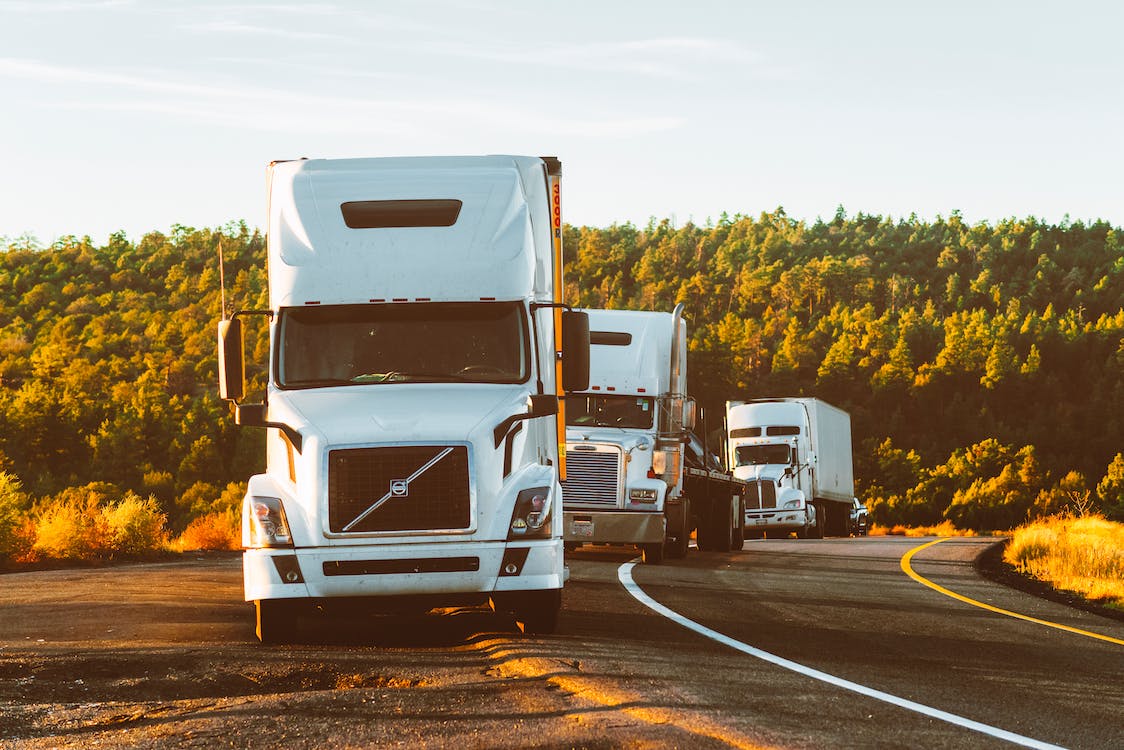
It comes as little surprise that offsite construction has the potential to revolutionize the building industry by offering faster, more efficient and more cost-effective methods of construction, especially in regions where sustainability is a priority. This approach involves manufacturing prefabricated building components, systems, or full volumetric modules in a controlled factory environment before transporting them to a jobsite for assembly. Central to the success of offsite construction is a well-coordinated supply chain, which ensures that materials and components are available when needed, maintaining the efficiency and cost-effectiveness of the process.
As such, BuiltWorlds’ June 12 analyst call attempted to tackle the question of how the AEC industry can enhance the supply chain to make offsite construction not just viable, but in some cases, the optimal project delivery method. Justin Schwaiger, General Manager of the US with KOPE; Armelle Coutant, Co-Founder and CEO of Kit Switch, and Vikas Enti, Co-Founder and CEO of Reframe Systems joined the webinar to share their insights on supply chain technology and offered a few possible ‘best practices’ from each of their unique perspectives.
