construction in a timely manner?
Offsite construction is the solution to ensuring construction is delivered in a timely manner and with quality, even in the face of a shrinking skilled workforce. “Shop” employees can be trained to perform tasks within a defined workflow (rather than specializing in one trade). Manufacturing facilities can operate in shifts, invest in automation and optimize workflows to meet demand. Stronger control in supply chain and logistics will only further this ability to ensure high quality and an accurate schedule, among other KPIs.

4. In growing Boldt’s modular business, what do you see as your biggest challenges, and why are those areas particularly challenging?
Our biggest challenge operationally is one that faces the industry in general: the project development lifecycle isn’t always a smooth, linear process. Sometimes, projects have fits and starts based on a client’s shifting operational priorities or challenges, and a project start date may move out, placed on hold or cancelled. This poses a significant challenge when scheduling manufacturing space and resources including labor.
a. How do you plan to overcome those challenges?
By working to build a steady pipeline and backlog of projects with repeat clients, or clients with larger program needs, we are better able to create a steady flow of work through our fabrication facility. At the same time, Boldt and its partners continue to collaborate with clients to foster the kind of DfMA thinking that will create future opportunities.
b. Can you offer any implementation tips or best practices for others who might be interested in implementing more prefabrication/modularization in their organizations?
IC, including prefabrication and, in some cases, fully-modular construction, can be implemented by nearly all lean-practicing organizations today. Finding the right design and construction partners with experience and a culture that promotes DfMA significantly lowers that barrier of entry.
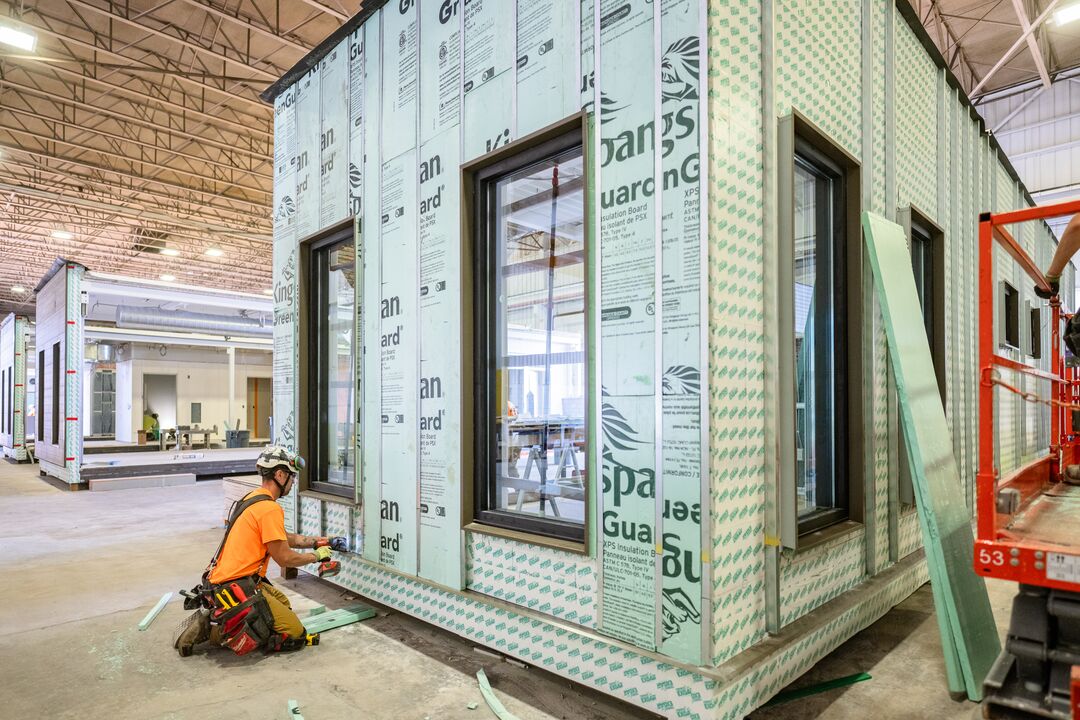
In terms of fully volumetric modular and full-scale manufacturing – In addition to having those experienced partners, organizations interested in implementing these solutions need to understand the capital investment and skillset resources required. Being prepared to fully commit to this investment, embark on the journey and adopt new modalities is crucial to maximizing the benefits.
c. What do you see as the ideal outcome for modular construction in five years, 10 years, and beyond?
The volume of construction that includes modular and prefabrication will outpace traditional construction in the United States. Modular will no longer be novel but the norm. The advantages, including cost, will outweigh a traditional approach; our industry will realize a positive environmental impact and drastically improve workforce well-being.
Discussion
Be the first to leave a comment.
You must be a member of the BuiltWorlds community to join the discussion.