In our May Construction Machines Research Report on the trends we follow under the Machines Category of topics, we noted that, despite generally low rates of adoption in the category (see chart below), Construction Equipment Management Software had achieved high ratings among the topics. Based on the finding from our Industry Benchmarking Program, we are able to identify several factors diving adoption as well as areas of opportunity for improvement in the sector.
We are now tracking more than thirty equipment tracking software solutions in our network company database, and we break down a few below.
Three Factors Fueling Maturing of The Sector, and One Driving Its Future:
I. Labor costs, skills shortages, Covid and other related complexities and the health of contractor backlogs are driving investment in machinery.
Our survey, completed just before the Covid Shutdown occurred, pegged more than 80% of survey respondents indicating that they would be increasing the size of their equipment fleet over the next two years. While Covid may have left the industry more cautious about capital expenditures, backlogs are still strong, and Covid has only added to the complexity of labor issues. As contractors invest more in tools and equipment, they also are interested in equipment management systems.
II. Contractors generally perceive the basic benefits of equipment management software.
Around 66% survey respondents believe their company has a firm understanding of telematics, and around 83% believed ‘equipment performance and use’ was the most valuable data made available through their use. The top three areas in which they see value from equipment management software are as follows:
- Vehicle Location & Identification – 6.9/10
- Providing Data on Equipment Usage – 6.1/10
- Insight into Equipment Health & Maintenance – 5.3/10
III. Solutions are rated moderately user friendly.
With an overall ease of use/user friendliness rating of 4.9 on a scaled of 1-10, solutions in the sector are definitely not loved by all. Project Document Management and Collaboration Software received a user friendliness rating of 7.0 on the same 1-10 scale, suggesting equipment management systems have a ways to go to be as accessible to users as other types of industry software. However, other types of software achieved lower rating, placing equipment management software roughly in the middle of the pack of industry solutions, based on “user friendliness” ratings.
IV. Integration With Other Contractor Systems: A Major Opportunity for Equipment Management Software Differentiation.
The place where equipment management systems score lowest we in the area of integration with Project Management, ERP, and other company solutions. Survey respondents in the Machines Survey gave integration a 4.3 out of 10. The response was even worse among respondents to the ERP and Project Management Survey they gave their technology a 3.5 out of 10 for integration with equipment management processes.
The suggestion here is that as basic functionality such as geolocation, usage monitoring, and maintenance needs become table stakes, differentiation in this topic area will be found as equipment management systems better integrate or extend their feature sets to other key functions. Even as systems developed specifically around telematics expand their offerings, we expect to see more systems developed to support rental/sales, project management, maintenance and other processes enter the sector.
Below is a look at twenty companies in the equipment management sector today. Looking at the emerging players as well as some of the traditionally project management-focused, rental, or maintenance players helpings suggest how the sector could evolve in the years to come:
- B2W Software – The company’s Maintain and Track Packages draw information from telematic data to track the maintenance process around heavy equipment. The system can track the location of equipment and also help create work orders, manage mechanic workloads, and schedule work orders.
- CatConnect – This system focuses a bit more on predictive diagnostics. As with other equipment management applications, it provides location and other data, but it also facilitates requesting of parts and service and scheduling of dealer support.
- Chetu – Chetu develops solutions for equipment management, including GPS tracking, tool tracking, and fleet telematics.

- Clue Insights – Tracks heavy equipment, crews, and other machinery all in one app and sends key recommendations directly to phones. It handles all the basic telematics and provides crew management features as well.
- Einsite – Uses AI to track and boost productivity in the mining and construction industries using a combination of cameras and sensors to automatically capture real-time data from the job site.
- EquipmentShare – Provides a range of equipment management solutions, from renting equipment to purchasing fleets to tracking assets with their proprietary advanced telematics platform.
- Komastu Komtrax – “Provided without fee to the owner of record,” the system comes standard on Komatsu equipment and can provide an array of data about equipment operations, maintenance, fuel usage, hours in use, and more. As with other manufacturer provided systems, Komatsu dealer support is also available.
- HCCS – HCSS offers a suite of software including HCSS Equipment 360 for maintenance, HCSS Telematics, FuelerPlus, and HCSS Trucking to provide its heavy construction customers complete set of solutions for fleet management.