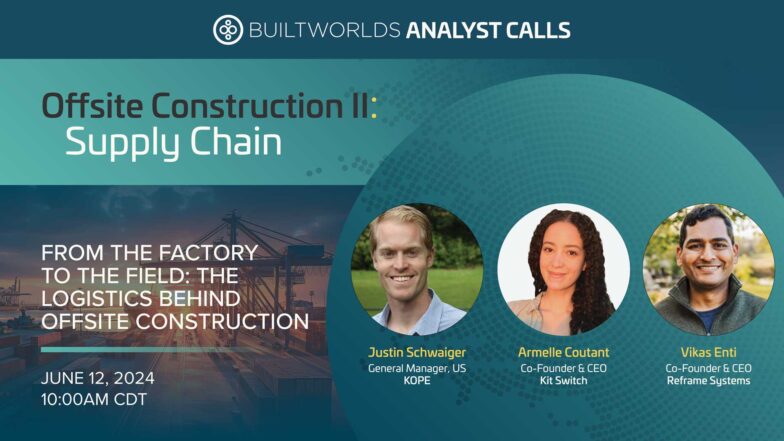
Lessons Learned From the Experts
The Role of EPDs, Disassembly and Inventory Management to Promote Supply Chain Transparency
Zooming out, having a clear line of sight into your supply chain is integral for companies to adhere to varying sustainability standards and ensure lead times are within reason—our guests identified EPDs, disassembly, and inventory management strategies as three ways builders and manufacturers can promote supply chain transparency and minimize the possibility of schedule delays.
Environmental Product Declarations (EPDs) enable companies like Kit Switch to share information about their pre-certified products that meet various green building standards. EPDs also offer standardized data on the environmental performance of products, enabling stakeholders to make informed decisions and demonstrate sustainability credentials.
Similarly, disassembly and inventory management strategies are both pivotal in promoting supply chain transparency by providing detailed information about the environmental impact, lifecycle, and traceability of building materials and components. Disassembly strategies ensure that components can be easily separated and reused or recycled, supporting circular economy principles and reducing waste. Effective inventory management, facilitated by technologies such as RFID and IoT, provides real-time visibility into material stocks and movements, ensuring accountability and reducing inefficiencies.
Together, these three elements can enhance the transparency, sustainability and efficiency of the supply chain.
Leveraging Local Supply Chains
By leveraging local supply chains native to the area of your project, such as local lumber yards, companies can inherently de-risk logistics by not needing to build their own supply chain. Vikas Enti and the Reframe Systems team believe that “the building materials industry is [one of] the most optimized industries in terms of cost per pound of material.” Understanding that local suppliers and vendors can often deliver on the same day, Reframe doesn't have to sacrifice space to store general commodities, which helps them utilize their factory and make the most of their limited space.
Traditionally, navigating supply chain issues has proven to be one of the largest obstacles to offsite construction, supported by data from the BuiltWorlds 2023 Offsite Construction Annual Report and benchmarking survey.
The Role of Partnerships and Purchasing Agreements
Pulling insight from the Lean Construction Institute's Introduction to Industrialized Construction, written in partnership with the Industrialized Construction Group, "many of the changes required to embrace industrialized construction require a deeper relationship with the supply chain and trade partners (e.g., moving from design for intent only to end-to-end product design, or launching new supply chain management software)."
With the rise of DfMA, or design for manufacture and assembly, partnerships between designers, offsite manufacturers, and material suppliers are another fundamental area that needs to be welcomed for the efficient fabrication of building components. As relationships grow stronger, offsite factories can operate with more confidence knowing that the materials and supplies they need will be there when anticipated, resulting in the efficiency gains and sustainable benefits so often discussed.
Looking Ahead
It's clear supply chains are the backbone of offsite construction, playing a critical role in ensuring the timely, cost-effective, and high-quality delivery of building components and systems. As the industry continues to evolve, new technology will likely emerge to optimize material procurement and onsite delivery, further driving the success and frequency of offsite construction. By embracing these advancements, contractors, developers and offsite manufacturers can continue to meet the growing demand for efficient and innovative building solutions.
Join us in December for BuiltWorlds' first-annual Offsite Construction Conference in Raleigh-Durham, North Carolina! Click on the image below to learn more or contact research@builtworlds.com for more information to join/speak.
The December conference will also serve as the formal launch of the Offsite Construction Reach Track, a forum designed to cultivate small-group conversation and a tool to identify and understand trends and emerging technologies related to prefabrication and modularization.
Discussion
Be the first to leave a comment.
You must be a member of the BuiltWorlds community to join the discussion.