(BuiltWorlds Member Contributor Post)
Introduction
Who cares…? Sorry, that came out wrong. I meant, who cares … as in who benefits from … “Quality” in construction? The answer: most everyone cares—or should care—about Quality. But what about measuring it? Who benefits from that? I asked a lot of people—and I got some interesting responses.
Many agree that measuring quality is intriguing and worthwhile. And I think most would agree with the general hypothesis that poor quality probably costs the industry millions, if not billions, of dollars. But it’s not really measured—at least not in a reliable, standardized way across the industry. Costs related to rework, punchlists, warranties, and defective work are typically borne by owners, contractors, subs, designers, and insurance companies—in other words, they’re “baked in.” But what if they weren’t?
In other words, what if we could leverage technology to improve the way we manage QA risk? What if we could establish consistent metrics—and build reliable oversight tools based on those metrics? There seemed to be a lot of interest here…as evidenced by the fact that several contractors are grappling with some version of this problem right now, internally. But what about externally? For example, what if insurers could measure the Quality of a contractor’s performance—in real-time? Something like that could prove useful in underwriting or evaluating QA risk. But is that good for contractors?
In Construction, What’s Good For One Is Seldom Good For All (…Unfortunately)
First, let’s set aside the largest GCs—many of whom likely have their own proprietary QA/QC processes. Let’s talk about the midsize GCs and large specialty subs. Is a standardized Quality metric or “score” good for them? Internally, sure—few would argue with that. And for the consistent ones (i.e., those who align Quality with profitability), even metrics shared externally could be good marketing. But it’s also one more thing to worry about—one more algorithm to “game.” I’m kidding, that never happens.
In this two-part series, we’re going to explore Measuring Quality in construction. The purpose of this series is to ask tough questions of the industry; and to inform the BuiltWorlds community about tech-enabled QA/QC in construction today—and then let you decide what, if anything, to do about it. In this 1st installment, we’re going to ask questions like, who benefits and what do we measure—and we’ll introduce a few startups and forward-thinking providers trying to make your QA/QC life easier. Then, following my August 19th discussion with Brian Kramer of QualityBuilt and Kirk Chamberlain of HUB, we’ll publish the 2nd installment, recap the important takeaways, and discuss next steps (…register here).
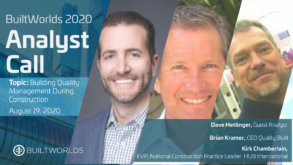
Is It A Good Idea To “Measure Quality”—Or A Fool’s Errand?
The tech enthusiast in me believes (…genuinely) that there’s tremendous value in establishing consistent metrics for the construction industry and using tech to measure it. But the cynical part thinks maybe we’ve measured everything else, and Quality is the last frontier. I picture a new-to-construction Data Scientist looking at Quality (personified), standing in the corner…not wanting to be measured. Instead of letting it be, the Data Scientist says, “No, don’t worry Quality, we’ll find a way to measure you.” And now we’re forcing Quality to be something it’s not. Are we forcing it—or is there more to it?
In an ideal world, of course we’d like Quality to behave like its more mature sibling, Safety—by replacing recordable incidents with predictive analytics fueled by computer vision—in other words, make it more tangible than before—and cooler. But Quality feels different than Safety. Playing devil’s advocate, isn’t it enough to measure cost, schedule, safety, productivity, and everything else that we already measure? Wait, what problem are we trying to solve again? It’s a lot to process—and it’s hard to stay focused.
The truth is that most of the contractors reading this article know their rework numbers (on average). And all are actively trying to lower those numbers with each successive project. And, if they cared to humor you, they could also give you a short, accurate list of the reasons “why rework occurs” on their projects, what they look for, how to prevent it, etc. And how “rework” is often a misnomer—one that is more accurately rooted in “design coordination issues” for example, rather than true “rework.”
Tech Can Help Us Achieve “First Time Quality” In Construction
And yet, at the same time, there are some proven tech-enabled solutions out there helping contractors improve margins by minimizing rework—helping them achieve that elusive “first time quality”, a term borrowed from manufacturing. <We so want to be manufacturing, by the way>. Unfortunately, in construction Quality is much more subjective than its siblings: Safety, Cost, Schedule, And Productivity—but you’d be amazed at how quickly Quality morphs into those things (…and others), in conversation.
