In an industry that continues to evolve with impressive new technological innovations by the day, it shouldn’t be surprising that the time-consuming process of sending two employees and a tape measure to capture jobsite measurements might soon be replaced. Matterport, a California-based startup and a leader in immersive media technology, has created an elegant tool to facilitate that shift: the Pro2 3D Camera.
The Pro2 3D camera first gained market traction by showcasing homes for realtors. The immersive 3D experiences captured by the camera and delivered by Matterport’s software platform give homebuyers realistic virtual tours of potential new houses, allowing them to walk through bedrooms and check out the kitchen as if they are actually touring the home in person.
It wasn’t until a client tipped off Matterport that he was using their 3D camera to document construction sites that Matterport investigated its technology’s potential for architecture, engineering, and construction (AEC).
Seeking a more efficient and accurate approach to documenting construction than sending out a two-person team with a tape measure and/or camera, many AEC firms have turned to laser scanning technology. But the precision offered by laser scanning comes with a hefty price, and the technology is considered challenging to use.
Matterport’s Manager of Virtual Solutions, Daniel Prochazka, said his team quickly realized this. “The technology for capturing spaces is complicated, difficult, expensive, and not very visually engaging.” Matterport’s beautiful 3D camera atop a tripod remedies this long-standing issue. “Basically, you can take your jobsite back to your office,” Prochazka said.
Matterport discovered that the Pro2 houses several advantages AEC customers find enticing. It’s accurate down to a centimeter, which is precise enough for many project stakeholders. It’s relatively inexpensive with the camera costing just under $4,000, in addition to an equally cost-effective cloud subscription counterpart. Plus, the camera is fast, capturing a scan in 30 seconds or less, compared to the five-to-ten minute length for laser scans.
Bill Carney, the BIM Director for BSA Lifestructures, a national multidisciplinary design firm, was an early adopter of the technology. Carney discovered Matterport’s 3D camera after a friend sent him a link to the virtual tour of a construction site. He could not only see the site’s dimensions but where the gas lines were located. When he realized how easily the camera captured this hard-to-obtain yet valuable info, he said, “it was so cheap at the time, I was crazy not to try it.”
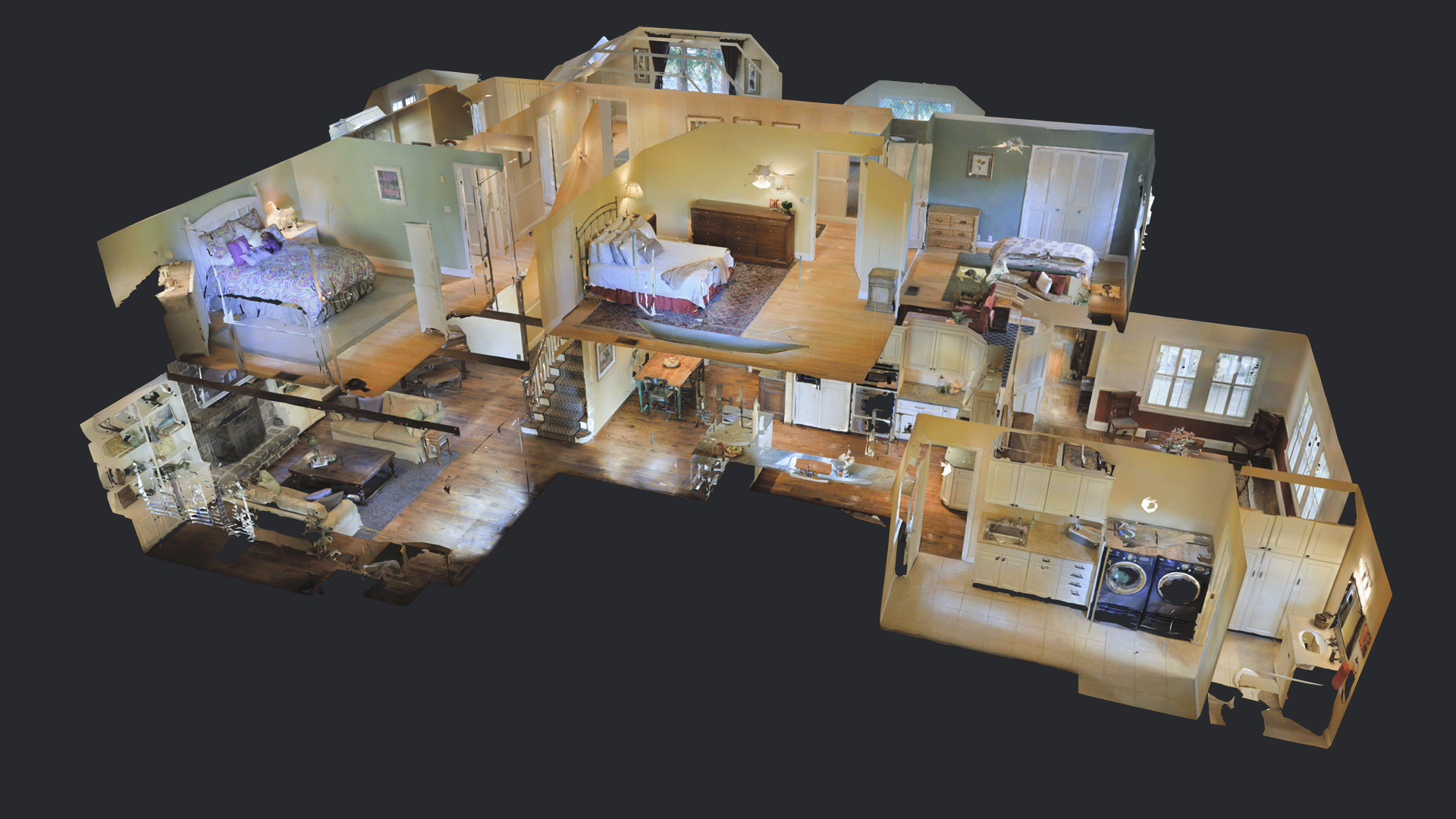
