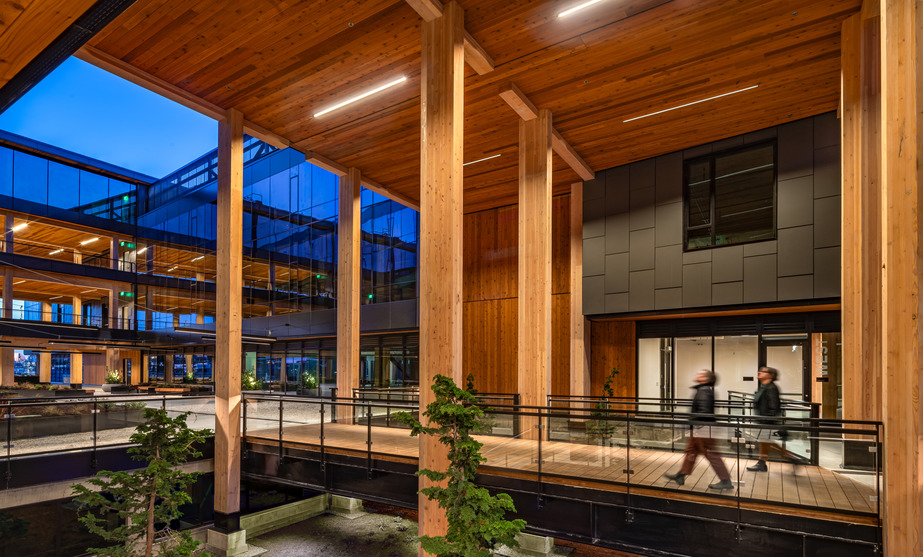
Lisa Podesto, the new director of mass timber and construction innovation at Swinerton, has long been enthralled by the opportunity mass timber presents for the built world. With over 15 years of experience with the material, Lisa's journey into mass timber began at the intersection of her interests in sustainable design and innovative construction technologies.
"I became captivated [in 2009] by a 9-story mass timber project in London: Stadthaus designed by Waugh Thistleton Architects," she recalls. "It was then that I began immersing myself into mass timber, collecting information and developing relationships with designers and industry abroad to translate the project experiences, ideas and solutions to a U.S. context."
Today, Podesto is published as a peer reviewer and author of the first U.S. CLT Handbook (2012), coinciding with the first U.S.-based cross-laminated timber (CLT) production launch. Since then, she has held roles in early project integration in markets where wood was not a typical material choice, such as high-rise buildings and projects for the U.S. Department of Defense, and roles in development and construction aiming to influence project success and advance market adoption more directly.
In a wide-ranging interview, below, Podesto shares some of her extensive knowledge about the innovative material. Responses edited for clarity.
Want to Learn More About New and Advanced Building Materials?
Join us December 4-5 in Raleigh-Durham for our inaugural Offsite Construction Conference and learn from Lisa & others about how mass timber and other advanced materials are impacting modularization and prefabrication.
As a building material in general, what are the advantages and disadvantages of mass timber? How do those benefits stack up against more traditional materials?
The beauty of mass timber is that there are just so many synchronous advantages. This is a material that can truly advance construction productivity while also reducing the environmental impact of the built environment—two of the biggest issues of our time in this profession. It can simultaneously remove embodied carbon from our buildings and create opportunities for reduced carbon emissions and increased carbon storage on the landscape. It offers biophilic and aesthetic opportunities that improve occupant experience and provide market differentiation for owners, while also reducing environmental impacts and cost compared to other finishes.
