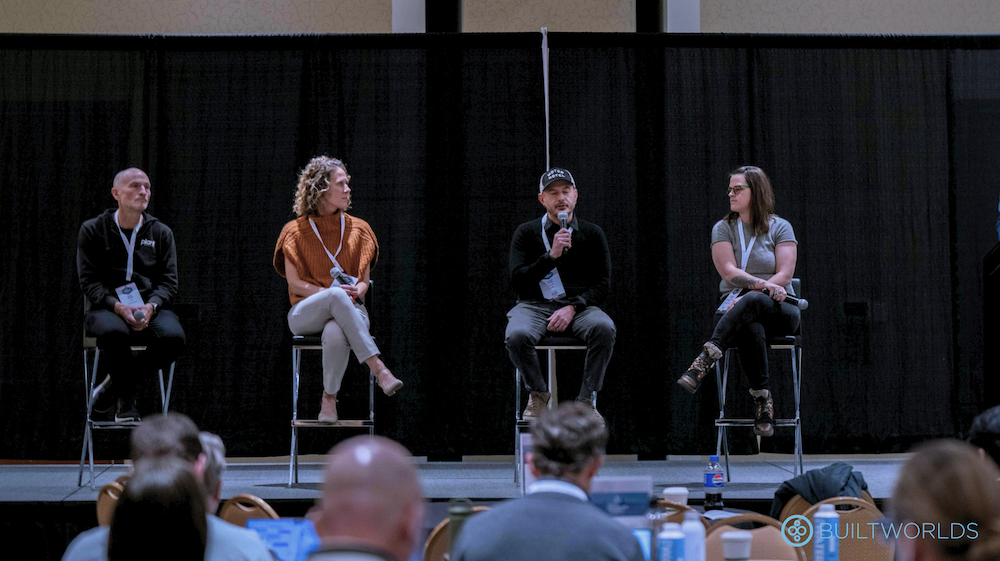
One of the best things about working on industrialized construction (IC) is the diversity and dynamism of the space.
You might spend a lot of time working on one system or segment in IC, only to turn around at a conference and meet others looking at it from a different angle. It’s particularly interesting now because of the amount of “idea-churn.” Everything from software interoperability to plant operations to product development processes is wide open for innovation. The deeper we get into developing IC platforms, products and systems, the more latent potential is discovered.
There’s a business development aspect to networking to be sure, but what gets me out of bed in the morning is the idea of working with innovators, the combinatorial potentials of innovations and how the execution works rather than just the size of a particular deal.
I was on a great panel this past December as part of BuiltWorlds’ Offsite Construction Conference, with Lisa Podesto, Michaela Harms, Steve Glenn and Stephen Anderson, discussing the potential for more advanced materials in IC, that was just a case in point that I think is worth sharing
The conversation generated four key takeaways that I’m going to spend some time thinking about this year.
Focus on the Trend Line, Not the Initial Cost
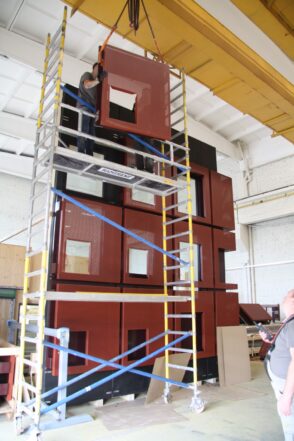
All IC efforts, by definition, incur a set-up cost that is higher than just the conventional procurement of the part.
The question for the owner is about the trend line vector: How quickly can I recover the setup cost? How much better is my sustained performance over time, having made the investment?
The key concept here is that IC introduces a set of systematized controls that were just not available previously, so the owner gains an ability to respond and adjust that trend line over time in a way that just isn’t possible with conventional procurement. This is one reason selecting the right product mix to start with is so important: if you focus on the wrong thing, you can spend a lot of time and effort that doesn’t sufficiently move the needle.
Done correctly, IC provides the owner a meaningful market advantage over conventional construction precisely because of the ability to calibrate products to achieve desired performance characteristics—which brings us to the next point.
IC enables Performance Tuning of Buildings and Components
The three basic performance characteristics in IC that drive the bottom line are cost, quality and speed. But these are merely initial performance thresholds.
The ability to cost-effectively engineer the technical performance of the component on a long term basis in IC is on a different order than what is available in conventional.
High tolerances, process engineering and CNC tooling provide IC materials a high Embedded Value. | Image: Sterling Structural
Thermal, mechanical and visual performance characteristics for example, can be calibrated and integrated much more precisely and to much greater effect than would otherwise be possible. Recall that 80% of the cost of ownership of a built asset is incurred during the operations phase and not the acquisition (i.e., construction) phase, so tuning the component for operational performance is where the money is for the owner/operator.
Building owners that are looking to achieve those higher performance thresholds now have a much more robust toolset to work with thanks to IC’s combination of digitization and manufacturing methods.
IC Materials Contain a High Embedded Value
Industrialized construction typically utilizes materials and components that represent a higher embedded value than conventional. For example, a cross-laminated timber (CLT) panel can be precisely notched and drilled with a very high level of accuracy (see above image). Where nominal timber framing members can swell and shrink due to moisture and humidity, CLT panels have very good dimensional stability, with dimensional tolerances that rival aluminum without giving up the ability to be drilled or sawn easily on site.
