Boston-based Assemble Systems, purveyor of Assemble Insight, one of the construction industry’s most popular model data management solutions, is on the move with a mobile app that makes the leap from office laptops to construction sites of all shapes and sizes. Known for the deep data-driven decision-making it yields during preconstruction phase, Assemble has developed a user-friendly system that leverages 3D BIM models to promote greater productivity, quality assurance, and cost savings in the field.
All that’s needed is an Apple iPhone or iPad for contractors, including project managers, superintendents and foremen, to access the app, a system that combines high-performance model viewing and advanced data management to assess and address a variety of site issues and conditions.
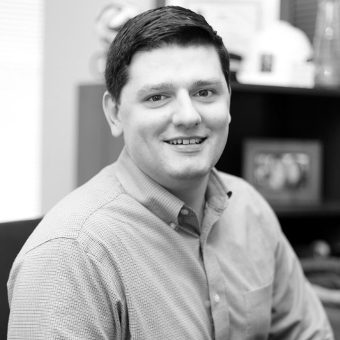
Although a mobile app has been pivotal to Assemble’s game plan for some time, growing demand added greater urgency to bringing the technology to market sooner rather than later, according to company product manager Tim Kelly. “We received a large volume of requests to develop mobile capabilities, particularly from general contractors, who rather than collecting field data and keying it in once they return to their offices, now can report information involving installation dates, status conditions and tracking issues directly from the field.”
App users can access all model data on Assemble’s cloud-based system, including visuals and information involving preconstruction, from design details and cost estimates to value engineering and schedule management. In short, Assemble users have at their disposal all the geometries, grids and inventory they’ve used for other applications. Accessing the information allows app users to leverage 3D data to address specific systems, scopes or objects on site in real time. “For large projects such as hospitals, we’ve made it easier to scan to reference a particular space or room,” said Kelly. “As you’re entering the room on site, you can call up the model and draw comparisons as you perform a walk through.
Users also can add specific assembly codes or status to any object to track activity in the field. “If you point the device at the bar code of a specific assembly and scan it, the app will call up the corresponding model,” Kelly said.
As a result, the app promotes numerous analyses following data gathering, said Kelly. For purposes of quality assurance, “Users can compare as-builts with components of the model, adding comments or identifying issues concerning a particular installation or system,” he elaborated.
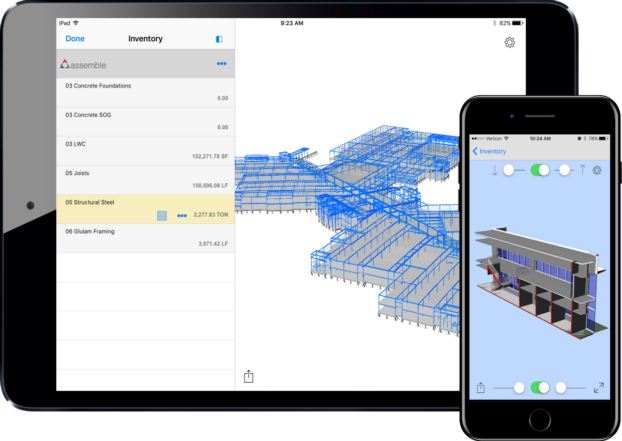
Users also can compare production to planned schedules, calculating, for instance, the actual amount of steel in the field as compared to anticipated tonnages for a specified time period.
The app likewise is useful in optimizing workflow. “If the project calls for four concrete pours over a specified period of time, a look at the 3D visuals and available quantities of material may assist in optimizing the sequencing of the pours,” Kelly said. “In turn, resulting information can be useful in managing budget and cash flows tied to the timing of corresponding pours. In some instances, the information may lead to consultations with concrete subcontractors concerning manpower during particular time periods.”
The app is capable of enhancing virtually all phases of construction, including testing and commissioning. “In anticipation of client handover, it’s vital to organize information in a manner that can be easily referenced in the future – typically by assigning a code to a particular space or object,” Kelly said. “For purposes of warranty, our app users can scan a component or system for start-up date or simply for status. They also can cross reference existing conditions with models as contractors perform walk throughs with inspectors or other parties.”
“The app is very easy to use,” Kelly said. “We can set you up in five minutes, with only an hour required for training.”
Release of the app is welcome news to users of Procore, provider of a construction management platform that seamlessly integrates with Assemble’s 3D data management solution, incorporating 3D model views into Procore’s project management workflows.
Founded in 2011, Assemble has grown at an astonishing rate that currently inculdes thousands of projects collectively valued at $50 billion. Kelly attributes the enterprise’s success to its flexibility, meaning “we provide customers direct access to whatever data they want to see.”
This article was sponsored by Assemble Systems.
Discussion
Be the first to leave a comment.
You must be a member of the BuiltWorlds community to join the discussion.