
Its name, Mechanical, Inc., is deceptively simple. With more than 500 employees at eight Midwest locations, the Northern IL-based company, one of the nation’s top 50 mechanical contractors, is involved in virtually every project phase – planning, engineering, prefabrication, construction, and maintenance. Building types are equally varied, from elementary schools to oil refineries.
Nearly two years ago, company leaders decided they required a greater grasp of new digital technologies seemingly poised to transform construction at every turn. Enter Travis Voss, who in February 2016 assumed the newly created post of technology manager for the vast enterprise.
Voss said the position wasn’t created for him, though it might as well have been. Since joining Mechanical, Inc., Voss, who was named one of BuiltWorlds’ Top 50 Tech Adopters, has investigated leveraging virtual, augmented, and mixed reality (VR), (AR), (MR) to improve operations, as well as removing silos that hamper the flow of critical information at various project junctures.
Here, he talks more about his role as technology manager with the firm.
Your interest in digital technology goes back quite a ways. When did the bug first bite?
TV: I’ve always had a knack for technology, and even took programming classes in high school, including basic programming, which at the time involved 286, 386, and 486 processors. From there, I later became involved with enterprise resource planning (ERP) that opened up the technology world to me on a professional basis.
While with Furst-McNess Co., an agribusiness, in Northern Illinois, I did some programming work to enhance and simplify the function of the firm’s ERP system, particularly its front end. I generated external facing programs to interface with its business partners and allow the commodity sales team to process orders more efficiently. Prior to joining Mechanical, I worked for a software start up that was more data-based and involved web service development.
Could you elaborate more on the digital technologies that prompted Mechanical to create your current position, that of technology manager?
TV: The firm’s leadership had a vision of a large digital transformation in construction that was going to require more than its existing personnel to take on. One of the chief components of that transformation is a paperless industry – one that more efficiently shares data by working off paperless models, or with virtual and augmented reality, with the recognition that more and more construction workers are retiring and the industry currently faces a labor gap. So, we look for technology to fill that gap, whether it be hardware, software, robotics, or what have you.
What types of technologies did Mechanical have in place when you joined it? Were there any gaps?
TV: The firm certainly was well established with building information modeling (BIM). I would say the main gap involved a fabrication data base for piping. As an industry, we need to become more diligent in addressing silos of data that don’t facilitate the flow of information through the enterprise, thereby hampering productivity and knowledge transfer.
