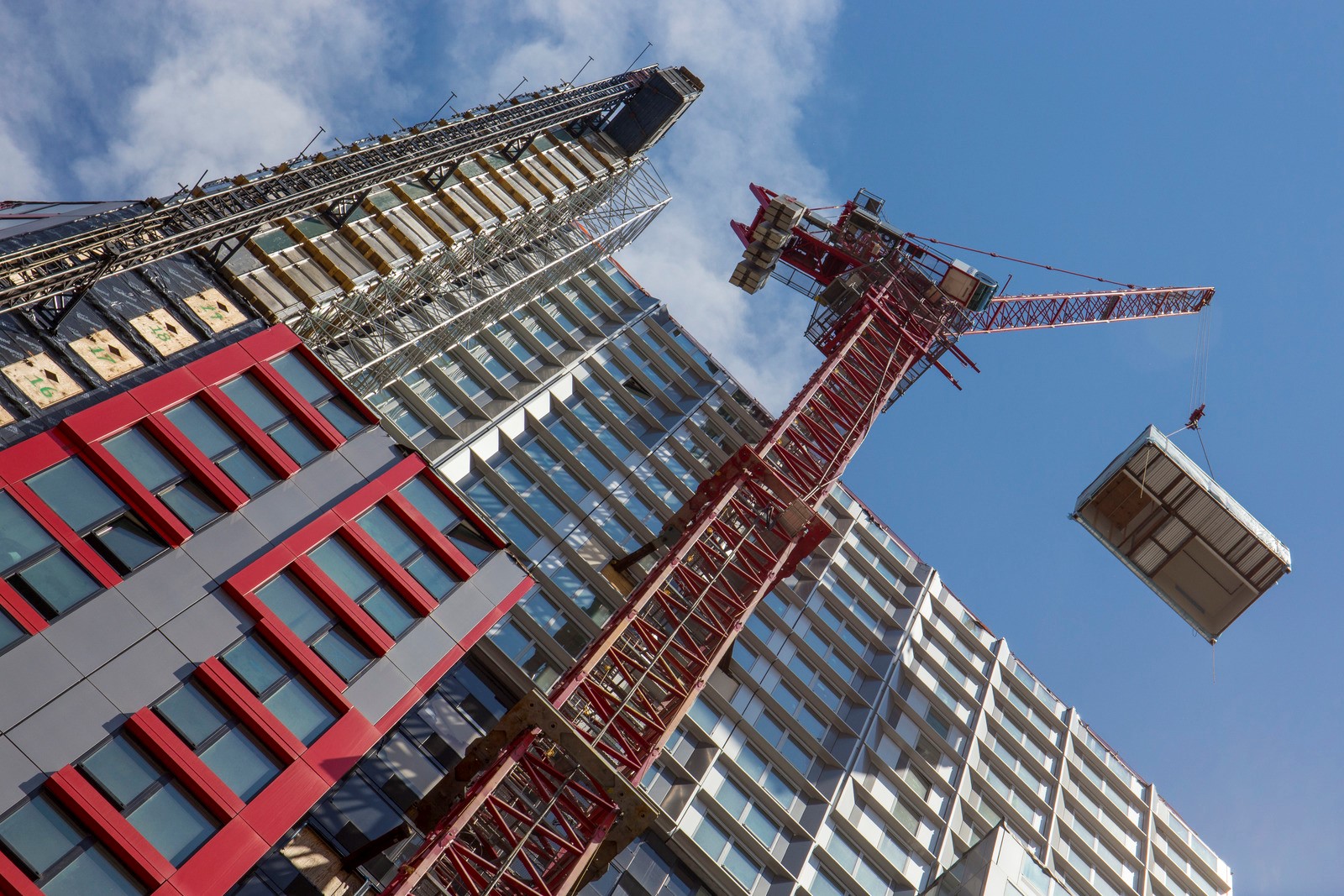
Moving Construction from Jobsites and Into Factories To Improve Productivity
Spanning across different sectors from single-family housing to high-rise office buildings, modularization impacts how we build. More fabrication of modular buildings occurs offsite, resulting in faster builds. This can be small (e.g., the stairs of a building) – to medium (e.g., entire sections of a building) – or the entire building itself! Entire modular skyscrapers have been constructed in the US; in fact, the world’s tallest modular high-rise was designed in NYC by SHoP Architects.