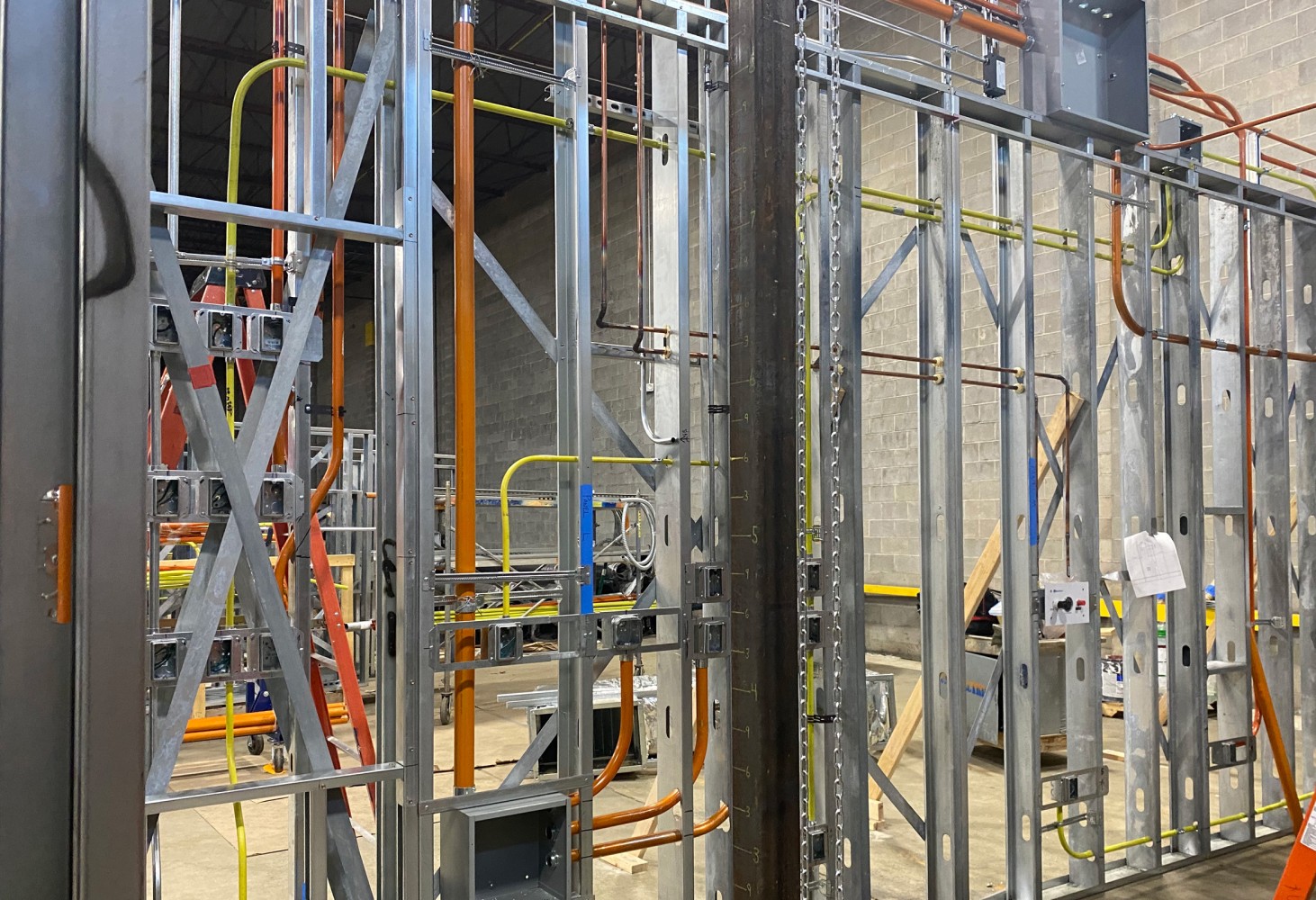
The complex multi-trade assemblies that are made possible by IC (see below image) are one of the few strategies available that can reliably and cost effectively support advanced components such as internet of things (IOT) and other next generation components and distribution within the build out.
Industrialized Construction ‘Intangibles’ Increase Bottom Line
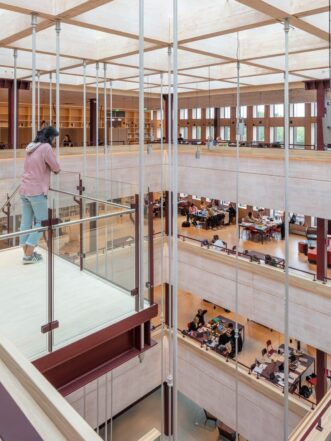
This was a wonderful point made by Lisa Podesto on her strategy of including a line item value for intangibles when she scopes alternative options that include IC products like CLT.
This is a powerful idea. In my experience, cost comparisons between IC products and conventional will often omit any value for these “intangibles.” For example, a CLT ceiling may get compared to a conventional option with a painted drywall finish without accounting any value for the feel and texture of the finish.
But capturing value for these ‘intangibles’ is important. At the end of the day, this is what owners really want: reliable performance from the build out and exceptional spaces for users. We must not shy away from representing that value in any cost/benefit analysis.
Fouad Khalil is the principal of Modly, a company providing market research, feasibility analysis and advisory services for modular and offsite construction.
Discussion
Be the first to leave a comment.
You must be a member of the BuiltWorlds community to join the discussion.