
The Role of Alternative Construction Methods in the AEC Industry
Offsite construction, encompassing both modular and prefabrication methods, has gained considerable interest in the construction industry in recent years. Despite not being a novel idea, this innovative approach involves assembling building components offsite in controlled factory conditions before transporting them to the construction site for final assembly. Understanding the potential upside, it's a growing concern for some modular players that several companies have ultimately closed their doors in the United States due to unique challenges traditional stick-built construction doesn’t necessarily encounter. Without further incentives or other mandates, the question remains if this will be a viable method for North American builders.
As such, BuiltWorlds has kept an eye on Offsite Construction over the past few months, paying particular attention to the current state of offsite construction, its benefits and discussing key challenges to its widespread adoption.
Offsite Construction Expert Mark Skender Addresses Industry CEOs
Last week, BuiltWorlds hosted its annual CEO Forum meeting as part of the Business Strategy Track, which provides an opportunity for industry executives to network, share, and identify key trends and innovations around the world as a means to shape the strategies within their own organizations.
In what was a packed two days of presentations and conversations with thirty of the most forward-thinking executives and leaders in the industry, the group heard from Mark Skender, former CEO of Skender Construction and now Co-Founder and CEO of RaaP, an industrialized construction platform looking to help the industry produce buildings faster and cheaper.
Pulling from Mark’s wealth of experience in the area, he provided several possibilities as to why “modular” has not lived up to its promise in addition to changes the industry needs to make to deliver.
Fallbacks:
1. Economies of Scale
2. Uncertainty of Cost
3. Lack of Standardization/Productization
4. Predictable Pipeline
5. Project Financing and Bonding
6. Risk
Necessary Changes From the Project Ecosystem:
Among the challenges that must be addressed, Skender discussed the following using the graphic as a reference.
1. Project Finance (Debt & Equity)
2. Developer Contributions
3. A/E/C Partners Involvement
4. Modular Manufacturers Creating a Product
5. Supply Chain
Source: McKinsey & Co., Modular Construction: From Projects to Products, June 2019
From the Newsroom: BuiltWorlds Coverage To Date
In addition to sourcing Offsite Construction visionaries for our members to hear from like Mark Skender, BuiltWorlds produces countless thought-leadership pieces propelling the conversation. Below are five of our most recent that speak to the prefab and modular construction landscape:
- In Modular Building, The Debate Rages Between Asset Heavy, Asset Light, and Asset-Digital Strategies - BuiltWorlds
- Canada Announces $600 Million Effort to Fund New Construction Technology - BuiltWorlds
- $6 Billion Canadian Government Fund Ties Infrastructure Money to Federal Zoning Rules. Is the US Next? - BuiltWorlds
- Taking Lessons from Katerra and Tesla, Aro Homes Builds Horizontally Integrated, Modular Housing Startup - BuiltWorlds
- Biden Administration Pushes Zoning Reforms, Manufactured Housing To Increase Affordable Housing Supply - BuiltWorlds
As alluded to in the first section of this briefing, the United States seemingly lacks the incentive to go all-in on offsite construction. However, especially when considering the affordable housing crisis and the influx of migrants in need of homes referenced in the articles above, offsite methods could be an interesting alternative to boost efficiency and quality.
However, realizing its full potential requires concerted efforts to overcome existing challenges and foster a supportive regulatory and market environment conducive to widespread adoption.
BuiltWorlds Research: Primary Benchmarking Data from Leading Adopters
As a data-first organization, BuiltWorlds leverages its various forms of research methods to pull key insights that are used in the annual reporting for each of our seven (and growing) research tracks.
Our annual Benchmarking Program serves as an objective, non-biased vehicle to capture the industry's perception, understand what technology is being used, how frequently it is being used, and, ultimately, derive satisfaction ratings. Much like the information Mark presented, data from the 2023 Offsite Construction Survey shows that 'Streamlined Project Schedules' was the most appealing benefit, followed by 'Sustainability' and 'Safer Working Conditions'.

Beyond sentiments, our team collects and analyzes satisfaction and utilization metrics for the solutions that our members identify. Prefabrication design solutions were not widely adopted among survey respondents. Only 28% of the 2023 Offsite Construction Survey respondents reported using a dedicated prefab design solution in some capacity, with just 7.7% of the sample using one for “every project.”
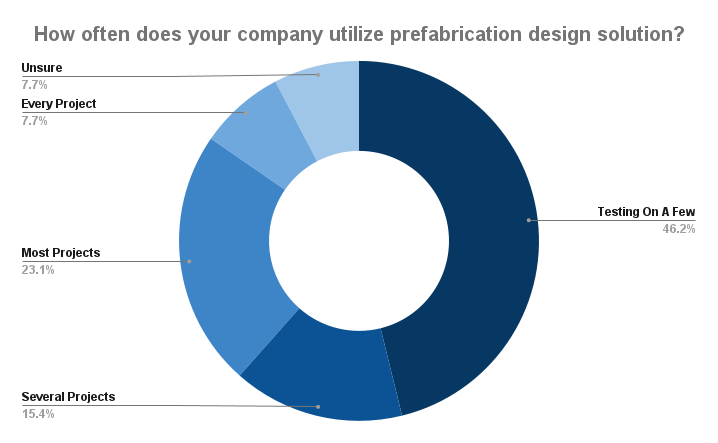
For more specific information regarding the specific solutions identified, read our research reports linked below!
Discussion
Be the first to leave a comment.
You must be a member of the BuiltWorlds community to join the discussion.