Join us on April 8th between 9:00 am – 12:15 pm CT as we learn how this is changing how we build and what it means for the future. This will build upon our lectures from Day One (emerging technologies on how we plan and design buildings) and Day Two (innovations in building products and materials) in our BuiltWorlds Buildings Conference!
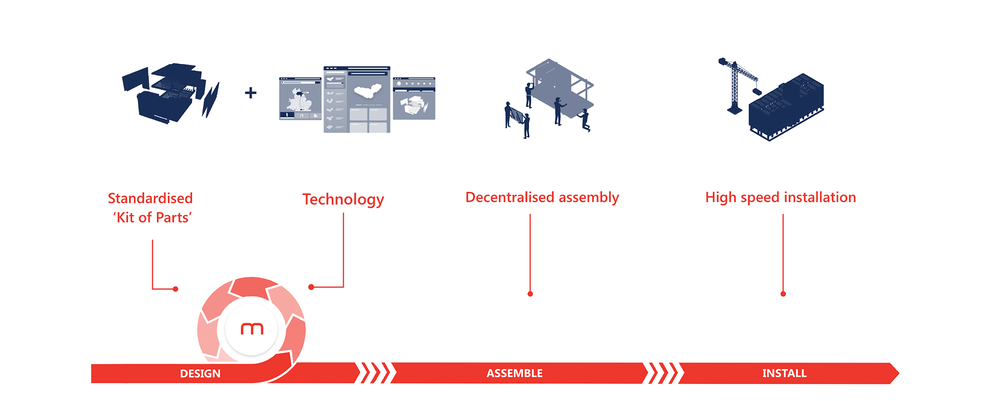
Meet the Experts
- Britton Langdon, CEO, MSuite
- Christopher Sharples, Founding Principal, SHoP Architects
- Aaron Holm, Co-CEO, Blokable
- Chris Mortenson, COO, Modulous
- David Hettinger, Founder & Principal, Entropy.Build
- Anil Sawhney, Programme Construction Lead, RICS
- Tim Jed, Supply Chain Leader, DPR Construction
Transforming How We Build Houses, Factories, Office Buildings, Data Centers, & More
Moving construction from jobsites and into factories has a significant impact on how we build. Modular building is a prefabricated process consisting of repeated sections called modules. Modular construction must be considered in all stages of a project’s lifecycle – from design to building erection. The key benefits to modular construction lay in reduced production times, leaner supply chains, and limiting redesigns.
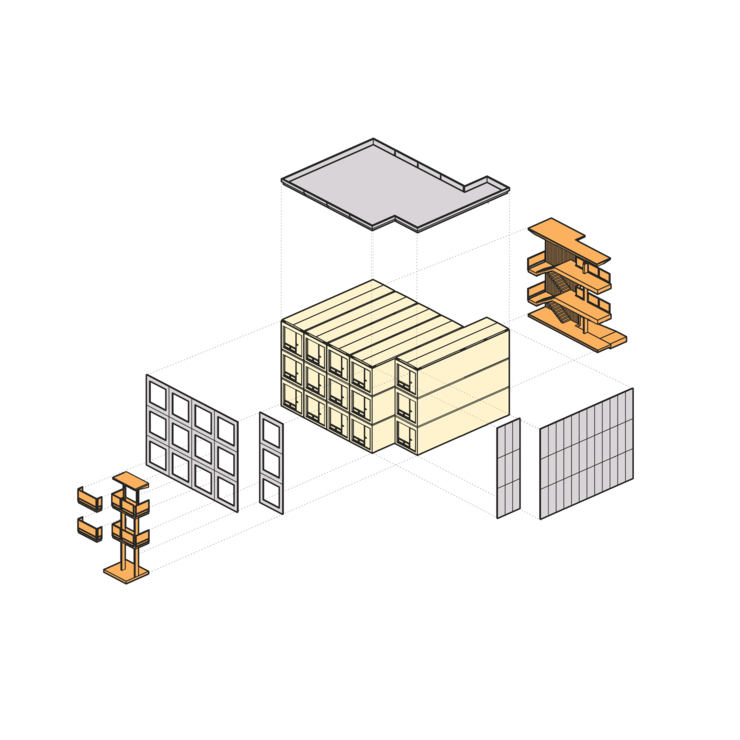
Fabrication, construction, and building erection can all be sequenced simultaneously for shorter project timelines as well. In fact, modular construction projects finish twice as fast, on average, compared to traditional construction techniques. Once on the jobsite, the reduction in customization, complexity, and RFIs allow construction workers to set modules in place, then lock them together to create a seamless building.