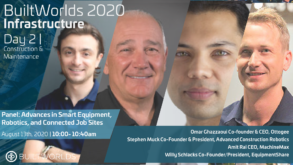
- MachineMax – Live reports of any machine, owned or rented, that helps finish projects on time with minimal overrun costs. MachineMax is one of the earlier stage players on this list. The company presented at our Demo Day this past spring (Machine Max BuiltWorlds Demo Event May 2020).
- Milwaukee Tools OneKey – More Tool and Smaller Equipment-focused, one key does boast some interesting features such as the ability to monitor charges of power tools and create rolls for different people involved with tools with different levels of permission to access tools. As the capability of this app expands, it would not be surprising to see more functionality in relation to larger equipment.
- OneView, from Pedigree Technologies– Provides all of the usual location, engine run time, geo-fencing to facilitate billing, maintenance, and usage optimization. Pedigree has integrated a camera view system into its suite and also a significant number of “on-road” features.
- Ottogee – Links people and equipment to optimize resource usage. Data collection emanates from their smart app and smart id badge wearables systems, and they suggest an ability to integrate with existing management systems or to fuel insights through their stand alone dashboard. Another emerging technology company, now part of Oracle’s Engineering and Construction Ecosystem, we’ll expect to see more tie-ins with other players in the group.
- Penta Technologies – As with other systems, Penta provides global location and usage data and also log maintenance histories and schedules. However, Penta adds project management and accounting features by integrating with project information to automate charging to projects. It can house and track charging rates, and it can also automate calculation of depreciation and book and tax valuations.
- PROCORE – In partnership with companies such as AHG Software, PROCORE offers an array of workflows related to equipment management and the possibility of tracking equipment on sight. The solutions within the PROCORE environment, setting aside the app marketplace, do not appear as robust at the present as with others, but that will likely change as PROCORE becomes more focused on the heavier parts of the construction market.
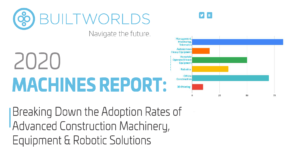
- Recon Dynamics – Recon is another of the players in the hardware sector, having created their own sensor system. They are also providing tool and equipment tracking. They have also introduced some really interesting technology for aerial lift safety, warnings when equipment is uneven, and line work safety, and materials management.
- SAP ETM – At least one larger contractor in the BuiltWorlds Membership leverages SAP in conjunction with partner software for equipment management. The SAP ETM site Indicates several other SAP applications as requisites for implementing ETM which suggests that, as with other, large software companies, there may be a higher degree of customization required to achieve the specific needs commonly addresses in other industry-specific solutions. However, for firms wanting to work with the large, well established players, there are definitely formulas out there.
- ShareMyToolbox – In a world where the trend is to track more and more things under one app, ShareMyToolbox is somewhat swimming against the trend with a bid for simplicity and a focus on tools. The app focuses on tracking the check out and check in of tools. Find tools, inventory tools, file insurance claims for lost tools, etc.
- Tenna – Integrates GPS, Cellular, Blue Tooth Low Energy and QR Technologies to enable tracking of mixed fleets, including heavy machinery, fleet, mid-sized equipment, and small tools. Features include utilization tracking, comparison of rental versus owned equipment, tracking of inspection and safety reporting, and location service.
- ToolWatch – ToolWatch provides location and management systems across equipment, tools, and materials. ToolWatch also boast integrations with CMiC, Computer Guidance, Sage, and Viewpoint, suggesting more potential for functionality related to accounting and project management.
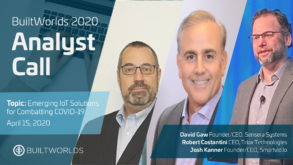
- Triax Technologies – Originally focused on tracking workers to promote safety, the folks at Triax have extended their “rugged” spot-r tagging technology to equipment, allowing site managers to collect data about their equipment and their people in one platform and opening up the possibility of added insights such as the ability to understand when people are in proximity of equipment or relate training and machinery.
Beyond these twenty solutions, there are many more, evidence of the initial state of maturity characterizing the sector. The table is now set for a phase of expanded and more robust features and functions than in the initial telematics-oriented offerings as well as acquisitions, consolidations, and integrations.
Discussion
Be the first to leave a comment.
You must be a member of the BuiltWorlds community to join the discussion.