Productivity: The Economists Perspective
Earlier this year, Chad Syverson, Economics Professor at the University of Chicago Booth School of Business, co-authored a research report alongside Austan Goolsbee, President of the Federal Reserve Bank of Chicago, on the topic of declining productivity in the construction industry. The report approaches the topic through various calculations comparing things like price inputs, labor productivity, and material productivity to broader global industries. What was found to likely be true, in every scenario, is that productivity in the construction industry was declining by roughly one percent per year on average since 1970, while it was steadily increasing for global productivity metrics by over two percent per year in the same time period. Over the 50 year period of measurement, this equates to a roughly 3x difference in the measured output of construction versus the global average for all sectors.
Below is Figure 1 from Syverson's & Goolsbey's report visualizing the trajectories of labor productivity in construction relative to the global average.
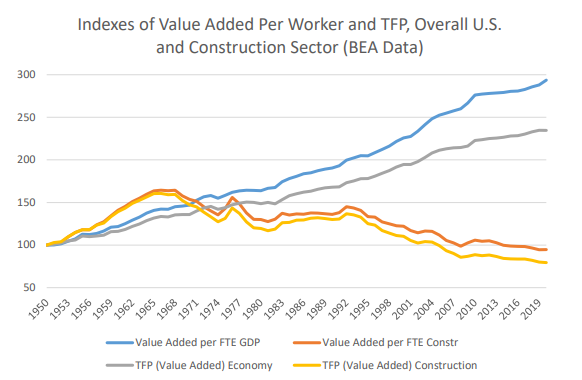
What does this mean?
Construction makes up about 4% of the United States’ total GDP for any given year over the last five decades. For this small piece of $1T of GDP, every year it requires more “input” to produce the required output of the industry. To (over)simplify Syverson’s & Goolsbey’s report, the same amount of work in place in the construction industry is more expensive and/or takes longer to complete now than it ever has, and is increasingly so. This means owners, developers, government organizations, and the broader real estate industry is paying more for the assets being put in place. Then, real estate acquisitions, leases, and other downstream expenses become more expensive, and so on. Extrapolated out, the loss of productivity equates to more capital required from all other organizations involved with building and infrastructure assets. That’s a bad thing right? Well, it depends on who you ask.
The General Contractor's Perspective
Once a problem is identified, it can start to be corrected. That is, unless those in the driver’s seat don’t actually see it as a problem. Construction has long been seen as a laggard when it comes to the adoption of technology. While many other industries have embraced and refined data collection, process optimization, and automation technologies, construction has struggled with all of the above. When looking at sectors like manufacturing, healthcare, consumer goods, banking, etc, technology allows them to cut costs, streamline services, and optimize the customer experience which all leads back to one goal - increased profits. When it comes to construction, however, it may not be so simple.
The vast majority of construction projects are paid on a “cost plus fee” basis, meaning the general contractor makes a profit based on an agreed upon percentage of the costs of the project. The more the project costs, the more fee they are eligible for. There are of course variations of this model, but in general it holds fairly true across both commercial and residential construction. If, then, the work becomes more efficient, thereby ultimately costing less to complete, contractors would not be able to obtain as much fee volume. Essentially, in certain instances, general contractors may be incentivized to not be productive in putting work in place.
This certainly does not extend to all activities or areas of the sector, but it may explain in part why the industry has been slow to adopt new, expensive technology. That said, there are also instances where it would greatly benefit general contractors to implement technology to become more productive. Good contractors are very good at managing and mitigating project risks, so any technology or process that can be implemented to demonstrably decrease risk areas are critical to the contractor’s tech stack. Let’s explore a few of those areas that contractors are heavily investing in.
Want to Meet Syverson?
Chad Syverson will be joining our 2024 CEO Forum Annual meeting as a speaker to provide more insights on the subject of productivity. Click here to learn more!
Document Control
By the time the 9th bulletin / addendum, 200th RFI, and 50th submittal package are through reviews and approvals, it is a project engineer’s nightmare trying to ensure the team is using the most up-to-date documents only, not the old versions. It is widely documented through various studies over the years that something as simple as poor document control has a significant, material negative impact on the cost and schedule of any given project. Though in reality, it is anything but simple.
General contractors are willing to pay significant sums for quality document control software because the increased productivity directly translates to protecting project fees by way of avoiding rework. This is why Procore has seen the significant rise that it has over the last decade, alongside Autodesk and Trimble who have both more recently moved to cloud project management applications. In fact, Procore claimed this past summer that using cloud-based document tools could increase productivity by 50%, a staggering number that would translate to direct benefits to their clients, general contractors.
Estimating
Setting up project teams for success is the most critical component of preconstruction teams everywhere. Drawing out lines in Bluebeam to develop quantities of square feet of carpeting, linear feet of drywall, or tonnes of structural steel, while not overly complex tasks, require capable, diligent estimators who can’t afford to make mistakes. All of that information needs to be populated and layered into logistics plans, schedules, and other plans required to understand, ultimately, how much a project is going to cost.
There has been significant interest from contractors in ensuring their estimating efforts are more productive and more accurate, leading to significant interest in solutions like DESTINI, Togal, ProEst, and others.
Site Logistics
A newer area of technology interest is in site management / site logistics solutions which enable project teams to coordinate delivery, staging, and other site operations in a digitized manner. While the days of superintendents receiving phone calls for deliveries are far from over, solutions like Plot, Voyage Control, Genda, and others provide project teams with the ability to more effectively view and manage jobsite operations. Oftentimes, poor jobsite coordination can lead to missed materials, improper material staging, or equipment use (i.e. tower crane) inefficiencies which comes at a cost to contractors. Providing opportunities to increase productivity in this way is a significant benefit to contractors today.
Interested to Learn More?
BuiltWorlds Technology Specialty reports provide you with the opportunity to review and learn about all the key technology solutions in particular areas of technology. Click here to view the library of reports!
The Bigger Picture
Aside from some of the above examples, there are many opportunities to improve productivity that are not entirely in the hands of the contractors, nor that would necessarily benefit contractors (though it still might). Ultimately, this would be a significant benefit to not just those cutting checks to the contractors, but those in many other sectors as well.
Modular construction has proven in certain areas to be significantly more productive than traditional construction methods. The ability to remove unforeseen conditions and reduce friction in the procurement and installation processes would provide significant benefits. Another example would be the implementation of robotics and other jobsite automation tools. At scale, the use of robotics is significantly more efficient than human labor hours when it comes to the installation of work. Lastly, streamlined and consistent permitting and regulation processes which allow owners and contractors to effectively request and receive approval required to build. “Hurry up and wait” is a significant source of inefficiency in the industry that can be mitigated through more productive review processes.
All this to be said, while it is well-documented that productivity is an issue in the industry, it is important to understand that while there is technology available to mitigate the issue, technology is merely a small portion of the opportunity to improve. It will take a much greater effort from those both inside and outside the industry to affect the change required to move productivity back on the right path.
Discussion
Be the first to leave a comment.
You must be a member of the BuiltWorlds community to join the discussion.