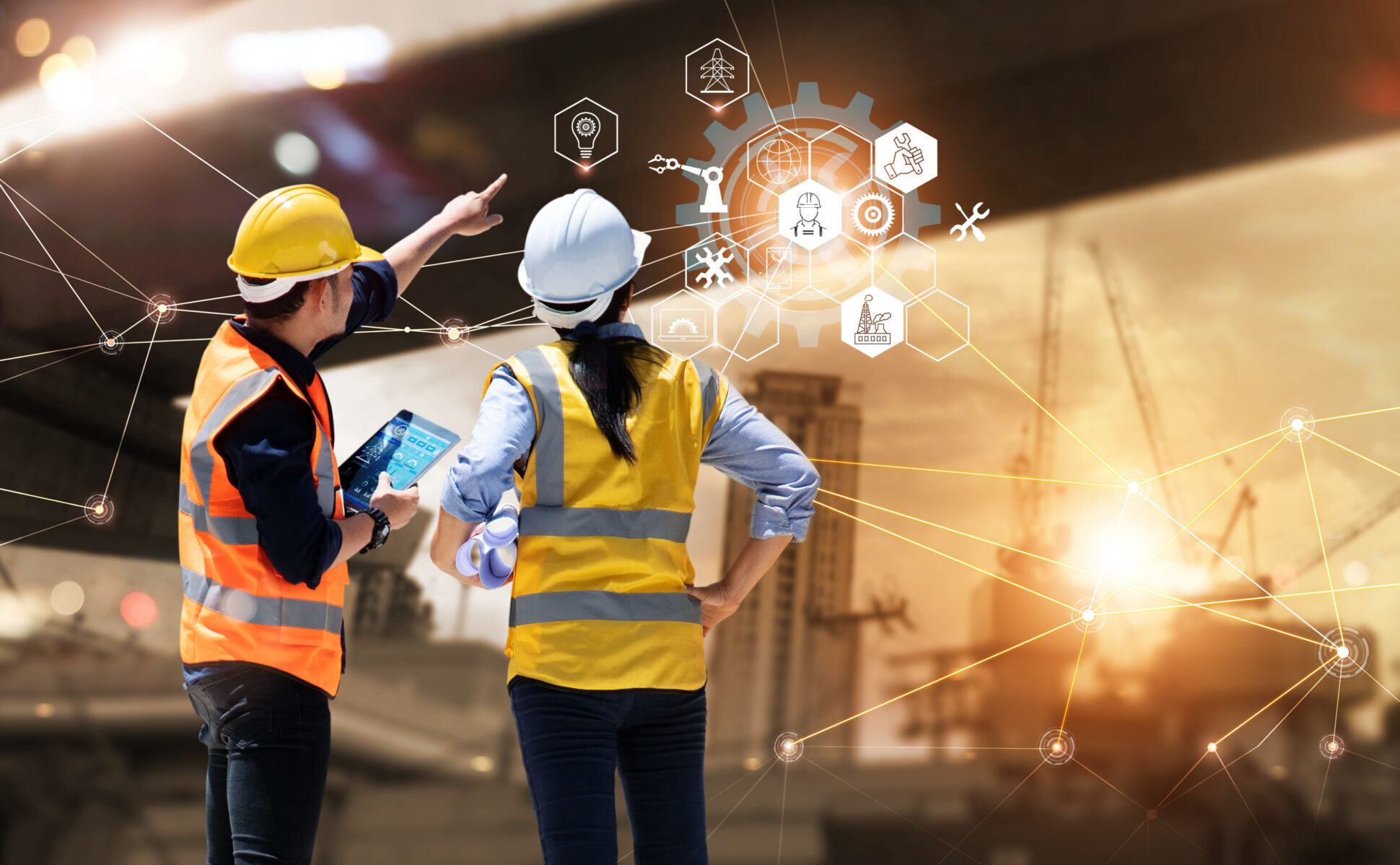
Construction is not an industry of rapid change. In fact, according to McKinsey, the AEC industry has been one of the slowest to adapt to innovation and digitize.
But, change is on the horizon.
As the construction industry faces a critical deficit in labor, along with an aging workforce, many in the industry are hopeful that traditional labor can be supplemented or enhanced with modern technology.
The possibilities of supplemental and augmentative technology in the construction industry are seemingly endless, with powerful promises of automation and optimization coming as a result of advancements in robotics, AI, reality capture, and the list goes on.
As the industry looks to potentially solve its persisting labor problems through innovation and new technology, companies face one universal challenge: the best technology in the world is ultimately worthless if people don’t use it.
The BuiltWorlds community will be gathering on March 5-6 to discuss the labor challenges and opportunities facing the construction industry at the 2025 Future Workforce Conference. In the lead-up to this event, we asked Dr. Jit Kee Chin, chief technology officer for Suffolk, and Dr. Chris Young, director of workforce development for the Texas Department of Transportation, how companies can successfully cultivate internal buy-in and implement efficient deployment of new technologies.
Not Just For Tech’s Sake
Once a new technology is identified for implementation, explicitly naming its benefits to the workers who will be using the tech is crucial to gain buy-in, particularly for technology that will be used on jobsites.
“If you’re pushing technology for the sake of technology, there is no interest,” Chin said. Instead, she adds, there must be a clear reason for the change and that reason should directly tie back to the workers who will be implementing the change day-to-day.