Here’s a list of words and phrases that surfaced when discussing Measuring Quality: checklists, rework, specs, inspections, punchlists, quality assurance (versus control), things just slipping through the cracks, accidents or errors, warranties, construction deficiencies, owner expectations, constructability reviews, construction defect litigation, non-conforming work, best practices, proprietary processes, know-how, etc. The takeaway: Quality is a lot of stuff—most of it hard to measure…and even harder in real-time.
Good News—Help Is On The Way!
Okay, you get the point—Quality is hard to measure. The good news though is that BuiltWorlds recently identified a short list of companies working hard to make your quality assurance and quality control life easier. Note: All of these were first mentioned in the BuiltWorlds Top 50 Project Software List.
- QualityBuilt –Backed by a team of architects, engineers and inspectors, QualityBuilt has developed a purpose-built software platform and robust proprietary database that addresses construction risk, encourages collaboration and delivers qualitative and quantitative data – allowing builders to effectively make informed business decisions.
- FTQ360 – The FTQ360 team believes that defects are preventable and that achieving First Time Quality construction is possible for everyone. First Time Quality focuses on building it the right way the first time, more and more often, and ultimately every time. And that’s why they created the FTQ360 Software Platform with a range of advanced features to help ensure compliance.
- TruQC – Paperless reporting software that allows you to report, track and analyze everything you need for compliance and beyond. TruQC’s offline-capable iOS app with a web component and highly secure, cloud-based software presents an easy-to-use interface for field users, and the knowledge of industrial processes makes sure the framework fits the way you work.
- Agile Frameworks –Agile Frameworks’ vision is to provide consulting engineers with impactful tools and automated processes making their firms leading companies that connect the construction network. In turn, this enables measurable efficiencies and great profitability so they can be leaders during the unfolding technology disruption in the construction industry.
- CloudVisit – By using CloudVisit’s leading maintenance, repair, and operation (MRO) software, inspectors can review a site without ever leaving the office—cutting travel time and expenses as well as the costs of keeping on site workers waiting for inspectors to arrive. Instead, site workers can capture images and video recordings and note the project progress.
How Often Do We Take Quality For Granted?
Probably more than we’d like to admit—but those of you who’ve experienced a problem project rooted in Quality issues may be the exception. Construction defect cases are a mess. Typically, lots of parties involved, very contentious, and rarely ends well. I’ve seen a single case involve an owner, an owner’s rep/CM, the GC, multiple subs, the designer, and the insurer—ALL as named parties. It settled.
And yet defects still happen, all because someone somewhere cut a corner…or something inadvertently slipped through the cracks. It happens. Sometimes it is just an accident. True story: The Supreme Court in Michigan just ruled that an “accident” (…installing expansion joints backward) was covered under general liability. I mention that not because of the legal implications—perceived by some as a “win” for contractors, and a “loss” for insurers. I mention it because when we talk about Measuring Quality, THAT is the problem we’re all trying to solve: preventing “accidents” or defects in real-time.
If we’re able to do that as an industry, we’ll be able to avoid the unnecessary, incremental costs that follow—including the costs that are “baked in” as well as those incurred after the fact—as part of a lawsuit. Those costs are often significant. The key question, however, is how do those costs compare to the cost of a reliable, tech-enabled oversight tool? Or the cost of consistent metrics? My guess is probably miniscule in comparison—don’t you think? That’s what we’re going to find out.
Once there are construction companies out there that are clearly and effectively addressing the quality issue (…in the same way Toyota did with the automotive industry), those companies will start putting others out of business…and then people will start to care. Join us on August 19th as we continue the discussion.
Contributor Bio (BuiltWorld members can also click through Dave’s bio thumbnail below for more on Dave, items he has contributed, and to connect with him):
Dave has spent his entire 15-year career analyzing problem projects, and helping owners, contractors, subcontractors, engineers, and architects recover from cost overruns and schedule delays—and he’s been very fortunate to learn from experiences with over half of the top 20 ENR contractors on a wide range of projects. He started Entropy.Build LLC in the wake of COVID to help clients leverage their data and technology to resolve disputes in real-time, thereby avoiding the incremental costs that follow.
Dave can be reached at: dhettinger@entropy.build. Please note: any ideas expressed in this article are the contributor’s own, and do not represent the views of Entropy.Build LLC’s clients, past or present.
Discussion
Be the first to leave a comment.
You must be a member of the BuiltWorlds community to join the discussion.