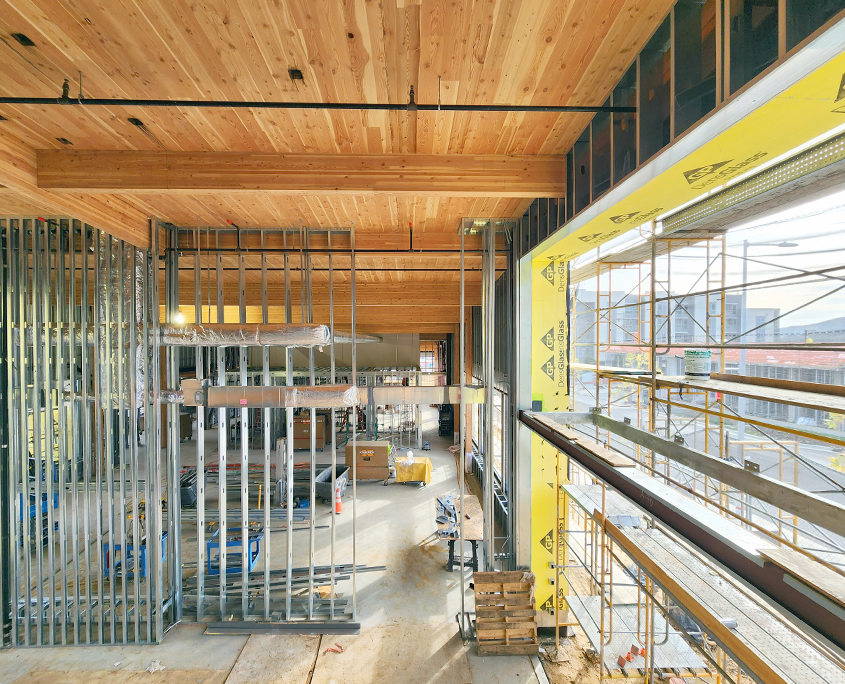
Mass timber's novelty is at the root of [the industry's misperceptions] about its fire or moisture performance, delays in project approvals or the ability to get affordable insurance. But impacts caused by a lack of familiarity are diminishing over time as the industry gains experience where the advantages are actually increasing.
The construction industry tends to resist novelty; the success of construction projects often hinges on an established rhythm, cultivated through generations of experience. However, once the initial apprehension is overcome, it becomes apparent that this novelty may actually offer important transformative potential.
To achieve the promise of mass timber will [require] a rethinking of processes, contractual frameworks, and business practices which the industry so desperately needs. Eventually, the industry will celebrate this technology precisely for the disruptive qualities that slow its adoption today.
With the majority of the U.S.’s old-growth forests gone, is there any question as to the durability and lifespan of CLT (cross-laminated timber) or GLT (glue-laminated timber) materials?
Mass timber, by definition, refers to a category of products derived from small-diameter trees rather than old-growth trees. In North America, these small-diameter trees are largely sourced from working forests, which are cultivated with the intent of being harvested for wood products. Remarkably, the standing timber volume in U.S. forests today exceeds that of a century ago, despite a tripling in population growth and increased resource demands. Our North American forest can support increased demand for wood products. Increasing our wood use will not put our North American forests at risk, in fact, there is more evidence that an increase in demand for wood products can help our forests by providing an economic incentive to keep private forests from transitioning to other land uses and keeping our public forests healthy. Many unmanaged forests in North America are experiencing increasing density beyond healthy limits.
Changing climate patterns and decades of fire suppression have led to severe droughts and diseases, creating conditions conducive to unprecedented wildfires and high tree mortality. Wildfire poses a serious threat to one of the planet's largest natural terrestrial carbon storage systems, forests. To put it in context, the California wildfires in 2021 emitted carbon dioxide equivalent to over 25% of the state’s annual fossil fuel consumption.
Mass timber products present a potential solution by enabling the removal of these hazardous fuel loads from the landscape without large releases of carbon dioxide into the atmosphere. They utilize lower-value, smaller-diameter trees, which typically lack sufficient economic value for removal otherwise. This potential is why mass timber has garnered substantial support from federal and state governments, as evidenced by the ongoing research investments from the U.S. Forest Service Wood Innovation Grants and new mandates from the federal government requiring consideration of mass timber for all military projects and federal buildings.
While the fiber supplying most CLT and [GLT] is not currently coming from public forest thinning projects, this dynamic will change as policy creates better access to thinned material and demand grows. Currently, both California Department of Forestry and Fire Protection and the Oregon Department of Forestry are focused on the benefits of thinning as part of forest management to improve forest health and create forest resiliency against forest fires.