Since then, BSA has ditched the tape measures in favor of 3D capture and Matterport’s accompanying iPad apps. They’ve used the technology not only to document construction, “total gut jobs,” and renovations but also to create navigable records of user group spaces before they are moved. BSA also uses the technology to market their completed projects.
Carney appreciates that the 3D capture eases the costs, time, and headaches associated with project changes, like floor plan revisions. “Before, you’d have an old set of plans or a PDF,” said Carney. “But this allows you to do a 360 capture you can reference throughout the project.”
BSA’s experience with the Pro2, Carney believes, has made technology adoption throughout his firm much easier. Now that the technology has hit all levels, from senior managers to new hires, people are hooked. He said it drives more productive conversations about what’s the best use of technology on the site. “[The camera] has been a gateway drug for using more reality capture at our firm,” Carney affirms.
Mark Halavin, an architectural designer at the Florida-based engineering firm BRPH, which owns three Pro2 cameras, finds the technology particularly useful in renovations. BRPH often needs to design and model new systems, such as ductwork, that have to interface with existing systems. They use the Pro2 to verify that their modeling of the existing structure is accurate. “We can spend a few hours with the equipment scanning a space and get just about every field dimension that we possibly need in that short time,” Halavin said.
“[The camera] has been a gateway drug for using more reality capture at our firm.” – Bill Carney, BSA Lifestructures
“Matterport’s technology solves for the limitations of 2D photography and the need for manual measurements by providing the fastest, easiest and most affordable way to create, share, and collaborate around jobsites,” said John Chwalibog, Director of AEC at Matterport. “We can scan an entire site in a fraction of the time, cut down on jobsite visits, and document key milestones for any project at an affordable price point. That’s what makes this technology so disruptive.”
That disruption has been swift, too, with Matterport technology now available in every US state and over 75 countries around the world. From Los Angeles and Chicago to Madrid and Brussels, Pro2 3D cameras are being used to document floor plans, create virtual walkthroughs of spaces, and offer additional tools like photography and measurements. What used to be the ‘hard work’ is now one camera away from being completed in a single scan.
BuiltWorlds partnered with Matterport to bring you this article.
Discussion
Be the first to leave a comment.
You must be a member of the BuiltWorlds community to join the discussion.