Importantly, professional jobs in construction, including engineers, planners, designers and analysts, are just as “technically savvy” as counterparts in other industries, often because technology is included in the education and training for these roles. Yet, Young recognizes a “gap for maintenance and operations teams,” when it comes to adopting new technologies and the need to specifically target these groups during company-wide buy-in initiatives.
One of the biggest hurdles new tech must overcome is that many of the techniques and processes that take place on jobsites are deeply engrained into workers, often having been honed over decades or even centuries.
“They’re comfortable doing it that way because it works for them, it’s part of the culture,” Young said. When introducing new technologies into this traditional environment, there has to be an explanation for how the tech “will make this (process) go faster, be safer and more efficient” in order to get buy-in from workers.
You Can’t Change Everything At Once
Sometimes, getting buy-in starts with implementing smaller measures that aren’t as flashy as AI and robots. Ergonomic tools that reduce injuries may lack the electronic component typically associated with new tech, but are an easy first step companies can take to introduce innovation on the jobsite.
“These are probably the half measures that are a little more palatable,” Young said. Highlighting lower-tech innovations, he adds, that don’t require much change from workers, but have a visible, positive impact on their quality of life, can open the door to bigger opportunities for innovation.
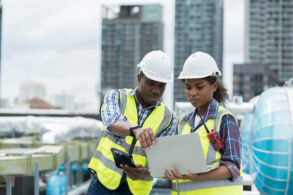
Communications is another area in which easily-implemented technology can generate significant returns on efficiency and productivity. While office workers are almost always provided a company email and frequently provided a company laptop and cell phone, many companies do not offer the same communication tools to field workers. While the Texas Department of Transportation, for instance, provides email addresses to all employees and cell phones for most field workers, according to Young, other “peer departments of transportation don’t even provision email accounts for their employees.”
Without access to these communications technologies, workers are “left out of the loop and seen as different from the in-office folks,” according to Young. Company-wide updates and other information are left to trickle down through site supervisors, he goes on to explain, which can hinder culture-building initiatives and other important communications.
“We’re trusting our folks with multimillion dollar projects,” Young said. “Why aren’t we trusting them with a $400 refurbished laptop?”
Shifting Attitudes Towards Technology
It’s possible that there’s a “generational shift” happening in the industry, according to Chin, where younger workers just joining the field “are more open to technology than someone who’s already perfected their way of managing the job.”
Catching these younger workers while they are still relatively new to the workforce and more malleable may help speed along the adoption of innovative technology as older generations retire or leave the construction industry.
On the other hand, workers of all ages are now likely carrying and using personal smartphones, which have reportedly rivaled the processing power of traditional PC computers for over eight years. When faced with a “sticky situation” while alone on a jobsite, Young asserts that workers are likely to pull out their phone and look to solve the problem themselves using Google and other online resources.
“They’ll see that someone has done this concrete form this way, and (say) ‘I’m not out of line if I do it this way and it works,” Young said.
In this way, the increased accessibility of technology in our day-to-day lives may make implementing technology in the construction industry easier. Workers who would not generally use the internet or computers in their jobs are becoming more tech-savvy in their personal lives and are, in turn, bringing that technology onto jobsites themselves without a directive from upper management.
Successful Implementation Strategies
In instances where technology is identified and implemented from the top down, Chin points out that successful deployment relies on “thoughtful change management, as well as piloting and scaling (processes).”
For Suffolk, this means first experimenting with a new technology before implementing it on three to five jobs to validate that it can deliver value, especially compared to the cost of the technology. This process will also determine if the technology is helpful on a broader scale or only in specific operational situations. If it’s determined to be helpful on a broader scale, then Suffolk will complete a scaled pilot across multiple situations and jobsites.
If the pilot is successful, the technology will be integrated into day-to-day operations over time with communications, legal questions and SOP build-out handled by the change management team.
“First, you need to find the right project with the right champion to experiment with, then you need to thoughtfully evaluate the net benefit of this tool,” Chin said. “Then, you need to (question) how do I integrate this tool a little more—but not all the way—into what people do day-to-day.”
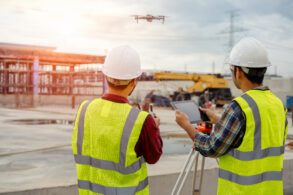
Chin and her team at Suffolk Technologies, a differentiated venture investment platform closely affiliated with Suffolk, help experiment with new tech before handing it over for the piloting phase. The Operations Excellence Team, Suffolk’s central team responsible for project performance and predictable delivery, then handles the change management strategy, including standardizing processes, building out SOPs and managing communications.
Young agreed that change management and “a robust communications plan” are vital to a successful implementation, recounting instances where tech was implemented without a change management strategy. In these cases, the responsibility of ensuring the technology was adopted and properly used was then put on users and super-users or champions, rather than on the team that was spearheading the change.
While overrelying on users or champions can bog down implementation, Chin sees value in engaging users who can advocate for the product within the company and offer perspective and direct feedback to the operations team as they bring the technology to scale.
Chin’s advice to companies looking to implement innovation is to “get tech in the hands of project teams” while staying vigilant on receiving feedback to understand how the technology is being used and what value is being delivered.
“The best job you can do,” Chin added, “is to bridge between the realities of your project team and the technology.”
Chris Young will be speaking at the BuiltWorlds Future Workforce Conference on Thursday, March 6th, as part of a panel titled “Pioneering a Culture of Innovation and Positive Changes for All Levels of the Workforce.”
Discussion
Be the first to leave a comment.
You must be a member of the BuiltWorlds community to join the discussion.