Why has mass timber more quickly caught on in other parts of the world but not the U.S.? Has the price volatility we’ve seen in lumber over the past several years had an impact?
The European and North American markets differ significantly in several key aspects. European consumers are generally more willing to invest in enhanced value, while the North American market prioritizes meeting minimum requirements and minimizing first costs. Much of the value that mass timber can offer extends beyond these minimum requirements.
Consequently, in North America, when mass timber is cost-compared to other buildings, the value is not equal. This inherent value is often incorrectly perceived as an unwanted cost burden, when studied in isolation, that cannot be "value engineered" out of the system. A holistic study will reveal [mass timber is] offsetting cost savings and adding value to numerous other building systems, building qualities and the project schedule.
Furthermore, Europe employs more objective and performance-based building codes, contrasting the highly prescriptive codes in the United States. Performance-based codes provide consultants and owners with greater flexibility to meet life safety and property protection requirements, facilitating the incorporation of novel solutions and fostering an industry culture that rewards ingenuity. Additionally, the U.S. construction industry faces more severe liability risks, further hindering efforts to explore new materials, systems, and processes. Similar distinctions can be observed between the U.S. and other markets where mass timber is gaining traction, such as Australia and Canada.
In North America, when mass timber is cost-compared to other buildings, the value is not equal. Studied in isolation, this inherent value is often incorrectly perceived as an unwanted cost burden that cannot be "value engineered" out of the system.
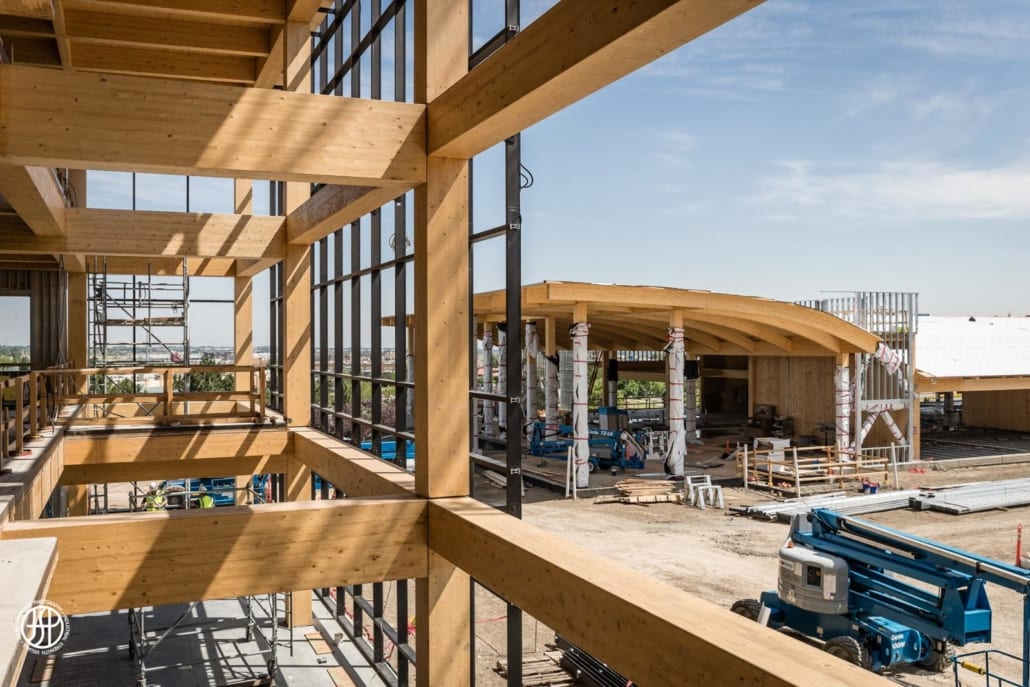
The extremes in material pricing experienced after COVID were felt across the entire material and labor spectrum and were unprecedented. While all commodities experience some degree of normal price fluctuation in response to supply and demand changes, mass timber benefits from a unique mechanism for mitigating this volatility. Project teams typically engage with suppliers very early in the design phase, often a year or more before on-site construction begins. This early engagement provides ample opportunity to leverage pricing trends to the project's advantage. The wood industry has historically experienced more extreme cycles, partly because its demand has been closely tied to the single-family-home segment of the construction market. As timber use expands and is supported by non-residential market segments, we can expect more stable supply and demand dynamics, resulting in reduced overall volatility.