As an example, silos frequently prevent the flow of information from bids to ERP systems, and from ERP systems to the project managers who develop the budget, and whose final costs may not circle back to estimating to improve the accuracy of future bids. As a result, I’ve been digging deeper to identify silos at Mechanical and working with the firm’s director of accounting to pass more data through the pipeline. I think there’s more we can do to leverage ERP.
Among your responsibilities is identifying technologies that will best benefit Mechanical and taking steps to implement them. What does the process typically involve?
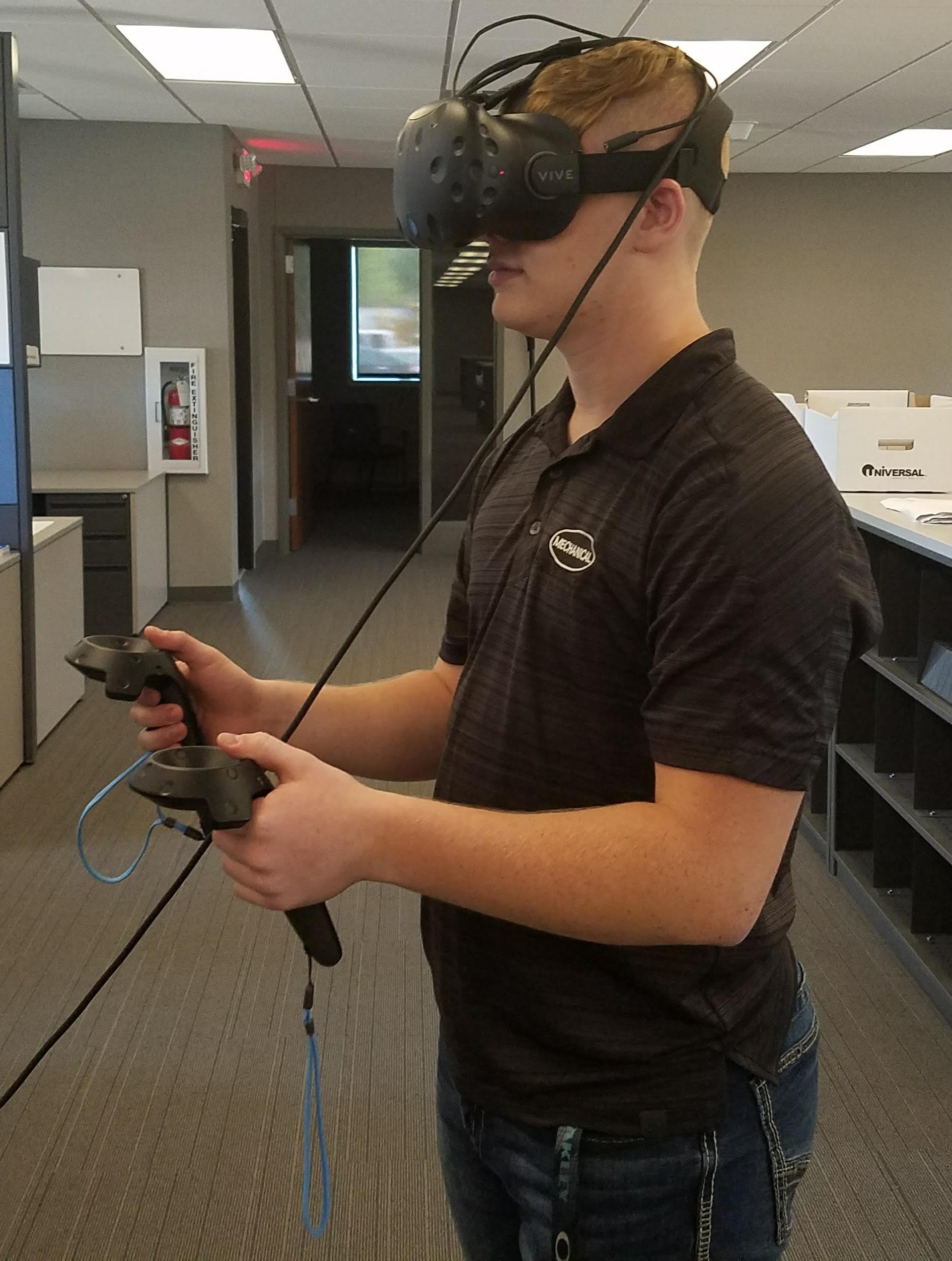
TV: I spend a lot of time performing research, attending industry events, and listening to colleagues about their processes. If those sources lead to implementation of a new technology, I’ll speak with a prospective vendor three or four times, then form a committee representing the user group to view demos and, assuming the technology passes muster, I’ll assist in implementation.
For example, we’re interested in implementing mixed-reality on projects, so we bought a pair of Microsoft HoloLenses. We probably spoke with about a half dozen vendors that publish BIM imagery on the HoloLens prior to making a selection.
I thought about writing a program myself, but in the end it made sense to make a selection among the candidate vendors. One important point: whatever we develop in our home office, we try to extend to our other locations.
To what degree has Mechanical been involved in virtual, augmented, and mixed reality?
TV: Prior to my arrival, other than dabbling with augmented reality on a few phones, the technology was new to the firm. I’ve been spending a lot of time with it now, pushing AR, MR, and VR into our existing workflows. Because virtual is immersive, it’s ideal for constructability reviews, QA/QC checks, and so forth during the design stage. It allows users to determine whether mechanical room dimensions will provide sufficient space to accommodate all required elements.
There are a lot of good modelers out there, but virtual brings it all to an entirely new level. We’re able to walk the space in AR, MR, or VR, which reduces risk before we fabricate elements and ship them to the site. Virtual reality also translates into a lot fewer mock ups, making the process less expensive.
Do you have an interest in implementing augmented and mixed-reality in the field?
TV: Yes. They add another layer of QA/QC. In this case you’re walking a finished mechanical room to ensure its dimensions will accommodate whatever part of the model you’ve overlaid onto the room, the difference being that with augmented reality, you’re viewing that information on a cell phone or tablet, but with mixed-reality, a device over your eyes that immerses you in the space. You get a better sense of it. As for implementation of virtual, augmented, and mixed reality, were still in the final stages of determining when to use it, at what point in the process it makes sense, and collaborating with stakeholders to learn more about when they may want to ask for it.
