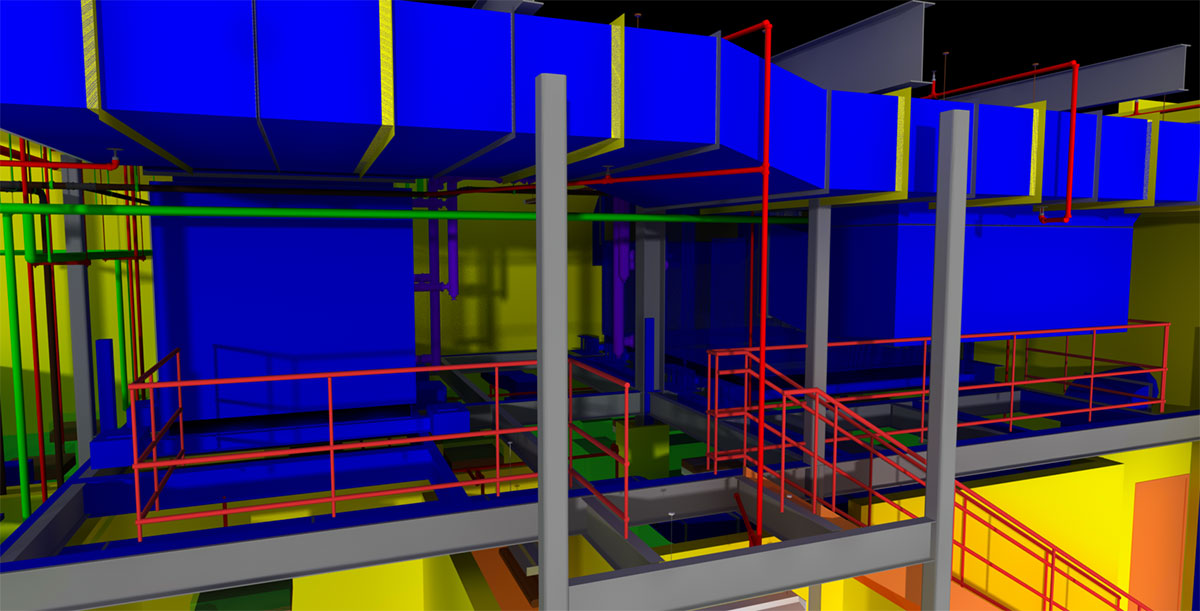
In less than a decade, the construction industry has been transformed by virtual construction – providing contractors and stakeholders with the ability to see a space and walk through it virtually before construction even begins.
Virtual construction is the process of creating true-to-size computer-based descriptions of a project, using Building Information Modeling (BIM) and 3D design instruments. These tools were once only used by architects and engineers, but have now been integrated into the construction industry and implemented by general contractors.
The built world is changing. Between the rapid adoption of technology and the shifts in the workforce, the industry looks totally different today than five years ago. Do you want to stay on top of these changes?
That's where BuiltWorlds comes in.
We provide our members with crucial insights and access to thought-leadership that will help them navigate this constantly-morphing industry.
Join our Member Network to attend our conferences and gain access to valuable research and insights.
An early adopter of virtual construction, and one of the first general contractors to create an in-house virtual construction team, Clune Construction sees 3D coordination as a natural progression in the construction industry.
“It’s a way to build virtually, starting with a 3D file from the architect, adding scan data and then further refining it with building trade input,” says Joe Zobel, Clune’s Vice President and MEP Coordinator. “The end result is a highly accurate road map for construction.”
Virtual construction streamlines the building process because when actual construction of a structure begins, it already has been built once before – virtually. The result is more accurate pricing and scheduling and the elimination of conflicts throughout the duration of the project.
It’s a way to build virtually, starting with a 3D file from the architect, adding scan data and then further refining it with building trade input. “The end result is a highly accurate road map for construction.
The ability to virtually see and walk through a project provides a tremendous advantage to all parties involved. To facilitate this, augmented reality glasses are used to blend the actual space with a holographic image of the proposed design, allowing the user to walk around the model prior to construction. This same technology is used during the construction phase as a modern quality control tool to allow the user to compare the model to what has been installed throughout the project.
In addition to being a design tool, scanned models act as a variance control tool, utilizing scanning equipment and software prior to construction to uncover the unknown. The contractor now has a real-life 3D “as-built”.
“If a picture is worth a thousand words, a 3D model is worth ten times that,” Zobel says. “Using advanced scanning and modeling technology enables contractors to capture not only accurate structural dimensions but also existing MEP infrastructure to 1/10 of an inch of accuracy.”
As one of Clune’s specialties is tenant interiors, they utilize virtual construction differently than a contractor might on a ground-up project. To overcome the biggest challenge with interior construction, which is a building’s existing conditions, Clune utilizes 3D scanning technology to capture the true dimensions of a building’s structural columns, ceiling heights, and walls and represent them in a 3D file that acts as a backdrop for the building’s trade designers.
Check out more BuiltWords content focused on construction technology:
As a result, HVAC items, such as ductwork and piping can be built offsite in controlled environments, minimizing waste and creating a safer jobsite.
When building meeting, presentation and conference rooms, where audio-video capabilities are always extremely important, virtual construction is extremely beneficial. It enables a contractor to ensure the accuracy of all measurements of audio-visual components for these types of environments before the project starts, saving significant time and energy during the actual construction process and avoiding conflicts by detecting and eliminating errors and inconsistencies, much earlier than otherwise.
“While interior construction projects use virtual construction differently than ground-up projects, it is still utilized in a similar way when it comes to what is at the heart of every construction project – effective communication,” explains Zobel. “Conflicts have already been resolved and things have been proven to fit correctly.”
According to Zobel, virtual construction can be useful on any size or type of project, as long as careful consideration is given to utilize the correct technology on each project. Clune Construction currently utilizes virtual construction on 80 to 85 percent of its projects ranging from commercial, to healthcare and data center projects.
Zobel believes the hardware used in virtual construction is improving at such a fast pace, it will soon allow for reality capturing equipment that is smaller, faster and more accurate. These improvements will also eventually make virtual and mixed reality technology available to the installers themselves, eliminating the need for drawings altogether.
This article was brought to you in partnership with Clune Construction.
Discussion
Be the first to leave a comment.
You must be a member of the BuiltWorlds community to join the discussion.