Moreover, the U.S. construction market is extremely large compared to those of other countries, contributing to a perception of slow growth. Despite this perception, the number of mass timber projects in the U.S. has experienced steady growth, with over 1,000 projects built to date. These projects are dispersed over a vast geographical area. Although mass timber is not yet a mainstream building technology, it is increasingly being considered for a growing variety of project types across the U.S.
In your new role at Swinerton, where do you see the immediate opportunities and barriers for mass timber? Where do you see the long-term opportunities and barriers?
One of the primary barriers to the widespread adoption of mass timber is the prevailing misconception that it is more expensive than traditional materials such as steel or concrete. However, a comprehensive understanding of how mass timber impacts the entire spectrum of project trades can guide owners and design teams toward decisions that capitalize on both the value and the cost-saving opportunities while mitigating potential premiums.
The intrinsic advantages of mass timber—such as its lightweight nature, precise tolerances, rapid construction speed, reduced labor requirements, and innate prefabrication—must be strategically leveraged to achieve cost savings. Notably, three critical areas where cost savings can be realized include foundations, vertical structures, and general conditions. Nevertheless, these savings have to be managed against additive costs related to other design aspects, such as the lateral load-resisting system, passive fire protection, building envelope and acoustics. To achieve net cost savings, it is crucial to actively exploit savings opportunities while minimizing budget increases in other areas.
One of the primary barriers to the widespread adoption of mass timber is the prevailing misconception that it is more expensive than traditional materials such as steel or concrete.
In the long term, the mass timber movement faces both significant opportunities and challenges. On the opportunity side, mass timber has the potential to revolutionize the construction industry by offering sustainable, efficient and versatile building solutions. A growing focus on measuring and reducing embodied carbon will create policies that incentivize or even mandate bio-based materials with carbon storage capacity like mass timber.
However, the industry must also contend with barriers such as regulatory inconsistencies and a building authority culture of “no.” The current U.S. building codes are highly prescriptive, but efforts are underway to expand the applicability of performance-based codes. There is also the challenge of securing building insurance and overcoming age-old norms of a linear design-bid-build process, which can create an environment where cost savings are harder to achieve. Many industry stakeholders, policymakers and regulatory bodies are working hard to create a more conducive environment for mass timber adoption.

Swinerton has secured a significant market advantage by strategically investing in mass timber starting in 2016, with the self-performed supply and installation of the then-largest mass timber office building in the U.S. Our proactive approach fostered delivery times four months faster than the industry average at rates 4% cheaper than structural steel.
Today, we are known for successfully building some of the country’s most innovative mass timber projects. This initial success of Swinerton’s mass timber self-perform team has grown into a independent Swinerton affiliate company, Timberlab, which together are servicing a national market.
Our ongoing investments include the construction of a new CLT factory and the acquisition of a GLT manufacturing facility, to not only meet growing demand and enhance our institutional knowledge but to reduce costs and deliver improved price stability through vertical integration.
What role does mass timber, in addition to other low-carbon alternatives, play in the push toward offsite (modular and prefab) construction in the U.S. and abroad?
Mass timber serves as an exceptionally effective prefabricated structural chassis due to its rapid installation speed and high dimensional accuracy. Its large, prefabricated components are quick and easy to install, eliminating the need for on-site measuring or cutting. The structural installation sets the schedule tempo for a project, and the precision afforded by computer numerically controlled manufacturing and fabrication methods ensures high dimensional reliability. This accuracy facilitates the integration of secondary prefabricated components that require tight tolerances.