Modularity Must Be Considered from Design to Construction
Modular construction is optimized when considered throughout the project’s lifecycle. This starts with architects and engineers in design. Next, it moves towards fabrication with manufacturers optimizing their supply chain to align with project schedules. Finally, all logistics must be managed from jobsite delivery to construction.
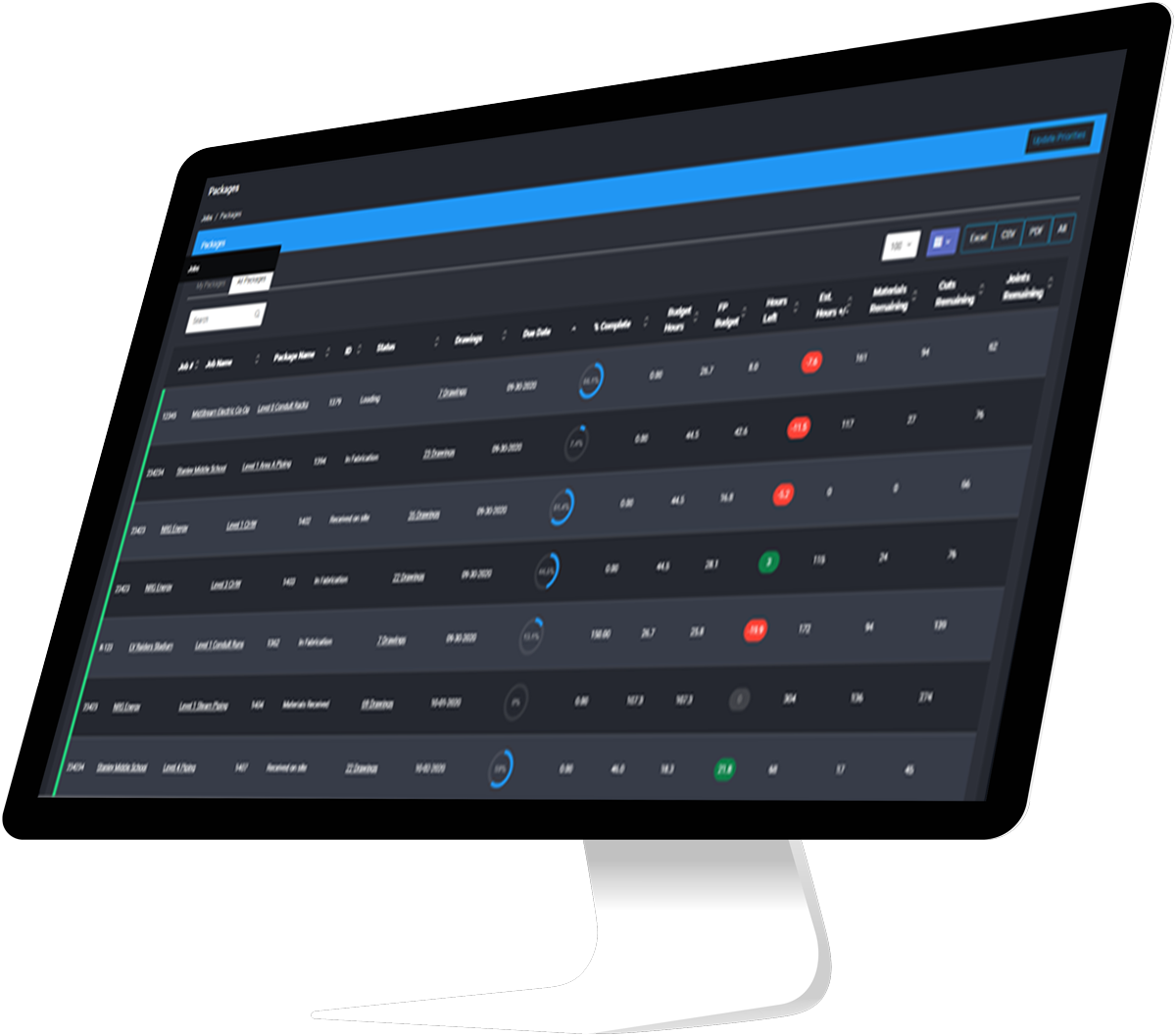
Discussion
Be the first to leave a comment.
You must be a member of the BuiltWorlds community to join the discussion.