This article was contributed by Joe Dardis of the American Institute of Steel Construction as part of the BuiltWorlds Verified Contributor Program.
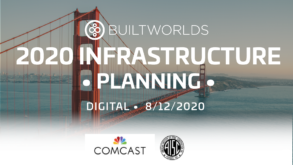
While the COVID-19 pandemic has taken a massive toll in terms of lives, jobs, and industries, the domestic structural steel industry remains vibrant.
While the economy began the year strong, activity in many parts of the country has all but ground to a halt. And while much of the construction industry has been designated as an essential business, there’s a lot of uncertainty about the supply chain.
Much of this uncertainty is due to the generic nature of the word “steel.” When people hear that mills supplying the automotive industry are shutting down, they assume that also applies to structural steel mills. But that’s not the case, and America’s structural steel industry remains a success story.
“We are unaware of any current shortages in steel supply, and all of Nucor’s steel mills have continued to operate during the COVID-19 pandemic,” said Katherine Miller, director of public affairs and corporate communications with AISC member producer Nucor Corporation. “Since the beginning of the crisis, our steelmaking facilities were determined to be ‘essential’ businesses in every state where we operate that has been subject to stay-at-home orders. As such, we have continued to produce steel for critical projects and to meet our customers’ needs for our products without interruption.”
Because steel mills were designated as essential businesses, production continued unabated. This also extends to hollow structural steel (HSS) production.
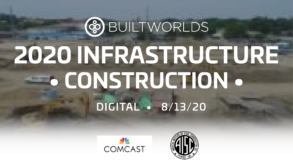
“From the beginning of the pandemic, Atlas was deemed an essential business since the steel industry was deemed critical infrastructure,” explained Brad Fletcher, a senior sales engineer with Atlas Tube, an AISC member HSS producer. “As such, all of our mills have been up and running as normal to meet our customers’ needs. While orders have fallen here and there, by how much varies by region and is due to mandated construction shut- downs in certain areas. We’ve cut back hours here and there based on demand, but we’ve had no layoffs—and we aren’t planning any.”
With operations remaining normal, so have lead times remained short, continued Fletcher. “While there has been some movement with lead times, this is seasonal and normal,” he said. “Lead times have not fluctuated due to the pandemic, and we’ve had no supply interruptions. We have a strong relationship with our coil producers, and there have been zero issues with our coil supply.”
Another bright spot, noted Fletcher, is that not only are current projects staying on target, but design work for upcoming projects appears to be continuing as well. “In talking with designers, they have stayed pretty busy through this, with very few reporting projects being canceled or put on hold,” he explained. “January and February were very busy months and I don’t think we will get back to those levels right away, but we expect things to be back to some positive level in the next six to 12 months.”
Because around 70% of structural steel is purchased from service centers rather than directly from steel mills and HSS producers, they can be a particularly good barometer when it comes to availability. Gary Stein, CEO of Triple-S Steel, an AISC member service center company with a network of approximately 30 locations, was quick to squelch any rumors of decreased material availability. “There are no steel shortages—absolutely, positively not,” he stressed. “I’ve seen headlines talking about steel mill shutdowns, but that’s not structural steel. Structural mills are all running just fine. The only shutdowns I’ve heard of are due to scheduled maintenance. Most structural steel flows through distribution centers like ours, and I and my competitors all have plenty of inventory.”
CLICK HERE TO LEARN MORE ABOUT HOW COVID-19 HAS IMPACTED VENTURE INVESTING IN THE BUILT WORLDIf there‘s any variation in demand, Stein noted, it‘s mostly due to localized construction climates. “In terms of demand, most of our customers haven‘t really shut down, maybe a bit at first but only briefly,” he said. “It really depends on the region, with New York and New Jersey being the most dramatically affected. But that‘s based on job– site closures, not availability.”
And even in areas where construction is on hold, Stein noted that fabrication has continued to stay generally steady as well. A unique problem in places like New York is that some fabricators haven‘t been able to ship finished product to job sites—which creates an issue for those with limited storage area. “So we‘ve let them ship finished steel back to us in those areas, and we‘ve been able to hold their product on trailers until their job sites open back up,” he said.
Structural mills shut regularly for scheduled maintenance, and any pandemic related shutdowns have been brief.
READ THE BW ANALYST BRIEFING 'OPTIMIZED MATERIAL MANAGEMENT: DIGITIZING THE CONSTRUCTION SUPPLY CHAIN'“In April, we conducted a maintenance outage at the Midlothian mill that had been planned since late 2019,” said Adam Parr, director of communications and public affairs with Gerdau Long Steel North America. “In late March, most operations at our Cartersville mill were temporarily suspended due to an increased number of COVID–19 cases in the area surrounding the mill. Normal operations resumed on March 31. We have not announced any lay offs at our structural steel mills, lead times have remained consistent, and we have not seen an extension of expected lead times at any of our structural mills.”
The pandemic did affect the maintenance schedule of one producer—though not in a bad way. “SSAB Americas‘ steel mill in Montpelier, Iowa, which produces steel plate primarily for bridge projects, was scheduled for a planned biannual maintenance outage in October,” said Ivonne Furneaux, director of communications and community relations with AISC member producer SSAB. “Due to the current situation of the COVID-19 pandemic, we are adjusting the outage schedule to an earlier start date. The outage is now scheduled to begin on June 22 and is expected to last approximately four weeks.”
However, outages like this are not expected to impact steel plate’s overall avail ability or pricing, the latter of which has declined for all of this year.
CLICK HERE TO LEARN MORE ABOUT LEADERSHIP AND COLLABORATION STRATEGIES DURING THE COVID-19 CRISISOf course, staying operational also means staying safe, noted Miller. “The health and safety of our customers is our number one cultural value at Nucor, and we have implemented a number of safety measures as we operate during this pandemic,” she said. “These include social distancing, face coverings, staggered schedules, enhance cleaning procedures for work areas, and using remote work where possible.”
“Our primary concerns at this time remain the health and safety of our employees as well as maintaining our quality product and service commitments to our customers,” echoed Furneaux. “At this time, production continues, our supply chain is intact, and we do not anticipate disruption to our service levels. However, we will continue to monitor the situation and will take appropriate measures as warranted.”
“Our plants are running routinely, though with precautionary measures, and sales and office staff have been working remotely,” said Stein. “But we’re still getting our work done. There’s plenty of steel in the supply chain every day, pandemic or not.”
This article was contributed by Joe Dardis of the American Institute of Steel Construction as part of the BuiltWorlds Verified Contributor Program.
Discussion
Be the first to leave a comment.
You must be a member of the BuiltWorlds community to join the discussion.