What distinguishes mass timber from other forms of industrialized construction is the high level of automation in its manufacturing and fabrication processes. This contrasts with the more manual fabrication and assembly techniques prevalent in the offsite construction market. As the skilled labor market becomes increasingly constrained, the automation inherent in mass timber production will continue to enhance both quality and cost efficiency.
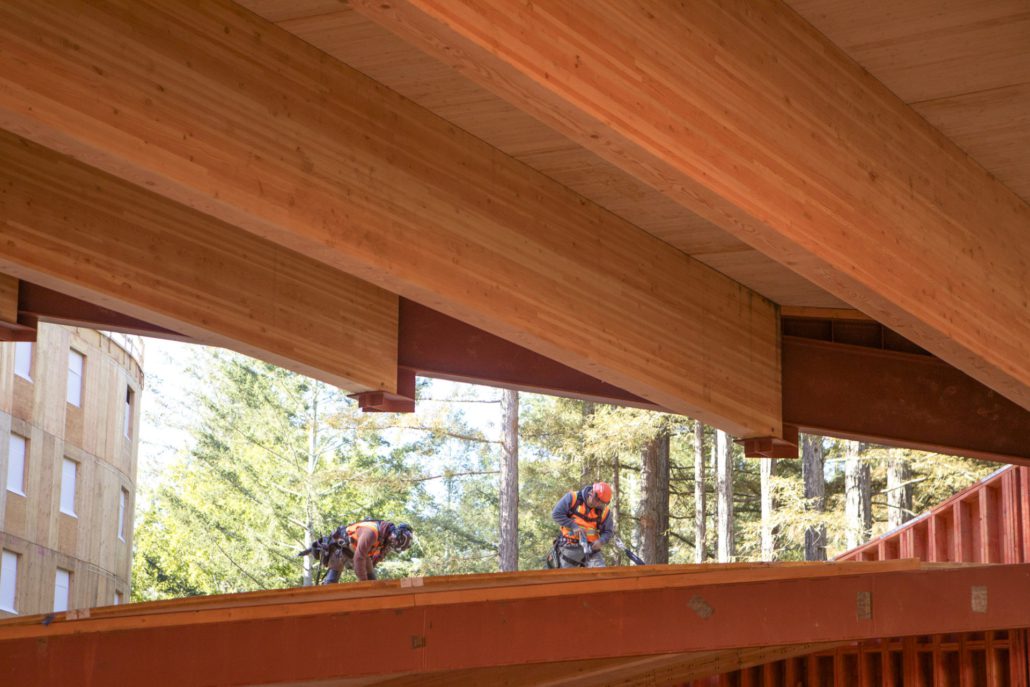
Mass timber also acts as a catalyst for the market growth of other prefabrication modes due to the synergies between on-site and off-site processes. The equipment, labor, and logistics planning required for mass timber installation can also be utilized for other prefabricated components. By leveraging the costs associated with cranes and off-site staging areas across multiple components, the overall cost impact is reduced. Once the modeling, preplanning, and coordination necessary for designing a fully prefabricated structure are complete, the groundwork is already laid for the componentization of services, façades, and finishes.
Because of its role in advancing prefabrication, mass timber represents a significant low-carbon alternative for on-site construction as well; fewer workers and fewer deliveries mean a reduction in emissions for transporting materials and labor to the site, lighter crane loads mean a higher likelihood of being able to use electric equipment and fewer raw materials being cut and assembled on-site means there is far less waste leaving the site for landfill. Its use in offsite construction aligns with the broader push towards sustainable building practices both in the U.S. and abroad. As awareness and demand for environmentally friendly construction methods grow, mass timber’s potential to reduce the carbon footprint of buildings becomes increasingly important.
Mass timber not only excels in prefabricated construction due to its precision and automation but also promotes the integration of other prefabricated components and supports the industry’s move toward sustainability. Its role in offsite construction is pivotal in advancing both the efficiency and environmental performance of building projects globally.
Discussion
Be the first to leave a comment.
You must be a member of the BuiltWorlds community to join the discussion.