This article was submitted as part of BuiltWorlds’ Verified Contributor Program.
Recent advancements in robotics, paired with the tailwinds of a worsening skilled labor shortage, are steadily driving interest and acceptance in integrating robots into construction sites. Many on the frontlines, ourselves included, are finally witnessing the impact of robots in executing routine, repetitive, yet transformative tasks such as layout, rebar tying, drywall finishing and painting – all of which are well suited for robotic efficiency.
The productivity gains on these tasks are measurable, and the robots are more resilient as they only require a narrow spatial awareness. Additionally, robotic automation of dangerous tasks like welding, picking and lifting, and operating heavy machinery present opportunities to improve the safety of the construction industry.
However, despite the considerable promise of robotics in construction, the hurdle of return on investment (ROI) remains.
To accurately evaluate the ROI of deploying a robot on a job site, general contractors (GCs) must compare the cost of “labor hours of traditional work” to the cost of “labor hours working with the robot, plus the cost of the robot subcontractor and additional detailing and coordination costs required for the robot” (Brosque and Fischer, 2022). The context in which this ROI assessment is conducted – whether on a single project or across multiple projects – is a critical factor.
Currently, ROI evaluations often occur within the scope of a single project, which is subject to a high-degree of variability and uncertainty. As GCs typically operate within razor-thin profit margins to meet project timelines and budgets, such risk-laden ROI scenarios may potentially hinder the adoption of this technology.
For example, in erecting a single commercial high-rise concrete building with steel reinforcement, many dozens of prefabricated rebar cages may be constructed, delivered and assembled onsite. If the GC elects to utilize robotics to prefabricate some of the cages, they have to purchase the robot themselves, lease the robot or subcontract out the work to the robotics company.
- In the first case, there may be heightened costs associated with the upfront equipment purchase as well as managing and leveraging the technology in house.
- In the second scenario, the initial cost is mitigated but the internal production costs remain.
- In the third case, the initial partnership risk and short contract lifetimes may not optimize contract value.
In any case, the GC may not realize the full potential of cost savings on this single project.
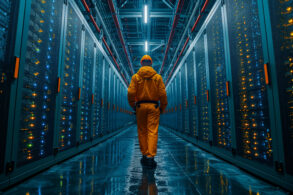
However, deploying the same robotic solution across multiple projects and assessing ROI across that broader scope could yield a more favorable result by minimizing upfront costs and standardizing customization and contract prices. We believe that for GCs to fully realize the substantial cost savings promised by robotics, they must establish multi-project, longer-term deployments funded through corporate budgets. This approach spreads ROI variability across projects, increasing the likelihood of favorable outcomes.
The biggest challenge with this strategy is that it hinges on greater project pipeline certainty. To date, this has been quite difficult to achieve for most GCs due to the constantly shifting macroeconomic environment, market demand, policies and regulations, and competition level, greatly reducing pipeline visibility. However, two strong factors are increasing project pipeline certainty:
- The emergence of the data center construction boom is showcasing a voracious appetite from organizations to build at scale, with data center capacity under construction surpassing 5.3GW in 2H23, according to a JLL report. In addition to these new facilities, existing centers are undergoing expansions to meet the rapidly growing data volumes and AI power demands. The construction cycle promises to remain lengthy as both existing and new facilities face risk of obsolescence in this environment, with experts recommending the “staggering of investment and a phased approach to development.”
- The rollout of funding of the Bipartisan Infrastructure Law is bolstering project pipelines across various sectors such as roads, bridges, airport terminals, and ports, among others.
Not only do these two catalysts present GCs with longer pipelines, but they also lend themselves well to robotic adoption. These projects are often located in areas with scarce population density, where traditional labor solutions like large-scale labor camps are increasingly unfeasible. Additionally, the systematic and repetitive architectural design of data centers in particular minimizes project-to-project variability. Therefore, in our eyes, the confluence of these factors creates an ideal environment for construction robots to finally thrive among GCs executing their robotics roadmaps.
MetaProp Co-Founder and General Partner Zach Aarons is a leading proptech investor, and also a professor, author and speaker on real estate technology. MetaProp Director Sage Shamsai is on the firm’s Investor Relations and Innovation Services team. MetaProp is a New York-based venture capital firm focused on the real estate technology industry.
Discussion
Be the first to leave a comment.
You must be a member of the BuiltWorlds community to join the discussion.