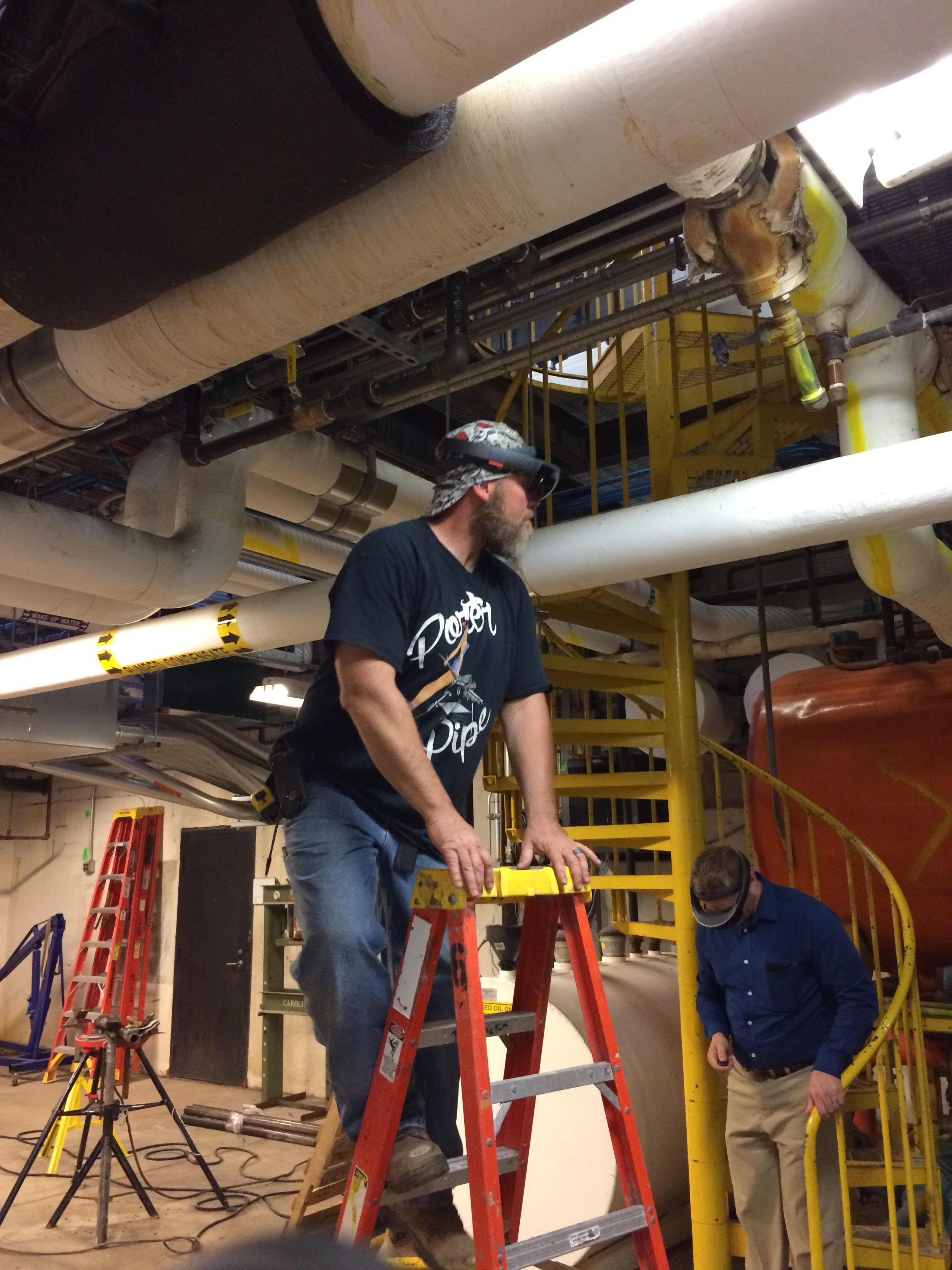
It’s been said you’re a huge proponent of enhancing worker safety.
TV: That’s true of Mechanical’s culture and, increasingly, that of the industry as a whole. We’ve been considering concepts ranging from robotics to exoskeleton vests, the latter of which assist in lifting and associated issues involving repetitive motion.
I’m also interested in performing analyses of materials and tools that improve efficiency while minimizing the number of physical steps taken on site, the goal being to eliminate slips, trips, and falls. There are also surveillance technologies to ensure workers are wearing their hats and avoiding no-go areas.
Do you see any huge technological disruptors on the horizon in the area of construction?
TV: I think there’s a huge discussion under way about transforming construction to something more like manufacturing. Rather than prefabricating parts, there’s the potential to fabricate entire rooms in Henry Ford style, with assembly lines that replicate tasks and emphasize quality. The approach would require considerably more up-front collaboration among stakeholders.
You’re Mechanical’s technology champion. What types of activities does that entail and how do you gain consensus among colleagues?
TV: It boils down to a lot of internal networking – learning the job functions of various workers and evaluating whether we can solve problems relating to those functions. It’s a continual feedback loop. When you adopt a new technology, you have to think of yourself as a start-up, regardless of how old your enterprise is. After a six-month trial, if the technology isn’t working, you need to abandon it and replace it with something else.
Discussion
Be the first to leave a comment.
You must be a member of the BuiltWorlds community to join the discussion.